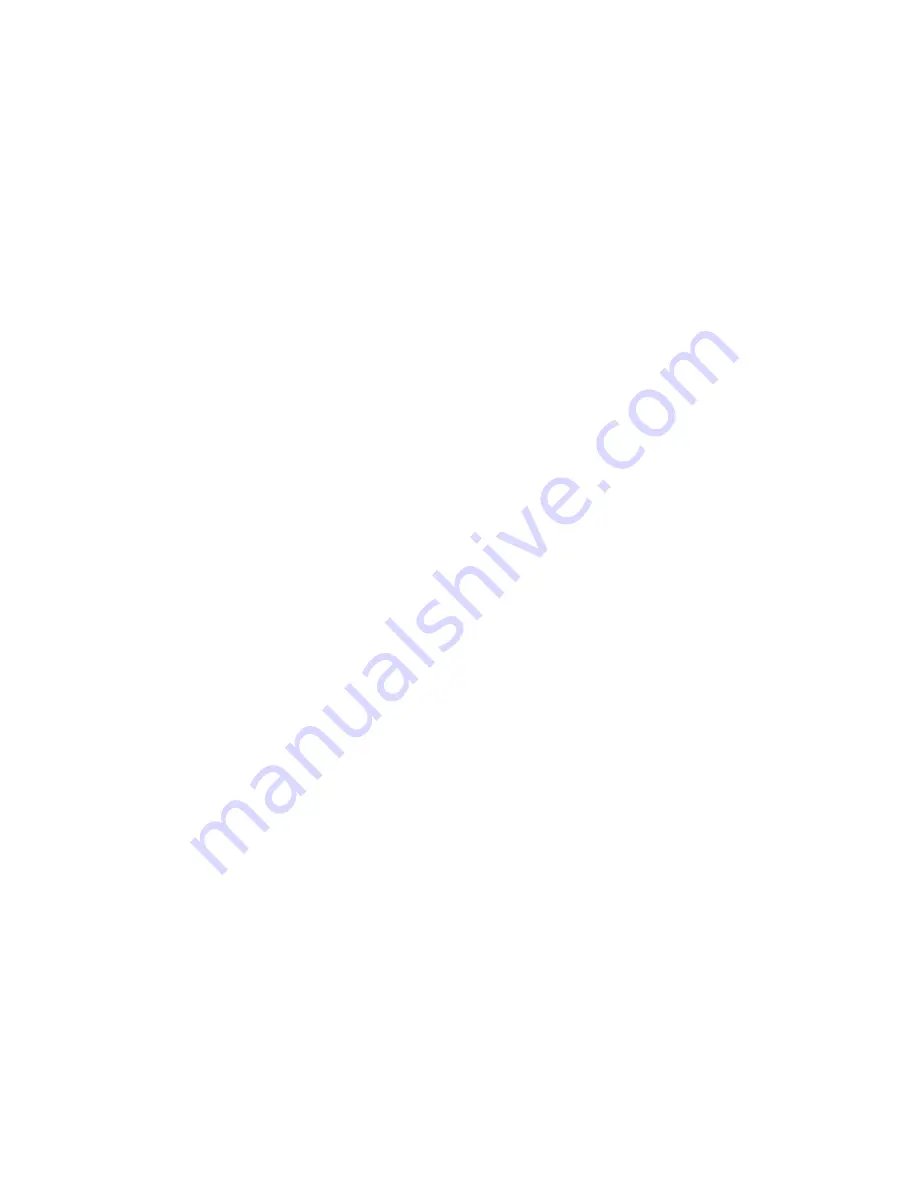
©Copyright Task Force Tips, Inc. 2003 - 2010
LIH-020 September 25, 2010 Rev06
2
BOLT-ON PISTOL GRIP REMOVAL: PISTOL GRIP [19v] is held on by a SOCKET
HEAD CAP SCREW [21v]. Remove screw with a 5/16” Ball Driver Allen wrench. To
reinstall, clean thread and apply Loctite® #271. Tighten screw to 95 in-lbs.
VALVE PLUG REPLACEMENT: After removing back end, VALVE PLUG [17v, 10b,
or 24b] is removed by pulling straight back. New valve plug can be installed using
a mallet.
VALVE SHUTOFF ADJUSTMENT: Shutoff valve is adjusted by the threads be-
tween the valve body and the front end of the nozzle. While holding the VALVE
HANDLE [3v] against stops in the OFF position, screw front end into the valve body
until contact is made with the VALVE PLUG [17v]. Open handle to ON position to
remove contact. Screw the front end in 1/12 turn further to give the valve shutoff
compression. Thread in both SET SCREWS [12v] until they bottom out, without
applying pressure. In an alternating fashion continue turning in set screws until tight.
VALVE ADJUSTMENT FOR SEVERE COLD: To help prevent hose line freezing
in cold climates, the valve may be adjusted for intentional leakage by unscrewing
the front end slightly. The valve may then be returned to normal adjustment for
complete shut off during warm weather as stated above.
SLIDE VALVE DISASSEMBLY SEQUENCE
HANDLE REMOVAL: Remove both BUTTON HEAD CAP SCREWS [6v] from
VALVE HANDLE [3v] using a 7/32” Allen wrench. Slide CAM and SAFETY PINS
[4v and 5v] out of handle by gently prying about 3/8” apart the handle and the valve
body using a fl at screw driver. To remove the handle, pull upwards while containing
the DETENT BALLS [7v] and SPRINGS [8v] to prevent their loss. Service to interior
valve parts should be done prior to reinstalling handle.
SLIDER AND SEAL REMOVAL: Remove #10-32 x ¼” SOCKET SET SCREWS
[12v] from the VALVE ASSEMBLY [11v] using a 3/32” Allen wrench. Unscrew front
portion of nozzle from valve. SLIDER [15v] can now be pulled out from the front of
valve. Remove and inspect O-RINGS [13v, 14v and 16v]. Replace O-Rings if they
are damaged.
SLIDE VALVE ASSEMBLY SEQUENCE
SLIDER AND SEAL INSTALLATION: Insert O-RINGS [13v, 14v and 16v] into
the proper grooves in the valve body. Check SLIDER [15v] for any raised metal at
groove area. Replace if necessary. Lubricate O-Rings and slider with DOW #112
Lube. Push slider into the valve body.
HANDLE INSTALLATION: Insert DETENT SPRINGS [8v] and DETENT BALLS
[7v] into the handle lugs. While holding balls in place, snap the HANDLE [3v] into
place with offset holes FORWARD. Carefully align the groove on SLIDER [15v] with
offset hole in VALVE DISCS [9v] and with offset hole in handle. Slide SAFETY PIN
[5v] into offset hole in handle. Push down into engagement with groove in slider,
until head of pin is fl ush with handle. Repeat procedure for CAM PIN [4v]. Insert
BUTTON HEAD SCREWS [6v] through the lower handle holes. Thread each into
corresponding center trunnion hole. Tighten HANDLE SCREWS [6v] securely with
a torque value of 100 in-lbs (11.3 N m). Handle should click fi rmly and smoothly into
all detent positions and the slider should move back and forth smoothly. The force
to move handle should be between 5 lbs and 13 lbs applied at top center of handle.
FRONT END
SHELL SERVICE PROCEDURE
SHAPER REMOVAL: The rubber bumper is permanently bonded onto the stream
shaper as a single unit referred to as the SHAPER [10f]. The shaper is attached
to the SHAPER GUIDE [4f, or 5f] by a threaded joint that is retained by Loctite®
#271. Grip rear portion of the nozzle in a vise with padded jaws, or clamp SHAPER
GUIDE [4f, or 5f] using TFT special tool TH502 held in a vise. Direct a hot narrow
fl ame around the rear portion of the shaper and heat for approximately 20 seconds.
Damage to BUMPER [10f] and LABELS [1f, 2f, or 6f] can be reduced by protecting
them with a wet cloth. Use a strap wrench to unscrew the shaper from the shaper
guide. Remove the shaper. Inside the shaper are (48) 13/16” ACETAL BALLS [8f],
some of which may fall free as the Shaper is removed. If Shaper is to be reused,
clean ball track and replace 336 O-RING [9f] if damaged.
SERVICE TO CAM GROOVES AND BALLS: When Shaper is removed, check
to see if the stream shaping GUIDE BALLS [3f] and CAM GROOVES [7f - part of
BARREL CONE ASSEMBLY] are damaged. Replace Balls if sheared or missing. If
the CAM GROOVES are badly damaged, the BARREL CONE ASSEMBLY should
also be replaced.
BARREL CONE ASSEMBLY SERVICE: This assembly is permanent and cannot
be taken apart. Check to ensure that the fl ush spring is not damaged by pushing
down on the Barrel Cone with both hands (about 50 lbs force). The Barrel Cone
Assembly should be replaced if the Barrel Cone does not push down or spring back
up by itself. Lightly grease the CAM GROOVES before re-installing the SHAPER
GUIDE.
SHAPER INSTALLATION: Install 336 O-RING [9f] in front groove of SHAPER
[10f]. Grease the seal and ball groove heavily. Place (48) 13/16” ACETAL BALLS
[8f] into greased ball groove. Apply Loctite® #271 to male thread on SHAPER
GUIDE [4f, or 5f]. Start shaper onto SHAPER GUIDE threads. Place three SHAPER
GUIDE BALLS [3f] into the grooves on barrel and screw down shaper until threads
bottom out.
PRESSURE CONTROL SERVICE PROCEDURE
Tools Required:
1/4 Allen wrench (10” Long)
1/4 Allen wrench (regular length)
Mallet
PRESSURE CONTROL REPLACEMENT: The pressure control may be removed
and replaced as a unit by following the procedure in the PRESSURE CONTROL
REMOVAL and INSTALLATION AND INITIAL OPENING ADJUSTMENT sections.
NOTICE: The Pressure Control Unit is part of the BARREL ASSEMBLY [7f]. This
unit is factory calibrated and sealed. Service on this unit is best performed at the fac-
tory using special tooling and equipment. In the unlikely event that this unit should
need service, it is highly recommended that you return the complete nozzle to the
factory for repairs OR replace the entire PRESSURE CONTROL UNIT. DO NOT
ATTEMPT TO DISASSEMBLE THE PRESSURE CONTROL UNIT! Task Force Tips
will assume NO liability for damage or injury resulting from attempts to disassemble
or repair the Pressure Control Unit.
PRESSURE CONTROL REMOVAL: To remove the CONTROL UNIT fi rst separate
the front end from the nozzle, then remove the VALVE PLUG (106, 24b or 17v).
Loosen and remove the shaft locking SCREW (1p) with a 3/16 allen wrench. Insert
a 7/32 Allen wrench into the front of the shaft and screw the shaft out of the barrel
assembly. LOCKING SLEEVE (2p) is removed by pushing it forward and out of
BARREL ASSEMBLY (7f) with a punch. Note: LOCKING SLEEVE may require light
tapping with a hammer to remove.
PRESSURE CONTROL INSTALLATION AND INITIAL OPENING ADJUSTMENT:
To install the CONTROL UNIT, lightly grease I.D. and O.D. of locking sleeve and
also threads of the screw. Place LOCKING SLEEVE (2p) with hollow end forward
onto back of shaft, thread fi nger tight. Note: If old LOCKING SLEEVE is reused it
may require light tapping with a hammer and punch to install. Screw CONTROL
UNIT (with pressure control parts installed) into barrel assembly. Insert a 7/32 Allen
wrench into front of shaft and turn in until baffl e just touches BARREL CONE (7f)
then turn back between ½ and 3/4 of a turn (opening gap of .026/.036 inches or
.66/.91mm). Keep Allen wrench in shaft to assure that shaft doesn’t turn and tighten
screw against locking sleeve, to approximately 180 in-lbs.
IMPORTANT: Always fl ow test after adjusting. Nozzle pressure and fl ow require-
ments are shown on the following table:
INITIAL OPENING at 40 PSI (2.8 BAR)
FLOW (MIN)
FLOW (MAX)
Opening Gap (REF)
38 GPM
58 GPM
.026/.036in
(144L/MIN)
(204 L/MIN)
(.66/.91mm)
NOZZLE PRESSURE NOZZLE PRESSURE
AT 95 GPM
AT 250 GPM
100 PSI MODEL
85 PSI +/- 6
99 PSI +/- 6
75 PSI MODEL
60 PSI +/- 6
80 PSI +/- 6
DUAL-FORCE KNOB REMOVAL: To remove the DUAL-FORCE KNOB [8p] from
the BAFFLE [4p]:
1) Turn knob to standard setting.
2) Turn the SHAPER [10f] back to full fl ush.
3) Insert a small probe (such as a 1/16” drill bit) into the smaller of the two holes on
top of the knob.
4) Simultaneously push down with probe while turning knob clockwise (when
viewed from the front). Once knob turns a little, the probe may be removed.
5) Turn knob clockwise until it hits a stop. (about 25 degrees).
6) Pull knob to remove from baffl e.