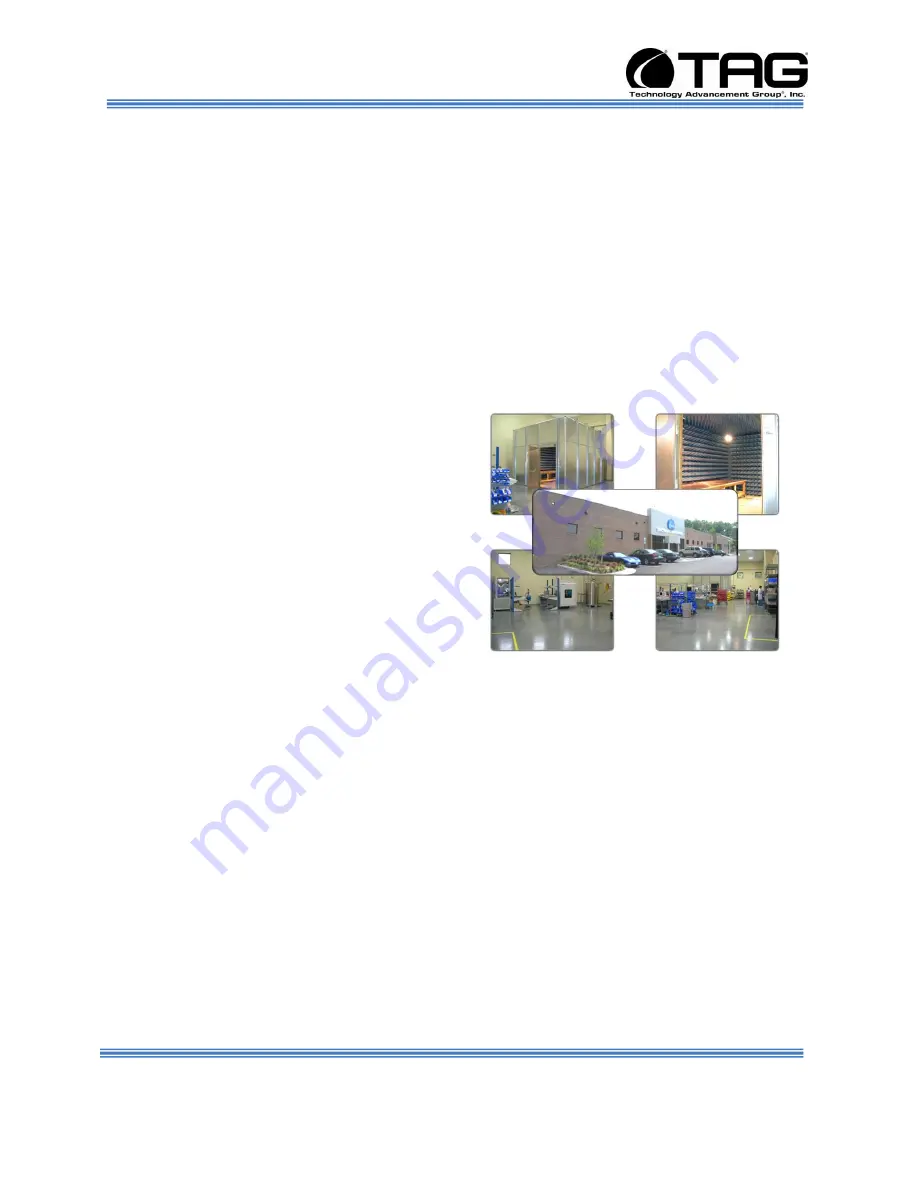
Operations Manual
SV-2001-THS Computer
Document Number: 273-MNL-001
Page 4 of 58
Version A. 08/25/2010
2.2 Core Competences
2.2.1 Engineering
TAG’s engineering methodology is built upon Multi-Disciplinary Optimization (MDO) and
rigorous design reviews. Although PMs drive the schedule at TAG, Engineering
leverages Computer-Aided Design (CAD) tools, Computational Fluid Dynamics (CFD)
modeling, rapid prototyping processes, and diverse test equipment and facilities to
ensure requirements are being met at every step of the design. TAG Engineering
follows a proven design-review process, ensuring all entrance and exit criteria are met
at each stage. Rigorous documentation is compiled to demonstrate requirement
compliance, risks are mitigated, and decisions are prudent
– throughout the design
process.
TAG prides itself on its engineering
laboratories and facilities. Over the past
three years, TAG has invested in several
pieces of equipment that allow TAG to test
and certify products directly onsite to the
harshest environmental requirements of
military standards
– including the MIL-STD-
810F and DO 160D.
TAG’s onsite test equipment currently
includes a Highly Accelerated Lifecycle
Testing (HALT) Chamber, an
Electromagnetic Interference (EMI) test chamber, and a high-/low-temperature thermal
test chamber. TAG’s facility also provides:
A floor plan designed to support a cellular manufacturing model with modular
assembly lines
A dedicated 24-hour system burn-in room
A modern production status tracking and Enterprise Resource Planning (ERP)
system with external web collaboration capabilities
Dedicated Quality Assurance workstations for system compliance and validation
inspection
2.2.2 Manufacturing and Integration
TAG implements Cellular Manufacturing processes through our compartmentalized,
state-of-the-art production facility to minimize waste byproducts and maximize
production efficiency. TAG’s manufacturing facility is physically partitioned to model the