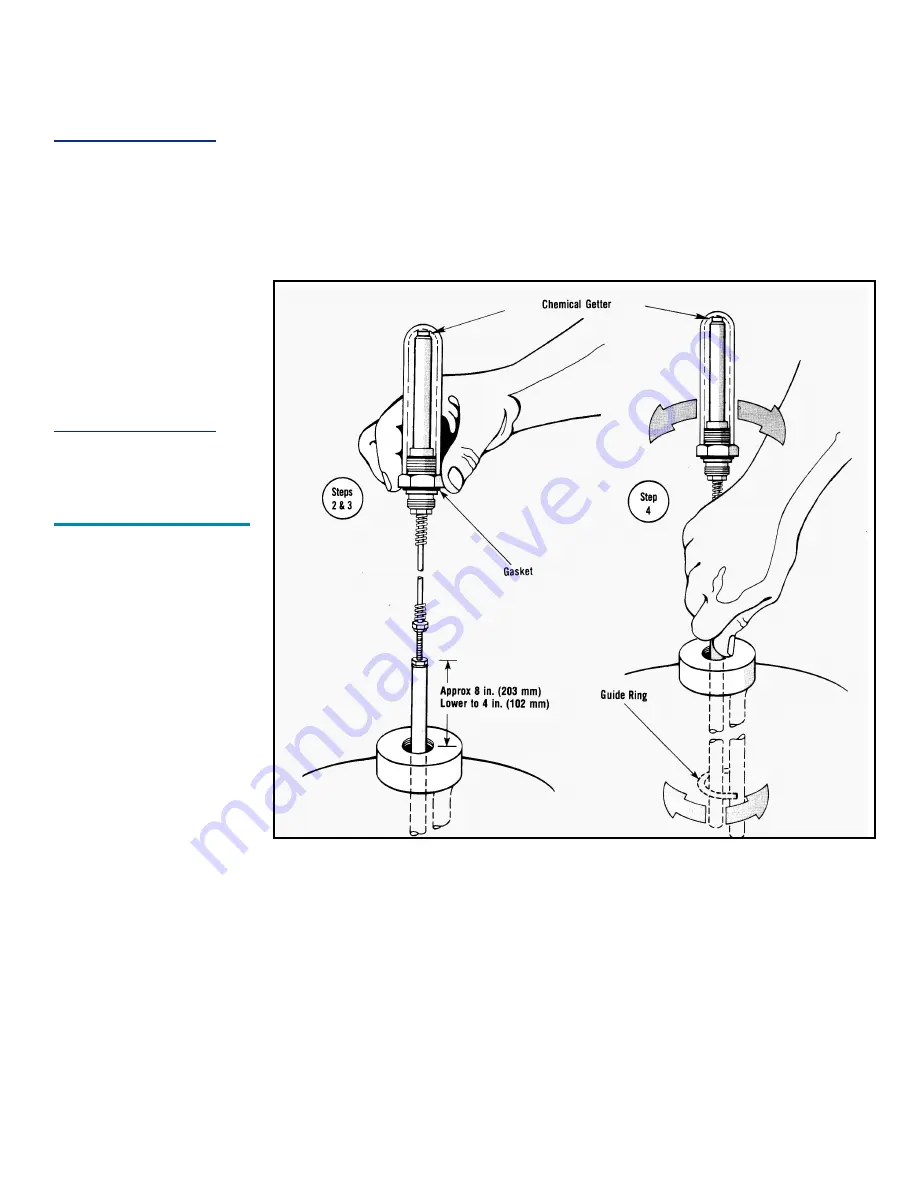
6. When you are satisfied that the float rod is correctly installed, lower the assembly the
rest of the way into the container until the top portion threads can be engaged.
7. Screw the gauge in place and hand torque to about 20 ft lbf (2.8 kgf m). Leak check the
connection of gauge body to the flange.
CAUTION:
When installing the
gauge assembly, care
must be taken to
ensure that the float
rod is inserted through
the guide ring
located on the liquid
withdrawal line inside
the container. If the
gauge does not
engage this ring, the
contents indication
will be inaccurate, or
the gauge may be
damaged in use.
Contents Gauge
Insertion
18