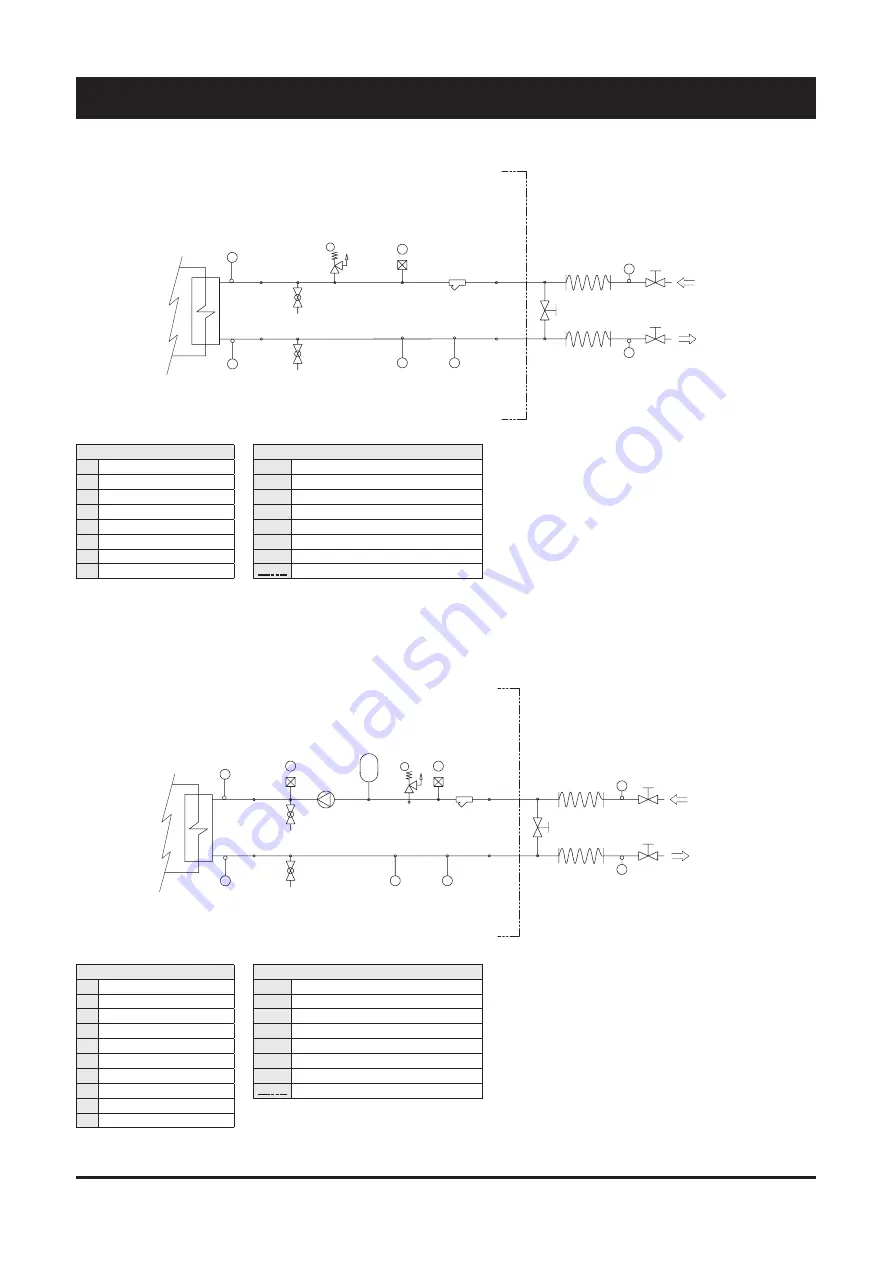
14
External water circuit - Basic Unit
4 - Installation
1
B
A
10
5
G
G
9
11
11
12
12
13
INLET
OUTLET
FS
I
8
E
D
8
COMPONENTS
1
Plate heat exchanger
5
Water filter
8
Pressure point/drain valve
9
Water outlet
10
Water inlet
11
Globe valve
12
Flexible pipes
13
By-pass valve
SAFETY/CONTROL DEVICES
A
Inlet water temperature sensor
B
Outlet water temperature sensor
D
Vent valve (105 mbar)
E
Water safety valve (3 bar)
FS
Flow switch
G
Thermometer
I
Hydrometer
Unit side
External water circuit - 1 Pump
8
D
2
E
8
I
FS
OUTLET
INLET
13
12
12
11
11
9
G
G
5
10
A
B
1
7
D
COMPONENTS
1
Plate heat exchanger
2
Pump
5
Water filter
7
Pressure expansion tank
8
Pressure point/drain valve
9
Water outlet
10
Water inlet
11
Globe valve
12
Flexible pipes
13
By-pass valve
SAFETY/CONTROL DEVICES
A
Inlet water temperature sensor
B
Outlet water temperature sensor
D
Vent valve (105 mbar)
E
Water safety valve (3 bar)
FS
Flow switch
G
Thermometer
I
Hydrometer
Unit side