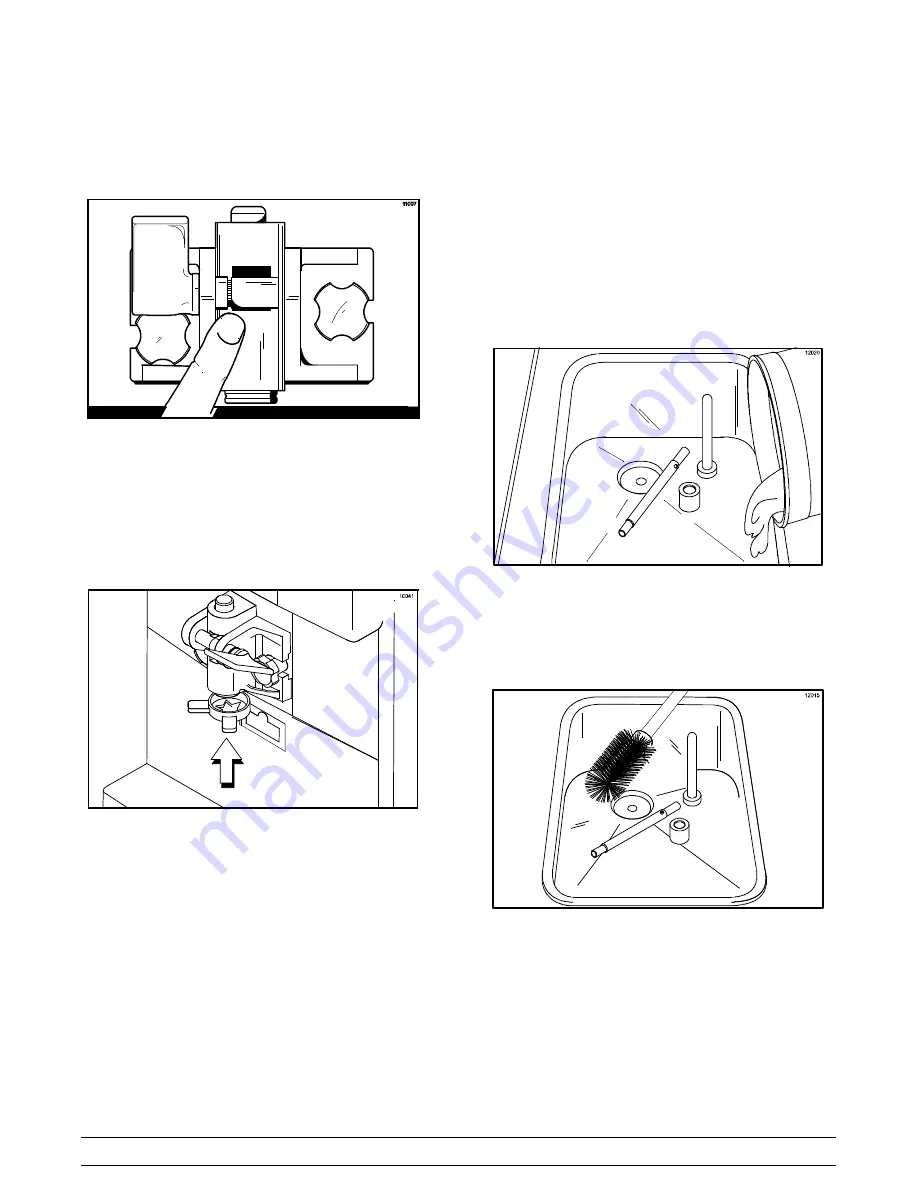
13
Model 142
Operating Procedures
090421
The illustration below shows the draw valve
assembled on the left side.
Figure 16
Step 9
Snap the design cap over the bottom of the freezer
door spout.
Figure 17
Step 10
Lay the feed tube and mix level float in the bottom of
the mix hopper.
Sanitizing
Step 1
Prepare a pail of an approved 100 PPM sanitizing solu-
tion (examples: 2- 1/2 gal. [9.5 liters] of Kay- 5
R
or
2 gal. [7.6 liters] of Stera- Sheen
R
). USE WARM WA-
TER AND FOLLOW THE MANUFACTURER’S SPE-
CIFICATIONS.
Step 2
Pour the sanitizing solution into the hopper and allow
it to flow into the freezing cylinder.
Figure 18
Step 3
While the solution is flowing into the freezing cylinder,
brush- clean the mix hopper, mix level float stem, mix
level float, mix inlet hole, and air tube.
Figure 19