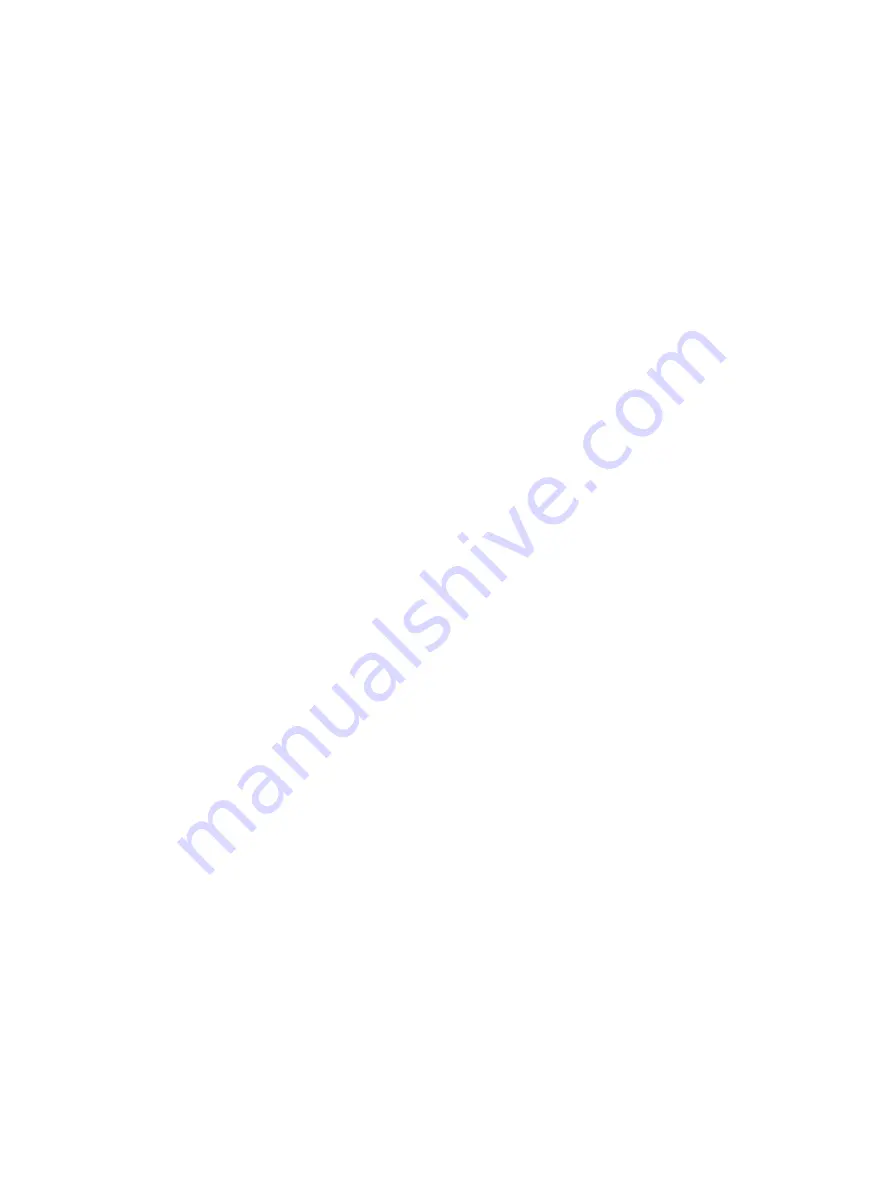
68
Circuit Descriptions
TP9100 Service Manual
© Tait Electronics Limited
May 2005
3.7
Interfaces Circuitry
Introduction
For a block diagram of the interfaces circuitry, refer to
For more information on the connector pinouts, refer to
Bi-directional Lines
Bi-directional lines are provided on two pins of the accessory connector
(
ACC GPIO
1
and
ACC GPIO
2
). These are formed by combining two uni-
directional lines. For example, the line
ACC GPIO
1
at pin 10 of the accessory
connector is formed from
ACC DIG GPI
1
and
DIG
ACC GPO
1
. The circuitry is the
same in both cases and is explained below for the case of
ACC GPIO
1
.
Output Signals
(
ACC GPIO
1
)
An output on the line
ACC GPIO
1
originates as the 3.3V signal
DIG ACC GPO
1
from the digital section. The signal is first inverted by Q905 (PNP device)
and the output divided down to 2.7V by internal resistors (10k
Ω
and 47 k
Ω
)
and R933 to drive the base of Q905 (NPN device). When the latter’s
collector current is low, the base current is a maximum and creates a small
voltage drop across R933, causing the collector emitter to saturate. As the
collector current increases, the base current decreases proportionally until
the voltage across R933 reaches 2.1V. At this point the base-emitter begins
to turn off and the base current diminishes rapidly. The net effect is a
current-limiting action. The current limit value is approximately 18 mA (the
inverse of the value of R933). The output configuration is open-collector
with a pull-up to 3.3 V.
Input Signals
(
ACC GPIO
1
)
An input signal applied to
ACC GPIO
1
is coupled via R908 to
ACC DIG GPI
1
and
fed to the digital section. As the input signal may exceed the maximum
allowed by the digital section, it is clamped by D906 and a shunt regulator.
The shunt regulator consists of Q900, R901 and R902 and begins to turn
on at approximately 2.7 V. In combination with D906, the input to
ACC DIG GPI
1
is therefore clamped to 3.3V nominally. The value of R908 is
made large to minimize the loading effect on the output pull-up resistors.
ESD Protection
On exposed inputs and outputs of the accessory and battery connectors,
ESD (electrostatic discharge) protection is provided. The protection
provided depends on the signal type and speed. GPIO and data signals are
protected by a 470pF capacitor, series resistors and clamping diodes.
For example, on ACC_RXD this consists of C903, R903 and D900. Audio
signals are protected by 10nF or 1nF capacitors (example:
AUD TAP OUT
consists of C909).
ACC PTT
is protected by a 100nF capacitor (C900) and
series resistor (R906).
Accessory PTT
Detection
Accessory PTT and function button signals are multiplexed in the accessory
on to the ACC_PTT analog input. External button presses (EPTT,
Function4, Function5 if fitted) create different DC voltages on the
ACC_PTT input allowing the radio software to determine which button
has been pressed. A voltage divider created by R904 and R931 ensure that
the voltage on the ADC input pin of IC204 does not exceed 1.2V.
Summary of Contents for TP9100
Page 1: ...TP9100 portables Service Manual MPA 00005 01 Issue 1 00 May 2005 ...
Page 4: ...4 TP9100 Service Manual Tait Electronics Limited May 2005 ...
Page 10: ...10 TP9100 Service Manual Tait Electronics Limited May 2005 ...
Page 74: ...74 Circuit Descriptions TP9100 Service Manual Tait Electronics Limited May 2005 ...
Page 78: ...78 TP9100 Service Manual Tait Electronics Limited May 2005 ...
Page 100: ...100 General Information TP9100 Service Manual Tait Electronics Limited May 2005 ...
Page 126: ...126 Disassembly and Reassembly TP9100 Service Manual Tait Electronics Limited May 2005 ...
Page 148: ...148 Interface Fault Finding TP9100 Service Manual Tait Electronics Limited May 2005 ...
Page 158: ...158 Power Supply Fault Finding TP9100 Service Manual Tait Electronics Limited May 2005 ...
Page 250: ...250 Transmitter Fault Finding TP9100 Service Manual Tait Electronics Limited May 2005 ...
Page 268: ...268 Receiver Fault Finding TP9100 Service Manual Tait Electronics Limited May 2005 ...
Page 294: ...294 Spare Parts TP9100 Service Manual Tait Electronics Limited May 2005 ...
Page 298: ...298 Antenna Identification Chart TP9100 Service Manual Tait Electronics Limited May 2005 ...