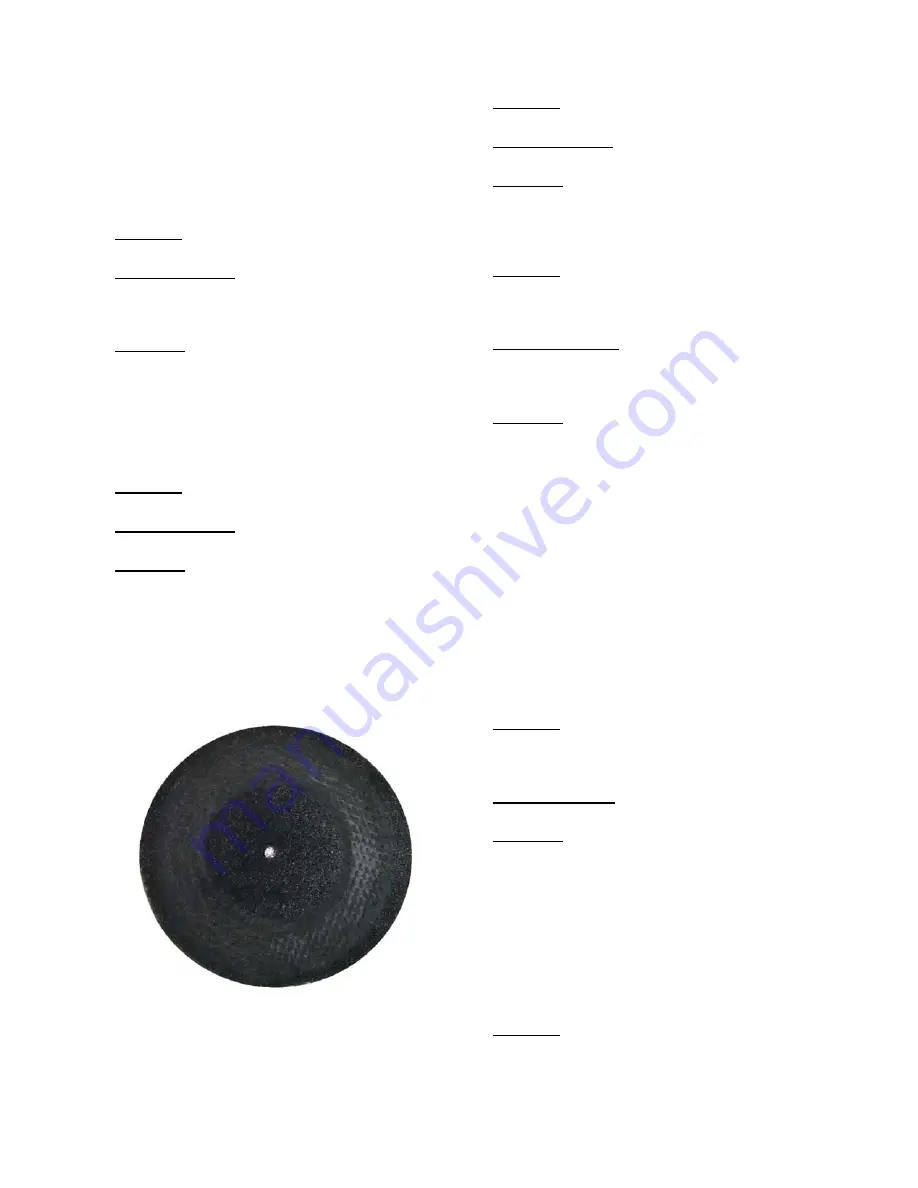
In the following procedures, it is assumed that
tests are conducted in an atmosphere controlled
to 50 percent humidity and 21 - 24°C
(70 – 75°F)
temperature. Also, samples are conditioned in
the test atmosphere for at least 24 hours before
testing.
Aluminum – Anodized Finish
Specimen: 100 mm
(4 inch)
square or diameter
with 6.35 mm
(0.25 inch)
center hole.
Wheels and Load: CS-17 with 1000 gram load.
Alternatively, use H-18 or H-10 Calibrade with
250 or 500 gram load. Or use H-38 Calibrade
with 1000 gram load.
Evaluation: Visual end point, indicated by the
first deep abrasion marks or spot breakthrough
as the wheel wears through the hard oxide
coating into the soft aluminum; or weight loss
method.
Carpeting (Figure 73)
Specimen: 108 mm
(4.5 inch)
round or square
mounted on S-36 mounting card.
Wheels and Load: H-18 or H-22 Calibrade with
500 or 1000 gram load.
Evaluation: Visual method, changes in luster;
surface; color; appearance of first broken
threads; appearance of a hole. Alternatively,
physical changes such as thickness; weight;
fiber loss.
Remark: Floor coverings, such as broadloom carpets or
automobile floor mats should be tested with 1000 gram load
using H-18 or sometimes H-22 wheels.
Figure 73
Ceramic Finishes
Specimen: 100 mm
(4 inch)
square with 6.35 mm
(0.25 inch)
center hole.
Wheels and Load: CS-17 Calibrase with 500 or
1000 gram load.
Evaluation: Visual end point, at the first sign that
the wheels have worn through the surface glaze.
Coatings (Paint, Enamel, etc.)
Specimen: Applied evenly to substrate
approximately 100 mm
(4 inch)
square with 6.35
mm
(0.25 inch)
center hole. (i.e. S-16 specimen
plate).
Wheels and Load: CS-10 Calibrase with 500
gram or 1000 gram load. Alternatively the CS-
17 with 1000 gram load or CS-10F with 125 to
500 gram load may be used.
Evaluation: Visual end point, at the first sign that
the wheels have worn through the coating to the
substrate; weight loss method, without
permitting the wheels to wear through to
substrate; or change in coating thickness.
Remark 1: Accurate, dependable evaluation of the abrasion
resistance of organic coatings requires application of a
uniform film of normal thickness (such as that applied in
actual production practice).
Remark 2: Prior to applying a coating, the substrate should
be thoroughly cleansed of dirt and grease.
Remark 3: The effect of age on organic materials and
coatings bears close investigation. Many coatings show low
abrasion resistance the first few days but progressively
improve during the following 30 days due to curing.
Concrete Floors
Specimen: 100 mm
(4 inch)
diameter or square,
with thickness to 12.7 mm
(0.5 inch)
. The S-21
extension nut should be used, which requires a
9.525 mm
(0.375 inch)
center hole.
Wheels and Load: H-22 Calibrade with 500 or
1000 gram load.
Evaluation: Weight loss or depth of penetration
[maximum depth of penetration recommended is
0.8 mm
(0.0312 inch)
].
Remark 1: Test is for abrasion resistance of cement floor
hardeners or surface coatings.
Remark 2: The specimen must be carefully molded for
uniform thickness and smooth surface to provide continuous,
even contact with the abrading wheels.
Decorative Laminates (Figure 74)
Specimen: 100 mm
(4 inch)
square with 6.35 mm
(0.25 inch)
center hole for material to 6.35 mm
(0.25 inch)
thick; 9.525 mm
(0.375 inch)
hole for S-
21 extension nut for material 6.35 mm
(0.25 inch)
to 12.7 mm
(0.5 inch)
thick.
34
5135 / 5155 Operating Instructions ver 1.1