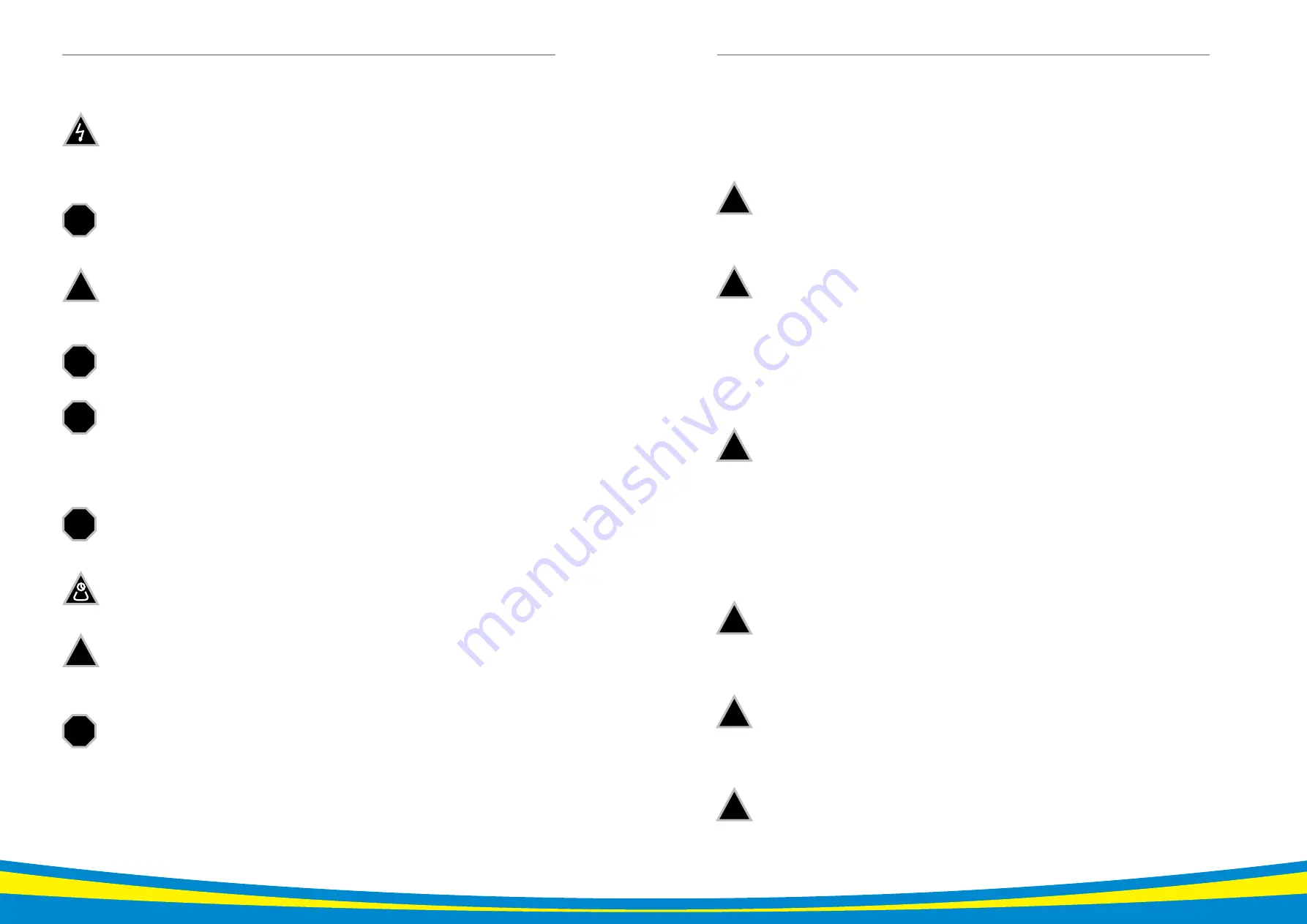
6
Instruction manual CTM mag drive pumps
IOM manual Tapflo PE & PTFE series pumps
7
0. GENERAL
0.5
Health & safety
Electric safety
Do not carry out any maintenance operation on the pump while it is running or before it has been dis-
connected from the power supply. Avoid any danger caused by electric power (for details see current
regulations in force). Check that electrical specifications on the data plate are equivalent to the power
supply to which it will be connected.
Chemical hazards
Avoid pumping liquids, even in different moments that may cause chemical reactions without having
cleaned the pump.
Dry running
Do not start nor carry out running tests before filling the pump with liquid. Always avoid the dry opera-
tion of the pump. Start the pump when it is completely filled with the delivery valve almost fully closed,
limiting this condition to the time that is strictly necessary to start the pump.
Temperature hazards
The cold or hot parts of the machine must be protected to avoid accidental contacts.
Rotating parts
Do not tamper with the protection of the rotating parts, do not touch or approach rotating parts in
movement.
Noise level
CTM pumps, including the motor, in normal operating conditions produce a sound level below 80 dB(A).
The major sources of noise are: liquid turbulence in the plant, cavitation or any other abnormal operation
that do not depend from the pump construction nor the pump manufacturer. The user must provide
suitable protective means if the sources of noise could produce a harmful noise level for operators and
for the environment (in compliance with current regulations).
Powerful magnetic field
Mag-Drive pumps use wide range, high intensity magnets. All pacemaker carriers must not approach
magnetic components; intense magnetic fields can disturb heart pace.
Solids
It is not recommended to use liquid with suspended solids, especially if sensitive to magnetism.
In case dirty liquids are to be pumped and this was not mentioned at the time of ordering, it is necessary
to contact Tapflo’s technical service before activating the pump.
Modifications and Spare parts
Any changes concerning the service of the pump as originally purchased, can be executed only after
written approval from Tapflo.
It is recommended to use only genuine Tapflo spare parts and approved accessories. The use of non-
original spare parts or non approved accessories will void warranty and removes any responsibility on
our behalf for any damage caused to people or things.
STOP
!
STOP
STOP
STOP
!
STOP
1.1
Receiving inspection
Although precaution is taken by us when packing and shipping, we urge you to carefully check the
shipment on receipt. Make sure that all parts and accessories listed on the packing list are accounted for.
Immediately report any damage or shortage to the transport company and to us.
1.2
Storage
If the equipment is to be stored prior to installation, place it in a clean location. Do not remove the pro-
tective covers from the suction, discharge and air connections, which have been fastened to keep pump
internals free of debris. Make sure to clean the pump thoroughly before installation.
1.3
Foundation
The pump-motor unit must stand on and be fixed to a sufficiently rigid structure that can support the
entire perimeter on which the unit stands. The foundation on a firm bottom are the most satisfactory.
Once the pump is in position, adjust level with metal shims between the feet and the surface on which
it stands. Check that the feet of the pump-motor unit stand well on each of them. The surface on which
the foundation stands must be flat and horizontal. If the unit is fitted on a steel structure, make sure that
it is supported so that the feet do not warp. In any case, it is advisable to fit some antivibration rubber
pieces between the pump and the brickwork.
As the pump is close-coupled type, pump-motor alignment is not required.
1.4
Piping connections
A pump is generally part of a piping system that can include a number of components such as valves,
fittings, filters, expansion joints, instruments, etc. The way the piping is arranged and the positioning of
the components has a great influence on operation and the operating life of the pump. The pump cannot
be used as a support for the components connected to it.
The flow of liquid from the pump must be as even as possible. It is advisable to avoid any tight bends or
drastic reductions of diameters that may cause flow resistance in the plant. In case of diameter reduction,
it is advisable to use appropriate conical reductions (possibly eccentric on suction side and concentric
on delivery side) at changes of diameter and at a minimum distance from pump inlets of five diameters.
1.4.1
Discharge pipe
A nonreturn valve and a shutoff/regulation valve are normally fitted on the discharge side.
The nonreturn valve protects the pump from any backflow. The shutoff/regulation valve excludes the
pump from the line and adjusts output. Never adjust flow-rate using the valve on the suction pipe.
1.4.2
Suction pipe
The suction piping is very important for the correct operation of the pump group. It must be as short
and as direct as possible. If a longer suction line is unavoidable, the diameter should be large enough,
i.e. at least as the inlet connection on the pump, to ensure less flow resistance. In any case, suction must
be carried out properly avoiding any air locks.
The CTM pumps are single-stage centrifugal type, thus not self-priming. It will therefore always be ne-
cessary to install a bottom valve in all cases when the static height of the liquid is lower than the suction
height of the pump. The suction piping must be without air inlets that are more probable with long
suction lines or if suction occurs with negative head. Critical points in these terms are also the seals bet-
ween flanges and the seals of the valve stems. Even some small air let into the suction line cause serious
operating problems that can make the pump stop.
1. INSTALLATION
!
!
!
!
!
!