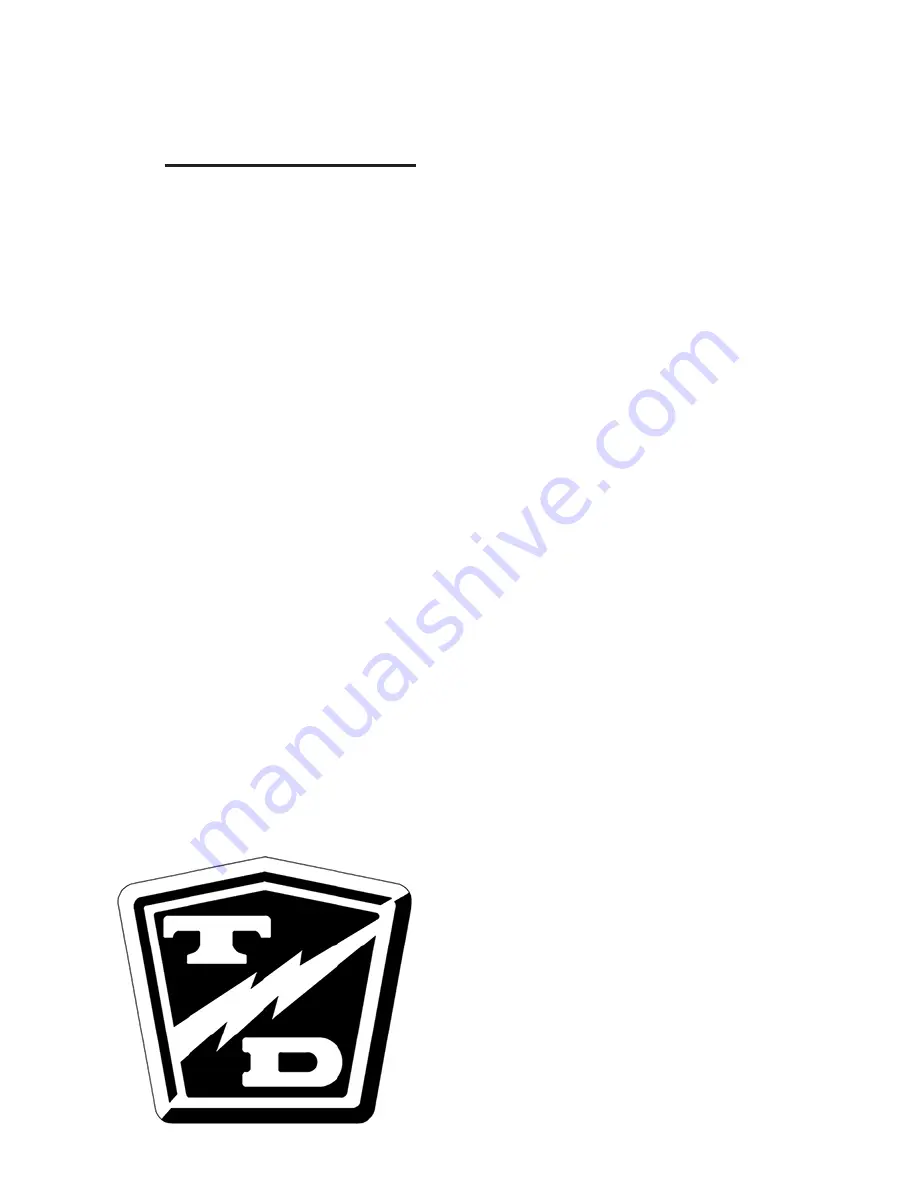
Table of Contents
Charger
Remove/Install .................................................2
Troubleshooting ..............................................2
Programming ...................................................3
Delta-Q ....................................................................3
Signet ......................................................................4
Delta-Q IC650 .........................................................5
Summary of Contents for AMB Ambulance
Page 2: ......
Page 6: ...TAYLOR DUNN...
Page 67: ...Maintenance Service and Repair Steering Page 21 Exploded View of Steering Gear...
Page 68: ...TAYLOR DUNN...
Page 110: ...Chargers Page 6 Notes...
Page 119: ...Maintenance Service and Repair Transmission Page 9 Rear Suspension...
Page 132: ...TAYLOR DUNN...
Page 154: ...TAYLOR DUNN...
Page 160: ...TAYLOR DUNN...
Page 172: ...TAYLOR DUNN...
Page 180: ...TAYLOR DUNN...
Page 182: ...Illustrated Parts Illustrated Parts Page 2 Front Axle...
Page 184: ...Illustrated Parts Illustrated Parts Page 4 Front Brakes 5 Brake Body Assembly...
Page 196: ...Illustrated Parts Illustrated Parts Page 16 Transmission B 2 00...
Page 200: ...Illustrated Parts Illustrated Parts Page 20 Transmission Differential Case B 2 10...
Page 204: ...Illustrated Parts Illustrated Parts Page 24 Rear Brakes B 2 10 8 Brake Body Assembly...
Page 206: ...Illustrated Parts Illustrated Parts Page 26 Motor...
Page 208: ...Illustrated Parts Illustrated Parts Page 28 Master Cylinder and Linkage...
Page 212: ...Illustrated Parts Illustrated Parts Page 32 Brake linkage parking brake B 2 10...
Page 216: ...Illustrated Parts Illustrated Parts Page 36 Wheels and Tires...
Page 222: ...Illustrated Parts Illustrated Parts Page 42...
Page 223: ...Illustrated Parts Illustrated Parts Page 43...
Page 224: ...Illustrated Parts Illustrated Parts Page 44...
Page 225: ...Illustrated Parts Illustrated Parts Page 45...
Page 228: ...Illustrated Parts Illustrated Parts Page 48 Batteries...
Page 230: ...Illustrated Parts Illustrated Parts Page 50 Seat Cushions Lights Deck and Frame 19 18...
Page 232: ...Illustrated Parts Illustrated Parts Page 52 Decals...
Page 234: ...Illustrated Parts Illustrated Parts Page 54 Fixed 2nd and 3rd Seat Option Hitches...
Page 244: ...Illustrated Parts Illustrated Parts Page 64 Sun Tops 2 3 4 5 6 1 7 8 9 9 10 11 12...
Page 246: ...Illustrated Parts Illustrated Parts Page 66 Automatic Driver Seat Brake B 2 10...
Page 248: ...Illustrated Parts Illustrated Parts Page 68 Optional Deckboards Illustration not available...
Page 258: ...TAYLOR DUNN...