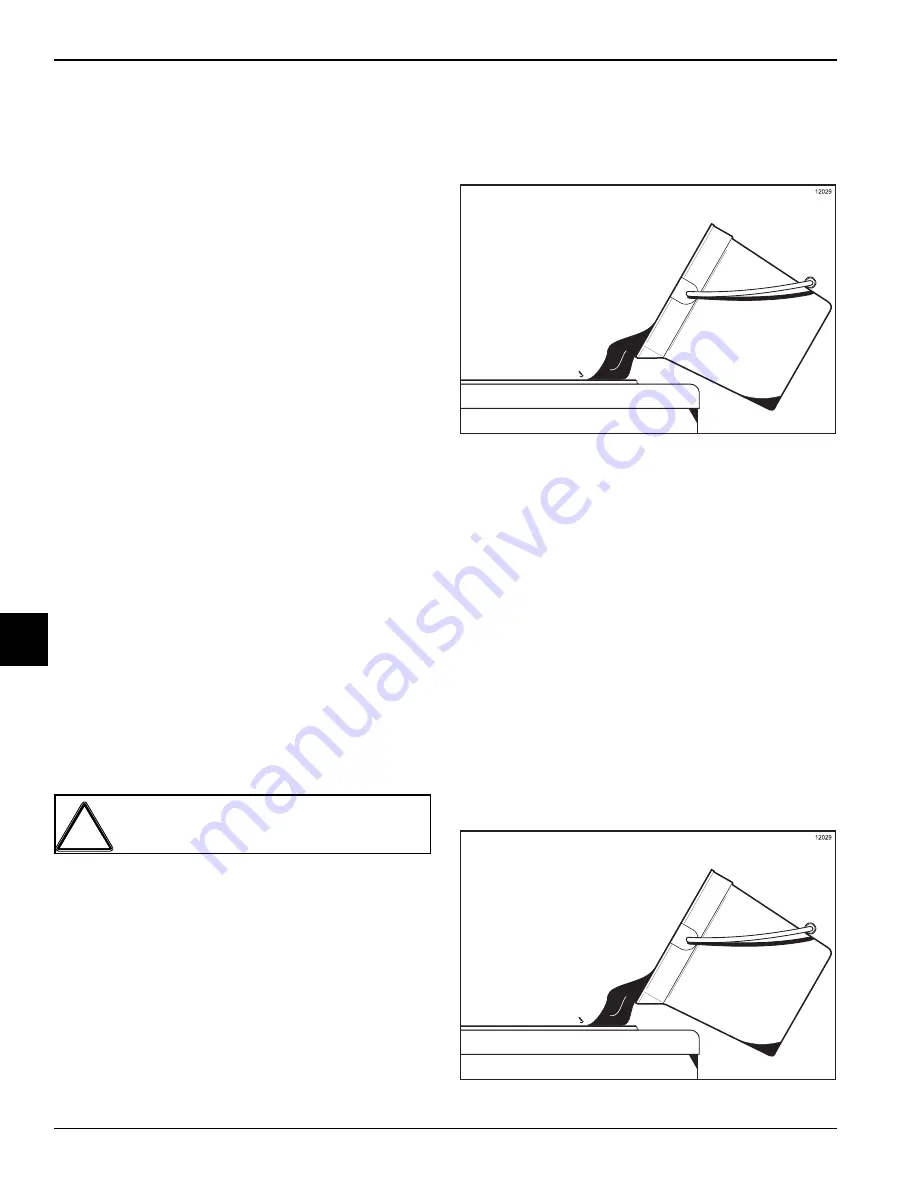
6-6
OPERATING PROCEDURES
Models C001 and C002
Operating Procedures
6
Closing Procedure
To disassemble your machine, the following items will be
needed:
•
Two cleaning pails
•
Cleaning brushes (provided with freezer)
•
Cleaner
•
Single-service towels
Draining Product From the Freezing
Cylinder
1. Place the FREEZE/CHILL and the HOPPER
REFRIGERATION switches in the OFF position.
2. Remove the flow regulator assembly, hopper covers,
gaskets, discharge chute and rear bearing drip pan.
Take these parts to the sink for cleaning in an
approved cleaning solution
(examples: Kay-5® or Stera-Sheen®).
3.
If local health codes permit the use of rerun,
place
a sanitized, NSF-approved stainless-steel rerun
container beneath the draw plate. Place the
DASHER switch in the ON position. Drain the
remaining product into the rerun container. When the
flow of product stops, place the DASHER switch in
the OFF position. Place the sanitized lid on the rerun
container and place it in the walk-in cooler.
Note: If local health codes do not permit the use
of rerun, the product must be discarded.
Follow
the instructions in the previous step, except drain the
product into a pail and properly discard the mix.
Repeat steps 1 through 3 for the other side of the
freezer.
Rinsing
1. With a pail beneath the draw plate, pour 2 gal. (7.6 L)
of
cool
, clean water into the mix hopper. With the
brushes provided, scrub the mix hopper.
Figure 6-17
2. Place the DASHER switch in the ON position. Agitate
for 5 minutes. Drain all the rinse water from the
freezing cylinder.
Repeat steps 1 through 2
until the water is clear.
3. Once all the rinse water has drained, place the
DASHER switch in the OFF position.
Repeat steps 1 through 3 for the other side of the
freezer.
Cleaning
1. Prepare an approved 100 ppm cleaning solution
(examples: 2-1/2 gal. [9.5 L] of Kay-5® or 2 gal.
[7.6 L] of Stera-Sheen®).
Use warm water and
follow the manufacturer’s specifications.
2. With the draw plate closed, pour the cleaning solution
into the mix hopper.
Figure 6-18
!
ALWAYS FOLLOW LOCAL HEALTH CODES.
Summary of Contents for C001
Page 22: ...5 4 USER INTERFACE Models C001 and C002 User Interface 5 Notes...
Page 36: ...9 2 PARTS REPLACEMENT SCHEDULE Models C001 and C002 Parts Replacement Schedule 9 Notes...
Page 40: ...10 4 LIMITED WARRANTY ON MACHINES Models C001 and C002 Limited Warranty on Machines 10 Notes...
Page 44: ...11 4 LIMITED WARRANTY ON PARTS Models C001 and C002 Limited Warranty on Parts 11 Notes...