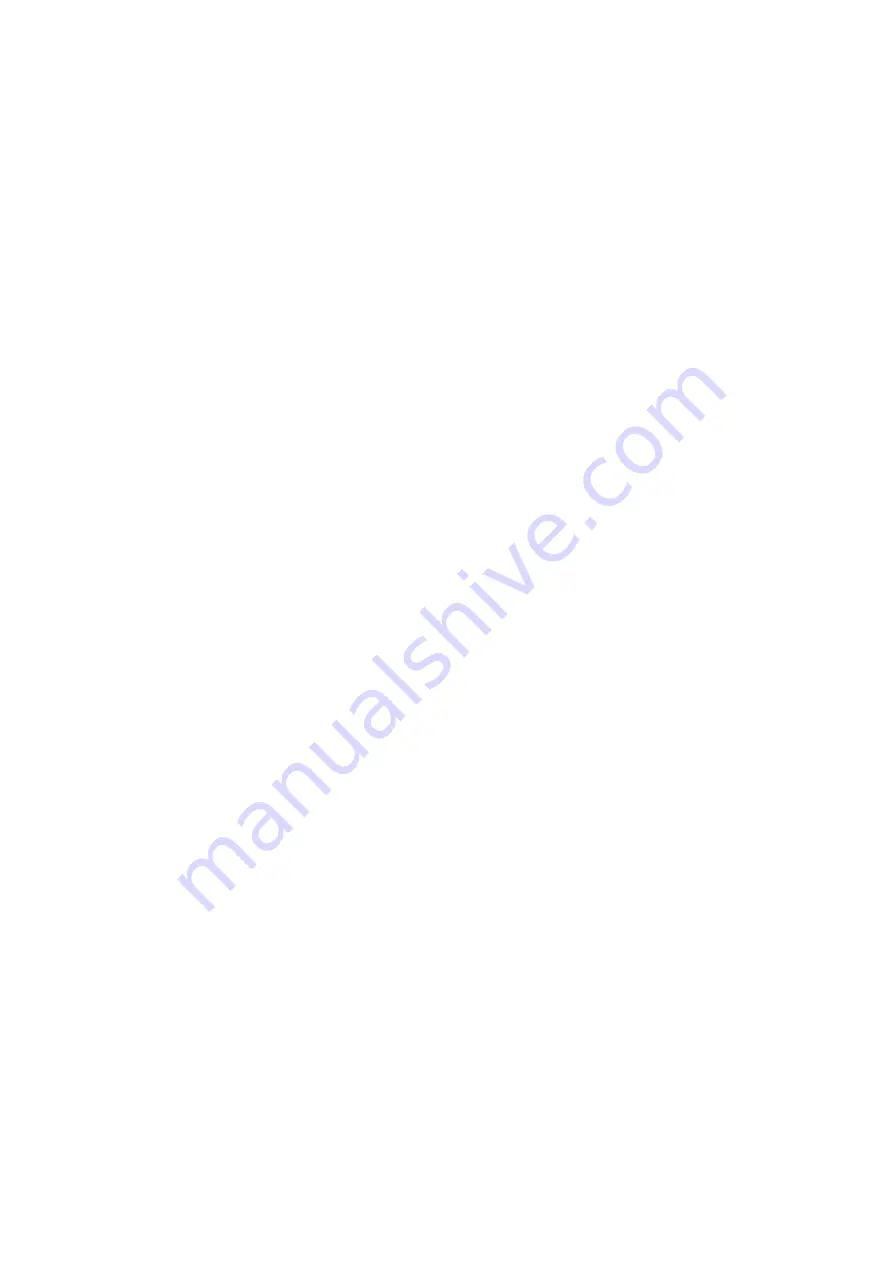
TM8100/TM8200 Service Manual
Circuit Descriptions
79
© Tait Electronics Limited
June 2006
The sections of the circuitry concerned with these functions are described
below.
Audio Signal
for Speaker
The audio signal for the speaker is generated by IC204 (
VOUTAUXP
ball).
This signal is post-volume-control and has a pre-emphasized frequency
response. The signal is then processed by R218, R217 and C231 (C205) to
restore a flat frequency response and reduce the signal level to that required
by the audio power amplifier.
Summing Circuit
The top of C231 (C205) is where side tones are summed in and the
CDC
RX
AUD
signal is obtained. C201 and R211 pre-emphasize and attenuate the
side-tone signal to give a flat side-tone frequency response and reduce the
input to an appropriate level.
Buffer Amplifier
IC201 (pins 8 to 10) amplifies the signal at the top of C231 (C205) by 19dB
and drives the
CDC
RX
AUD
system interface line via C212 and R225.
The capacitor C212 provides AC output coupling and R225 ensures
stability. The DC bias for this amplifier is derived from IC204.
Audio Power
Amplifier
The signal at the top of C231 (C205) is fed via C204 to the audio power
amplifier IC202. IC202 has 46dB of gain and a differential output
configuration. C209, C211, R252 and R253 ensure stability of the amplifier
at high frequencies. When operational, the output bias voltage for IC202 is
approximately half the radio supply voltage. When not operational, the
output becomes high impedance.
Control of Audio
Power Amplifier
Power up, power down, and muting of IC202 is controlled by two signals
from the digital section,
DIG AUD PA EN
1
and
DIG AUD PA EN
2
. The network
consisting of Q200, Q201, R200 to R206, R210 and R250 converts the
two digital signals to the single three-level analog signal required by IC202.
Microphone Signals
There are two microphone source signals:
■
ITF AUX MIC AUD
from auxiliary or internal options connector
■
ITF CH MIC AUD
from control head.
The biasing for electret microphones is provided by a filtered 3.0V supply
via R226 and R227. The components R209 and C202 provide the supply
filtering. The microphone inputs to IC204 (
VINAUXP
,
VINAUXN
,
VINNORP
,
and
VINNORN
balls) are differential. The negative inputs are decoupled to the
filtered 3.0V supply by C215 and C216. The positive inputs are biased to
approximately 1.5 V by R229, R232, R230 and R233. AC coupling and
DC input protection is provided by C213 and C214.
Auxiliary Audio
Input
The auxiliary audio input signal
ITF
AUD
TAP
IN
is DC-coupled to the ADC
input of IC205. R241 combined with internal clamping diodes in IC205
provide DC protection for the ADC input. IC205 provides the input biasing
of approximately 1.5V.
Summary of Contents for TM8235
Page 1: ...TM8100 mobiles TM8200 mobiles Service Manual MMA 00005 04 Issue 4 June 2006...
Page 10: ...10 TM8100 TM8200 Service Manual Tait Electronics Limited June 2006...
Page 62: ...62 Description TM8100 TM8200 Service Manual Tait Electronics Limited June 2006...
Page 148: ...148 Disassembly and Reassembly TM8100 TM8200 Service Manual Tait Electronics Limited June 2006...
Page 162: ...162 Servicing Procedures TM8100 TM8200 Service Manual Tait Electronics Limited June 2006...
Page 178: ...178 Interface Fault Finding TM8100 TM8200 Service Manual Tait Electronics Limited June 2006...
Page 258: ...258 Receiver Fault Finding TM8100 TM8200 Service Manual Tait Electronics Limited June 2006...
Page 446: ...446 Spare Parts TM8100 TM8200 Service Manual Tait Electronics Limited June 2006...