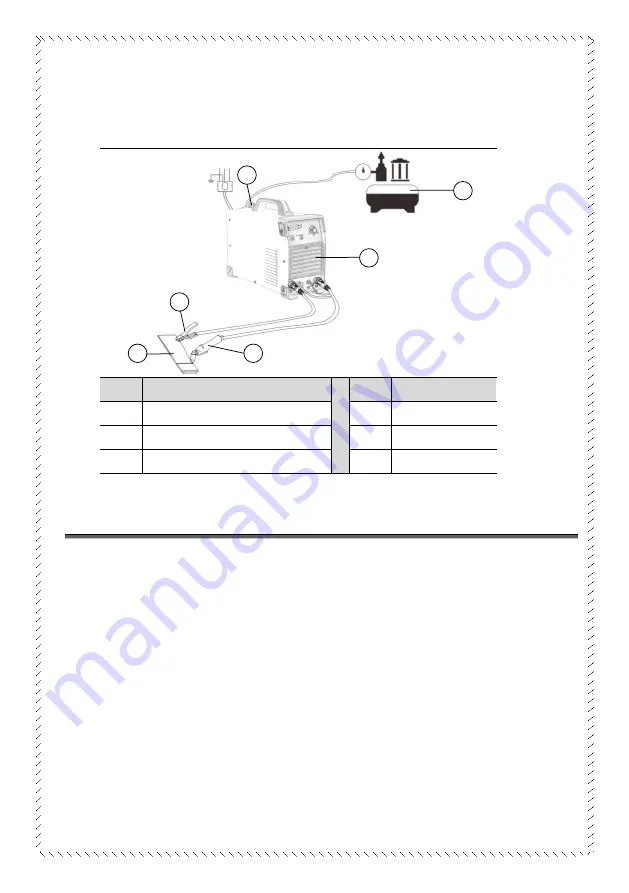
-
16
-
the rear panel of the machine. Then switch off the power at the main
distribution box.
2. Schematic Diagram of Cutting Machine
No.
Item
No.
Item
1
Cutting power supply
4
Earth clamp
2
Air pressure reducing valve
5
Workpiece
3
Air compressor
6
Torch
Maintenance
Safe operation of the machine is dependent on regular maintenance and the
replacement of worn and defective parts where necessary.
1. Daily Precautionary Checks:
1.1. Abnormal vibrations, sounds or odours.
1.2. Signs of overheating on cable connections.
1.3. Smooth fan operation.
1.4. Power switch efficiency.
1.5. Proper cable connection, insulation and damage.
1.6. Cable integrity and insulation.
3
2
4
5
6
1