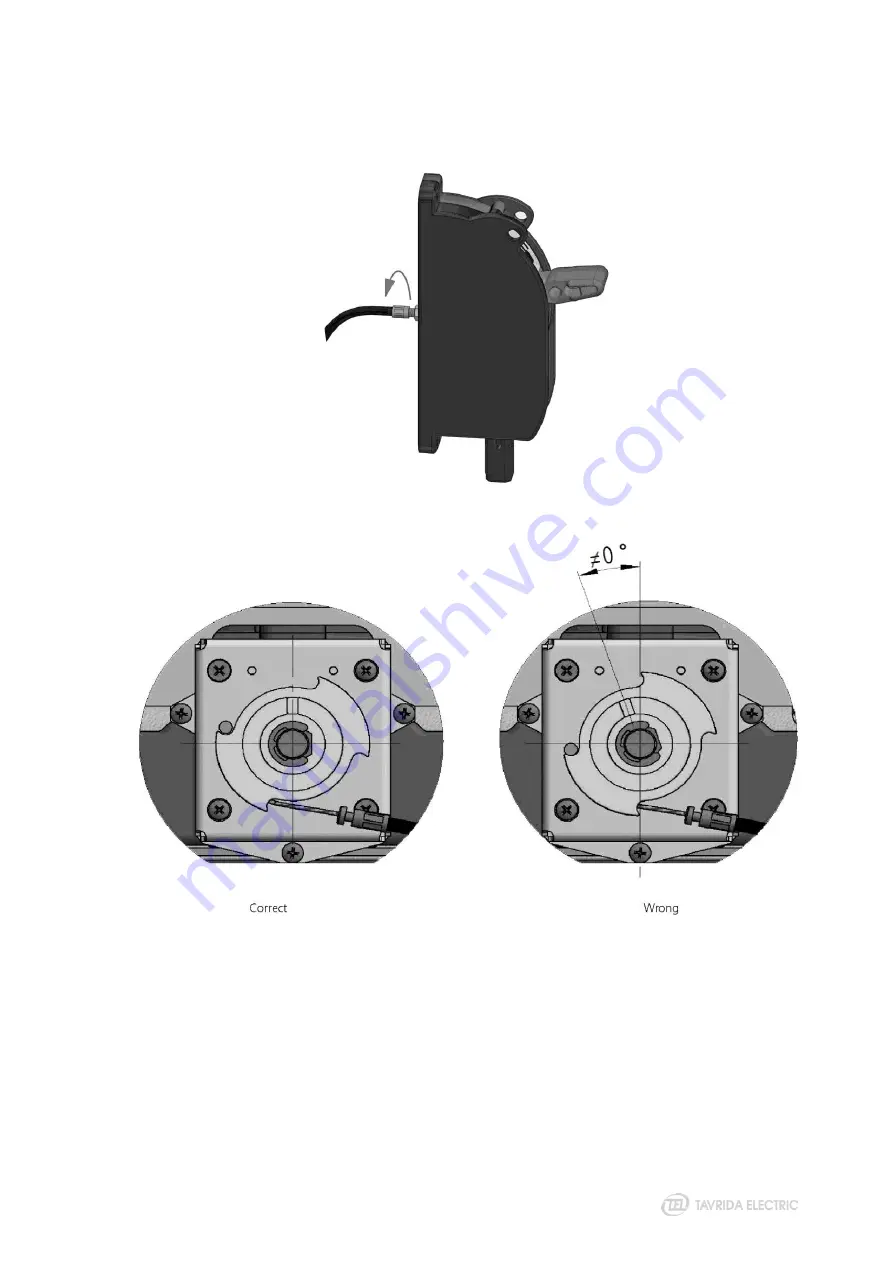
67
from the delivery kit of CBkit_Interlock_3. Alternatively StandDet_Screw_DIN7504-K(4.8_19_Fe-Zn) from the
delivery kit of CBkit_Interlock_3 can be used.
The flexible release cable shall be fixed in the Switchgear with help of StandDet_CableTie_LS(4.6_150_40)
from the delivery kit of CBkit_Interlock_3. If necessary the stroke of flexible release cable can be adjusted as
shown in the Figure 118.
Figure 118
Adjustment of stroke of flexible release cable
Figure 119
Position of interlocking shaft of the ISM with connected CBkit_Interlock_3
Connection of CBkit_Interlock_4 to ISM15_LD_8, MD_1, MD_3, Shell_2,
HD_1 interlocking shaft
CBkit_Interlock_4 can be used with the ISM15_LD_8, ISM15_MD_1, ISM15_MD_3 and ISM15_HD_1 as an
accessory for manual trip / lockout of the ISM by rotary switch. CBkit_Interlock_4 can be used with the
ISM15_Shell_2 via CBkit_Interlock_8.
Summary of Contents for VCB Series
Page 1: ...COMPATIBLE SERIES USER GUIDE...
Page 2: ......
Page 4: ......
Page 5: ...1 Product description...
Page 13: ...13 2 Nameplates and seals...
Page 18: ...18 3 Product handling...
Page 37: ...4 Installation...
Page 87: ......
Page 88: ...5 Commissioning...
Page 94: ...94 Figure 155 The connection points of the contact resistance meter...
Page 95: ......
Page 96: ...6 Operation...
Page 100: ...7 Maintenance and troubleshooting...
Page 105: ......
Page 106: ...8 Disposal...
Page 109: ...109 Appendix 2 Overall Drawings...
Page 112: ...112 ISM15_LD_3 Weight 13 kg ISM15_LD_6 PCD 133 mm Weight 55 kg...
Page 113: ...113 ISM15_LD_8 PCD 210 mm Weight 26 kg...
Page 114: ...114 ISM15_MD_1 150_L PCD 150 mm Weight 33 kg ISM15_MD_1 210_L PCD 210 mm Weight 35 kg...
Page 115: ...115 ISM15_MD_3 Weight 13 kg ISM15_Shell_2 150_L PCD 150 mm Weight 51 kg...
Page 120: ...120 ISM15_HD_1 275 PCD 275 mm Weight 72 kg ISM25_LD_1 210_Par2 PCD 210 mm Weight 36 kg...
Page 123: ...123 ISM25_LD_2 2 PCD 150 mm Weight 37 kg ISM25_LD_3 Weight 14 kg...
Page 125: ...125 Dimensions of Control Module CM_16_1 Par1_Par2_Par3_Par4_Par5 Weight 1 kg...
Page 127: ...127 Dimensions of Interlocking Kits CBkit_Interlock_1 CBkit_Interlock_3...
Page 128: ...128 CBkit_Interlock_4 CBkit_Interlock_5...
Page 129: ...Appendix 3 Secondary Schemes...
Page 130: ...130...
Page 131: ...131...
Page 132: ...132...
Page 133: ...133...
Page 134: ...134...
Page 135: ...135...
Page 136: ...136...
Page 137: ...137...
Page 138: ...138...
Page 139: ...139...
Page 140: ...140...
Page 142: ...Bartlett...