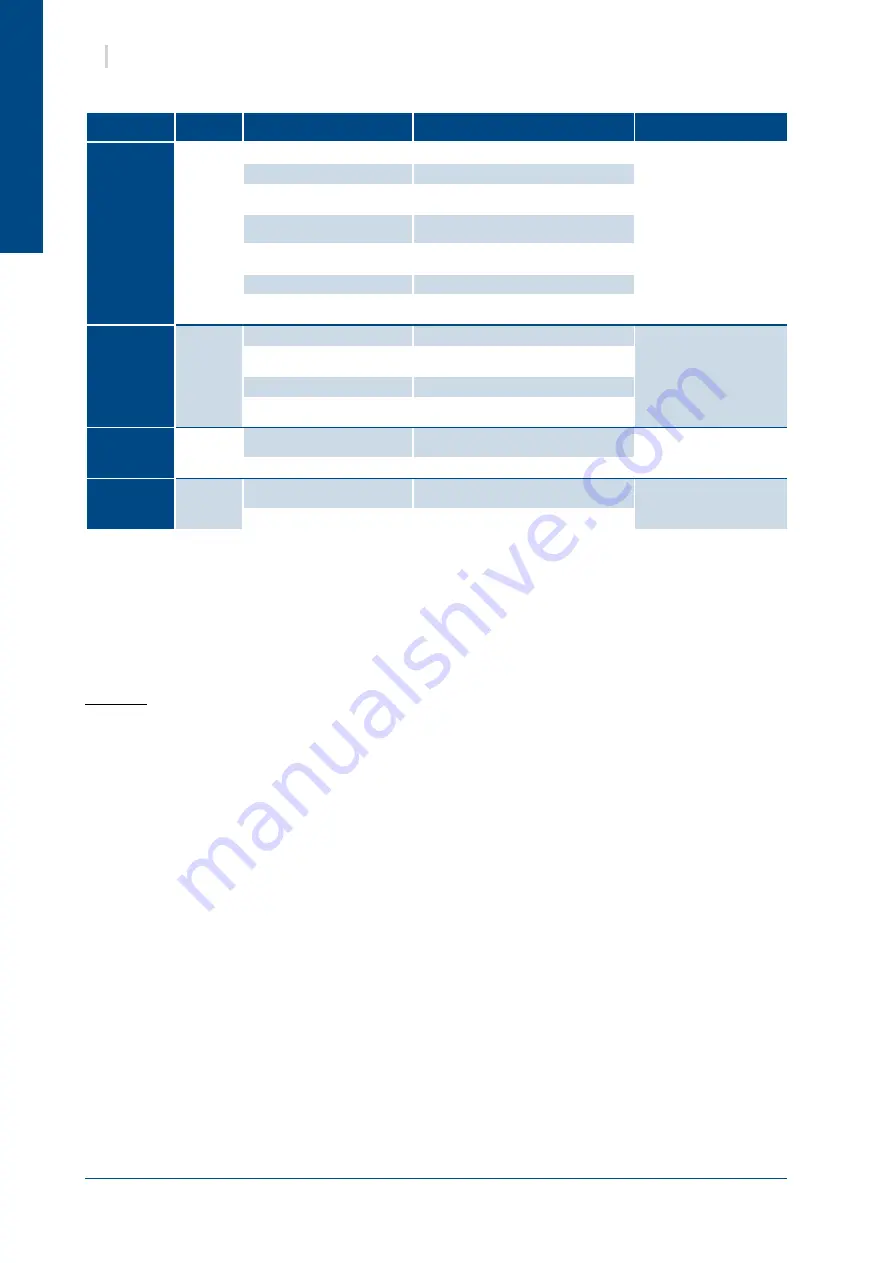
English
36 SYSHRW
17.2.3. HEATING MODE
FAULT
LED LARM CODE POSSIBLE CAUSE
CORRECTIVE ACTION
ACTION FOR CANCELLING FAULT CODE
AFTER CORRECTION
High pressure or
water flow fault
100000000
1 flashe
Insufficient airflow
Check proper fan operation.
Cut the mains power supply for
5 seconds, and then reconnect.
Clogged filters.
Clean or replace the filters.
Too high aeraulic pressure loss due to an
obstruction in the intake duct.
Test the aeraulic network.
Insufficient water flow or no water flow at
the level of the appliance.
Test the flow from the pump on the main loop.
Stop cock or water inlet valve shut (**)
Test the valve electrical supply. Test the direction of
flow. Open the valve.
Faulty pressure differential
Check electrical connections.
Pressostat defective, broken wire or short
circuit.
Check the proper connection of the HP pressostat and/or
conduct a continuity test.
Low pressure
110000000
2 flashes
Insufficient water flow in the appliance.
Test the pump flow at the level of the main loop.
The fault code is automatically
cancelled after correction(***).
The LED stops flashing and the green
light remains on.
Pressostat sensor defective, broken wire
or short circuit.
Check the proper connection of the LP pressostat and/or
conduct a continuity test.
Refrigerant leak.
Find and repair any leaks on the pipe circuits.
Water inlet valve closed (**)
Test the valve electrical supply. Test the direction of
flow.
Low water
temperature limit
111110000
5 flashes
Hot water loop temperature < 13°C .
Test the temperature at the level of the main loop.
The fault code is automatically
cancelled after correction
(***).
The LED stops flashing and the green
light remains on.
Insufficient water flow.
Test the water flow at the level of the main loop.
High water
temperature limit
111111000
6 flashes
Hot water loop temperature > 35°C
Test the temperature at the level of the main loop.
The fault code is automatically
cancelled after correction
(***).
The LED stops flashing and the green
light remains on.
Insufficient water flow.
Test the water flow at the level of the main loop.
(**)
This case only concerns installations where the valve is fitted on the water loop upstream of the
machine.
(***)
Lockout if 3 faults within 1 hour. Cut the mains power supply for 5 seconds, and then reconnect.
Note
: More than 2 alarm codes can be activated at the same time. Only the last code detected will be
visible on the RCL control module or on the STORM2 circuit board. After the source of the first alarm code
is resolved, the second code will appear, and so on until all the faults are cancelled and until the LED stops
flashing.
Example:
111 000 000
²
1 corresponds to one flash of the LED situated on the STORM2 circuit board or on the RCL.
²
0 indicates that there is no flash.
In this precise case, there will be 3 flashes, then the flashing will stop for a while (a few seconds), then there
will be 3 further flashes and so on until the fault is cancelled. Then the LED is off in OFF mode, and fixed on
in ON mode.
18. IN-WARRANTY RETURN MATERIAL PROCEDURE
19. SERVICE AND SPARE PARTS ORDER
Material must not be returned without permission of our After Sales Department.
To return the material, contact your nearest sales office and ask for a "return voucher". This return voucher
shall be sent out with the returned material and shall contain all necessary information concerning the
problem encountered.
The return of the part does not constitute an order for replacement. Therefore, a purchase order must be
entered through your nearest distributor or regional sales office. The order should include part name, part
number, model number and serial number of the unit involved.
Following our personal inspection of the returned part, and if it is determined that the failure is due to faulty
material or workmanship, and in warranty, credit will be issued on customer's purchase order. All parts shall
be returned to our factory, transportation charges prepaid.
The model number, the confirmation number and the unit serial number indicated on the name plate must
be provided whenever service works or spare parts are ordered.
For any spare part order, indicate the date of unit installation and date of failure. Use the part number
provided by our service spare parts, if it not available, provide full description of the part required.