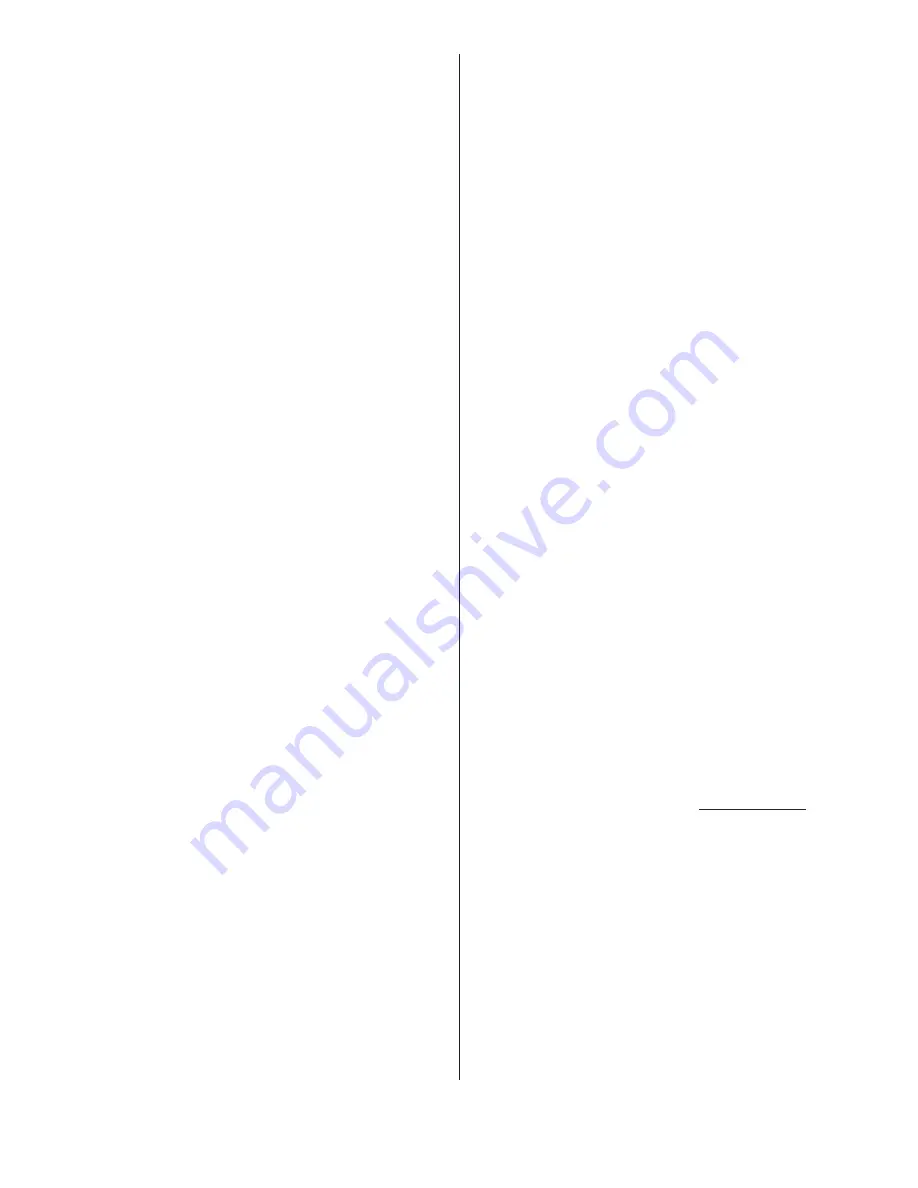
Systematics, Inc. West Chester, PA. 19380
3
WIRE FEED SPEED RANGE:
50 - 800 inches per minute
DIMENSIONS:
Height
34 in.
Width
14-1/2 in.
Depth
34-1/2 in.
Weight
165 lbs.
TORCH SPECIFICATIONS
NECK ANGLE:
60 degrees
LEAD LENGTH:
10 feet
OVERALL LENGTH:
10 feet
COOLING METHOD:
gas (air)
RATING - DUTY CYCLE:
With Argon/CO2 gas
150 amps @ 100%
With CO2 gas
200 amps @ 100%
CHECK LIST
THE SYSTEMATICS PBE180 INCLUDES THE
FOLLOWING:
1- Combination Power Source/Wire
Feeder
1- Cylinder Rack/Industrial Wheel
Kit-Factory installed
1- 15TG10 MIG Torch with adjustable
nozzle
1- 20 foot Power Input Cable
1- 10 foot Work Cable and Clamp
1- MP250PK-1 Parts Kit
1- GR-FM Gas Regulator/Flowmeter
1- Nozzle, 1/2 in. orifice (in-
stalled on MIG torch)
1- Contact Tip, for .030 in. wire
(installed on MIG torch)
1- ER70S-6-30-3, Sample Spool of
.030 Steel Wire
ITEMS REQUIRED FOR MIG WELDING
WHICH ARE NOT PROVIDED WITH THE
PBE180
1. Full cover welding helmet with
proper colored lens (shade 9 to
11 depending on operator’s pref-
erence).
2. Proper shielding gas and cylin-
der.
3. Leather welding gloves.
4. 208 or 230 volt 40 amp single
phase AC power.
5. Other personal protective
equipment which may vary to
match the welding being per-
formed.
INSTALLATION
POSITIONING THE UNIT
Locate the unit adjacent to the
welding area and position it so
there is adequate clearance all
around for ventilation and mainte-
nance.
ELECTRICAL SUPPLY
Ensure that there is a 208 or 230
volt, single phase, 40 amp electri-
cal supply within easy reach of the
unit. The input cable supplied is 20
feet long. A 50 foot cable is an
optional extra. Attach a suitable
plug making sure the green wire is
attached to the ground terminal of
the wall plug. All wiring should be
performed by a qualified electri-
cian.
230V INPUT SELECTION
1. Factory selected no change is
needed.
208V INPUT SELECTION
1. Remove the top cover.
SPECIFICATIONS (Cont.)
(continued on following page)