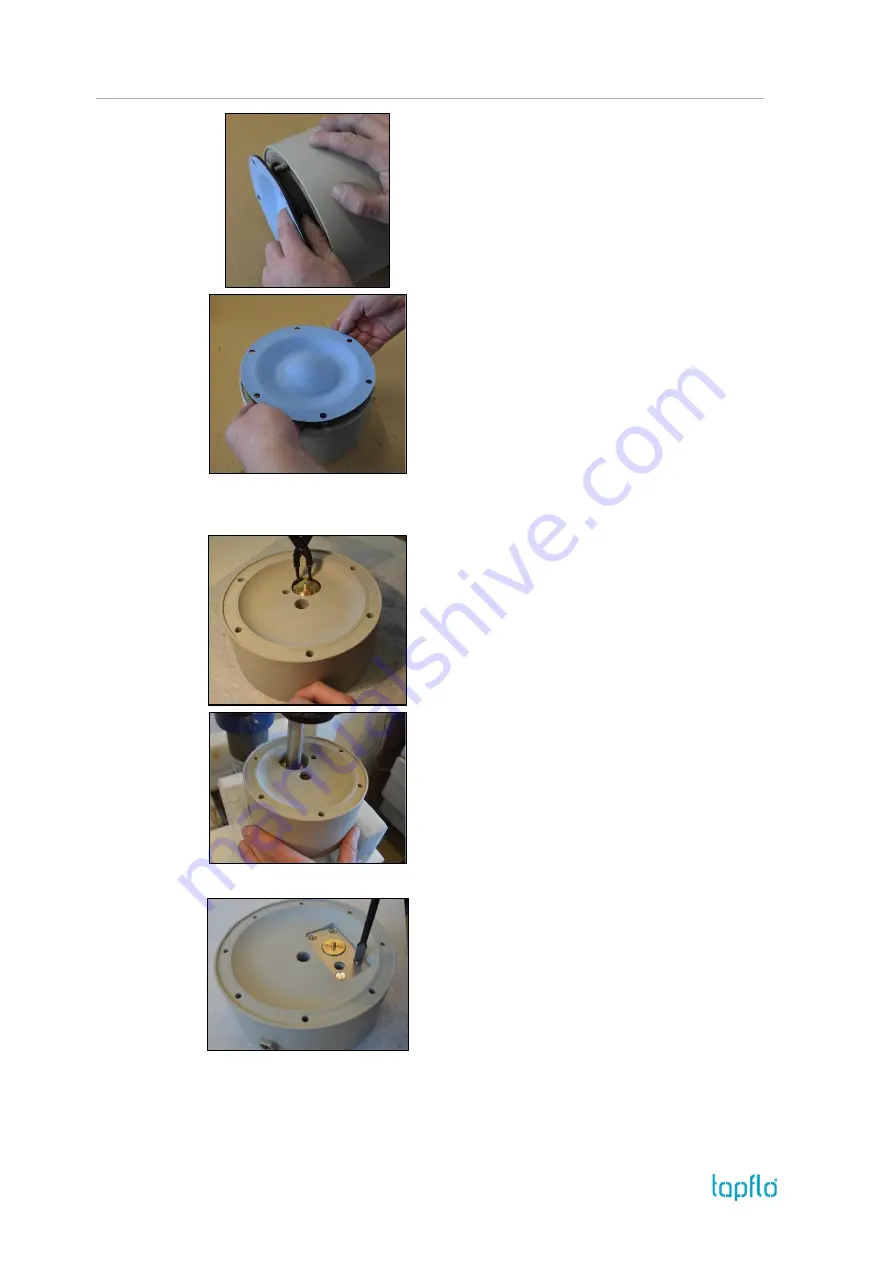
3. MAINTENANCE
IOM manual Tapflo Metal Series
24
Fig. 3.7.5
Unscrew the diaphragm [15] from one side of the pump.
Fig. 3.7.6
Take out the second diaphragm [15] along with the shaft
[16].
a)
Circlip mounted air valve
–
T/TX70, T120, T820
Fig. 3.7.7
Using pliers remove both circlips [27] from the centre
block [12].
ATTENTION!
While doing this, cover yourself with your
other hand, as the circlip easily flips away
Fig. 3.7.8
Press out the air valve [61] by means of a pressing
device. Be careful not to damage the brass edges of the
air valve.
b)
Plate mounted air valve
–
TX120, T/TX220, T/TX420
Fig. 3.7.9
Unscrew plate screws [2711] from both sides of the
centre body [12] and take out the left and right plate
[271].
Summary of Contents for Metal Series
Page 32: ...5 SPARE PARTS IOM manual Tapflo Metal Series 32 5 1 3 TX70 TX420 Spare parts drawing...
Page 36: ...5 SPARE PARTS IOM manual Tapflo Metal Series 36 5 1 6 TX820 Spare parts drawing...
Page 40: ...5 SPARE PARTS IOM manual Tapflo Metal Series 40 5 2 3 T220 T420 Spare parts drawing...
Page 44: ...5 SPARE PARTS IOM manual Tapflo Metal Series 44 5 2 6 T820 Spare parts drawing...
Page 51: ...6 DATA IOM manual Tapflo Metal Series 51 Dimensions T820 S...
Page 56: ......