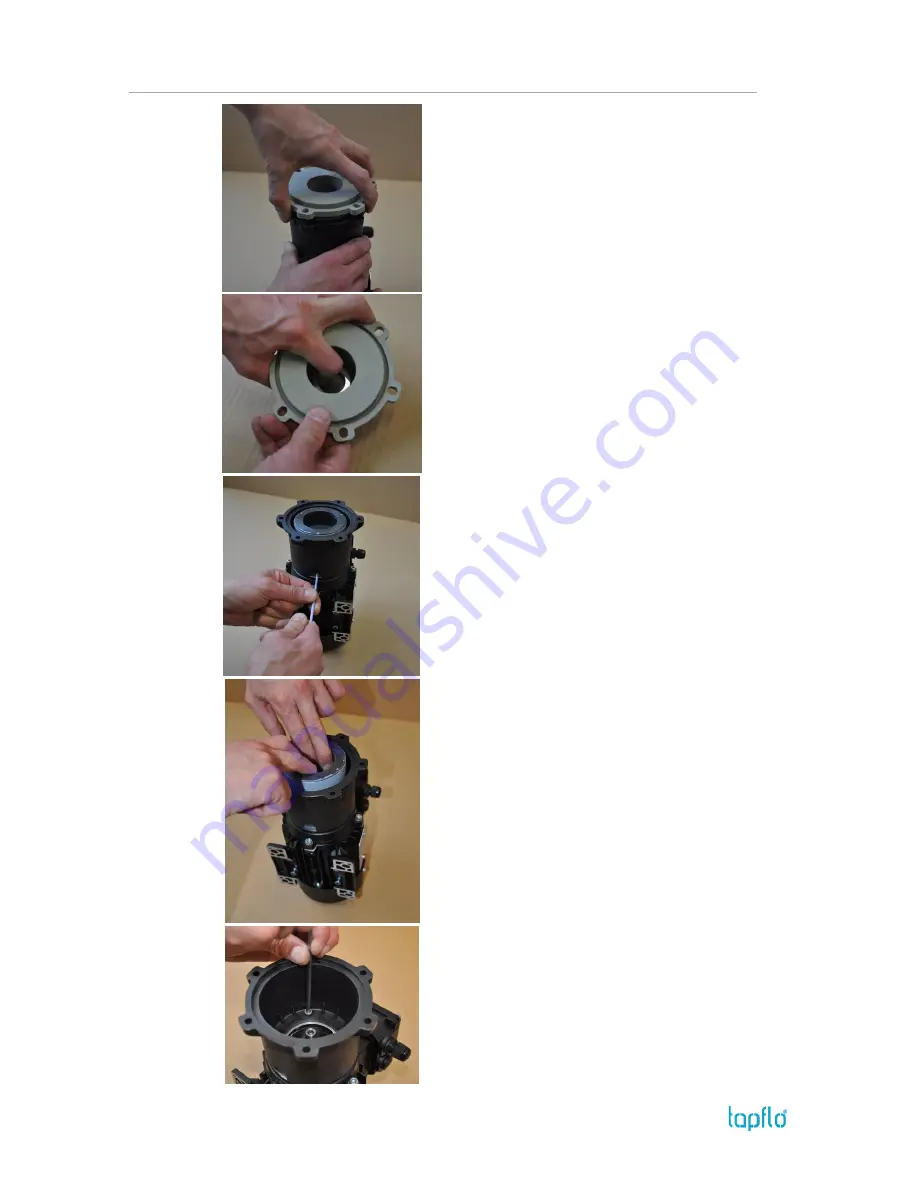
3. MAINTENANCE
IOM manual CTM mag drive pumps
17
Fig 3.3.8
Take out the isolation shell [12] form the lantern [11].
Fig 3.3.9
Pull out the rear static bushing [1522] along with the O-
ring [1822].
Fig 3.3.10
Loosen the lock screws (2 x [161] on CTM20/25; 1 x
[1611] and 2 x [1612] on CTM32).
Fig 3.3.11
Take out the external magnet assembly [16] form the
lantern [11].
Fig 3.3.12
Unscrew the motor mounting screws [111] and remove
the lantern [11] form the motor.