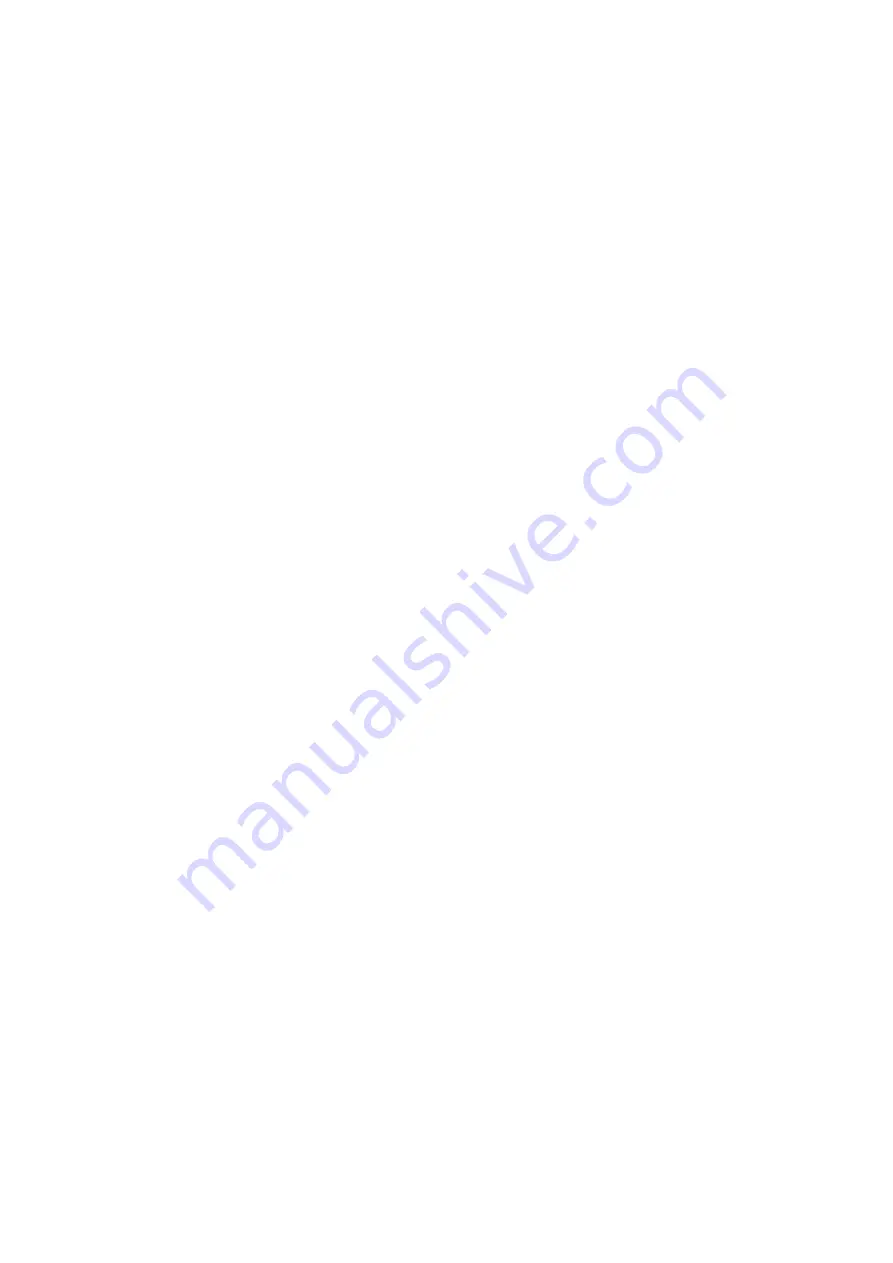
6-13. Spot Killer Circuit
The spot killer circuit is included, in order to eliminate damage of the CRT while switching
power on or off. The -225V is obtained from the voltage on pin7 of T440 via D489. When power
is on both +75V and -150V will charge on C349 via D349, at this moment Q348 is off. When
power is off, the positive end of C348 is ground and Q348 is on, -225V is fed to G1 via Q348,
R348A, and D357 cutoff the beam current.
6-14. Brightness Control Circuit
The brightness control of the monitor is achieved by changing the G1 voltage via Q495, Q497.
The control voltage is derived from the pin 26 of I501; the variation of the DC voltage on the base
of Q495 via R492 will vary the G1 voltage via R498.
6-15. Blanking Circuit
The vertical blanking pulse is produced from pin5 of I330 via R337, C337, R338 R339, R340,
and D338. It is also combined with horizontal blanking signal via network R342, C342. Both of the
signals are fed to the amplifier Q341, Q353. This blanking signal is fed to G1 via C355.
6-16. Horizontal Position (Raster) Circuit
The adjustable horizontal raster centering is achieved by using the circuit of D485, D486, and
R485 by adjusting P402 in either a DC current element flow in or flow L485 out the yoke assembly.
The background raster should be centralized with respect to edging to the bezel during the
procedure setting up.
6-17. HV. B+ Control Circuit
This circuit generates the supply voltage for the horizontal scanning circuit. This supply voltage
is approximately proportion to the H frequency in order to keep the scanning amplitude constant
when the horizontal frequency changes. The circuit is a step-up converter and it uses the current
mode regulation principle.
The feedback signal is derived from pin 9 of T440 via R405, R443 and R325A Peak-detected by
C451, R451, is fed to the error amplifier on pin 15 of I401. The value of R325 is chosen to get a
suitable gain for the error amplifier. A saw-tooth waveform signal related to the output current of
Q440 is fed to pin16 of I401 via R442, R440 and C326.
Both of the feedback and saw-tooth waveform signals are fed to a comparator in I401 to generate
a PWM (Pulse Width Modulation) control signal output pin28 of I401.