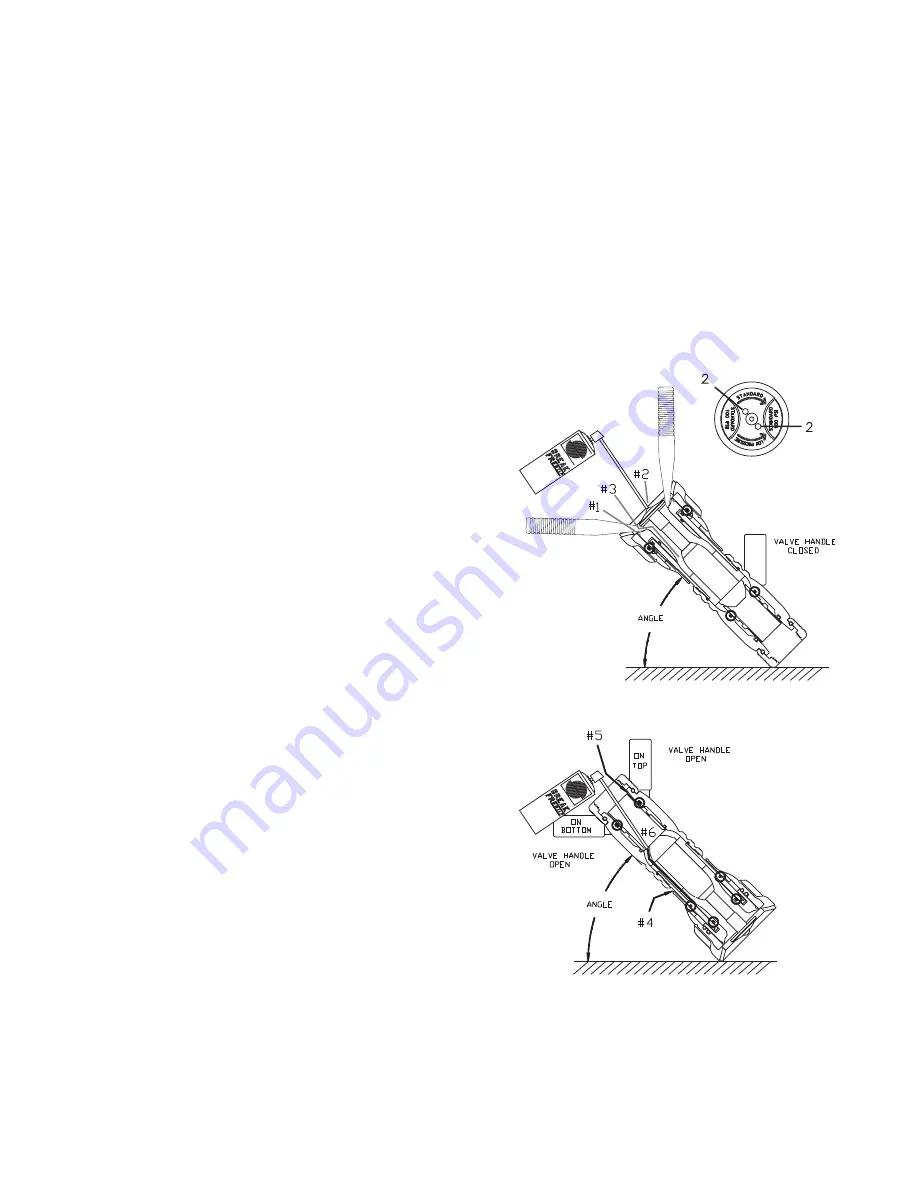
©Copyright Task Force Tips, Inc. 2002 - 2015
LIN-035 June 16, 2015 Rev15
24
11.0 MAINTENANCE
TFT nozzles are designed and manufactured to be damage resistant and require minimal maintenance. However, as the primary
fi refi ghting tool upon which your life depends, it should be treated accordingly. Do not drop or throw equipment.
11.1 FIELD LUBRICATION
All Task Force Tip nozzles are factory lubricated with high quality silicone grease. This lubricant has excellent washout resistance and
long term performance. If your department has unusually hard or sandy water, the moving parts may be affected. Foam agents and
water additives contain soaps and chemicals that may break down the factory lubrication.
The moving parts of the nozzle should be checked on a regular basis for smooth and free operation, and signs of damage. IF THE
NOZZLE IS OPERATING CORRECTLY, THEN NO ADDITIONAL LUBRICATION IS NEEDED. Any nozzle that is not operating
correctly should be immediately removed from service.
The fi eld use of Break Free CLP (spray or liquid) lubricant will help to restore the smooth and free operation of the nozzle. However,
these lubricants do not have the washout resistance and long-term performance of the silicone grease. Therefore, re-application of
Break Free CLP will be needed on a regular basis. CAUTION: Aerosol lubricants contain solvents that can swell O-Rings if applied
in excess. The swelling can inhibit smooth operation of the moving parts. When used in moderation, as directed, the solvents quickly
evaporate without adversely swelling the O-Rings.
The nozzle can be returned to the factory for a complete checkup and re-lubrication with silicone grease
PART ONE — COUPLING DOWN
Position the nozzle at a 45-degree angle with the COUPLING end down.
CLOSE the valve handle and set the pattern to STRAIGHT STREAM. Then
spray a short burst into these areas:
#1 FRONT PATTERN CONTROL SEAL
Spray in between the pattern control and the barrel.
#2 PRESSURE CONTROL UNIT
Place check sticks behind baffl e while shaper is in fl ush. Cycle baffl e in and
out using check sticks several times to work lubrication into o-rings.
#3 FRONT SLIDER SEAL
a) Rotate shaper into FLUSH position.
b) Spray down the front end of the nozzle to dribble lubricant into the
clearances between the shaper and the valve body.
Spray into holes
Dual pressure nozzle
While holding nozzle at the angle, wait 30 seconds for the lubricant to penetrate into the clearances. Cycle the valve handle and
rotate the shaper from straight stream to full fl ush several times, and then proceed to the next section.
PART TWO — COUPLING UP
Position the nozzle at a 45-degree angle with the BUMPER end down.
OPEN the valve handle and set the pattern to FLUSH. Spray a short burst
in these areas:
#4 REAR SHAPER SEAL
Spray down the clearance between the label and the shaper guide.
#5 REAR SLIDER SEAL
Spray into the clearance between the slider and the valve body.
#6 FLUSH MECHANISM SEAL
a) With the handle on the top, spray down into the nozzle. The aerosol
extension tip will help direct the spray into clearances leading to the O-Ring.
b) Rotate nozzle so the valve is on the bottom and spray another short burst.
#7 DETENTS IN THE HANDLE
Spray a small amount on the detent followers located in the handle.
While holding nozzle at the angle, wait 30 seconds, then cycle the valve handle several times. Rotate the pattern control from straight
stream to full fl ush several times. The pattern control should move freely and easily. The barrel cone should move forward to within
1/16” of the baffl e before the shaper reaches straight stream position. Wipe off excess lubricant.
IF THIS PROCEDURE DOES NOT RESTORE SMOOTH AND FREE OPERATION OF ALL THE MOVING PARTS,
THEN FACTORY SERVICE IS NEEDED. • 24-HOUR HOT LINE — 800-348-2686 • www.tft.com