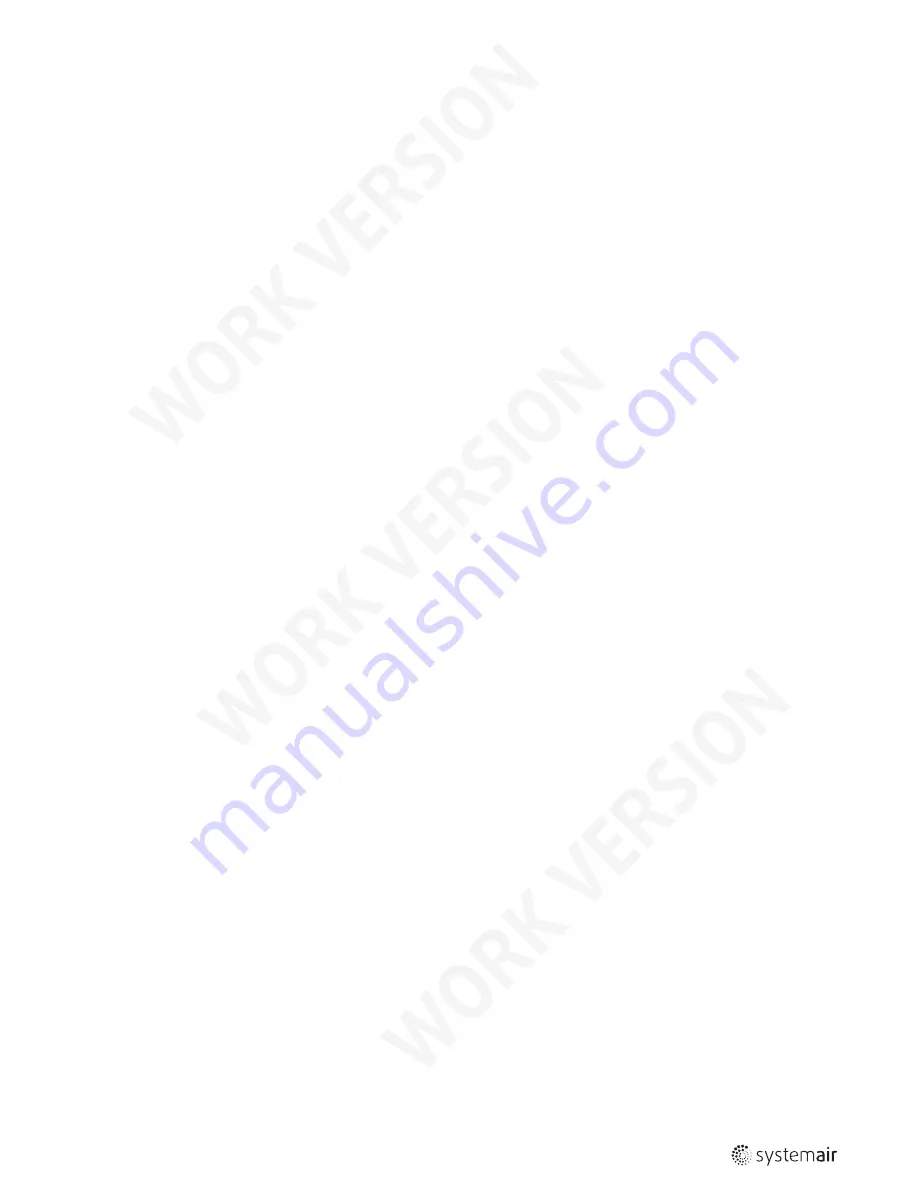
FGS | PP-105_201608 | 11 / 16
1.2 Installation of the FGS into a SOFT CROSSING (Fig. 3, Tab. 2)
1.
Prepare a rectangular opening with dimensions
L
1
=
L
+ 260
mm and
H
1
=
H
+ 135 mm (according to Fig. 1), the opening
surfaces must be even and cleaned.
2. Put together the frame from two parts (1a a 1b) according to
the wall width, and screw it into place with screws DIN 7982
C-H 4.2 × 13 included in the pack.
3.
Prepare the mineral wool installation segments (with density
150 kg/m
3
, thickness 50 mm). First apply the suitable
fireproof layer/glue (e.g. Isover BSF) onto the FGS installation
frame at the place of its future placement, assemble and glue
the filling of the future installation with the same glue.
4. Fix the frame to the rectangular opening with screws
(recommended screws 5 × 100, fabory 29385.050.100;
screws not included in pack; Fig. 3). Part 1a of frame has to
be abreast with the wall. Lead the cable for the connect - see
Fig. 10 and 11. After the glue has dried, the installation frame
along with the filling are ready for installation.
5.
Apply the same glue onto the internal surface of the wall
opening. Also apply the same glue on the external surface
of the filling glued on the damper surface. Immediately after
application, place the installation frame into the wall opening
in such way that will not deform the installation frame.
6. After inserting the installation frame into the opening and
after fixing it, apply the same fire-resistive mastic, at least
2 mm thick layer and 100 mm wide, on the opening filling
and wall edges evenly from both sides.
7. Before the glue dries, remove the unwanted remnants
of the mastic.
8.
If needed, uncover and clean the installation frame after
installation.
9.
Connect the connector with the plug.
10. Insert the closed FGS into the installation frame, join the
connectors and fix both the upper and lower side of the FGS
with screws DIN 7504M-SR 4.2 × 25 (Pos. 7; screws are in
the pack - the amount depends on nominal dimensions of
the FGS)
11.
If needed, uncover and clean the FGS after installation.
12.
Check the functionality of the FGS.
2 Operation and maintenance
2.1 FGS operation
After installation, the functionality of the FGS must be checked
and set into the open operating position.
2.1.1 Manual FGS
On the bottom of the front right side, one hole is placed (Fig.
12). Insert a screwdriver through this hole or a thin object with
a diameter of 6 mm max, lever up the upper blade and push
the latch (spring) - this releases the mechanism. Twist the
blades into the horizontal position (in the direction indicated
by the arrow - Fig. 13), force against the spring and fix the first
blade from the top side with the thermal fusible link (Fig. 14).
2.1.2 Motorised FGS
By connecting a power source according to the relevant
scheme displayed in Fig. 5-8, activate the actuator and the
blades will open. For an actuator with the BKN230-24 unit -
by connecting a power source to the unit BKN230-24, activate
the actuator and the blades will open.
2.2 Maintenance
Systemair FGSs are maintenance free. Only periodic dry cleaning
is necessary - no different than entire ventilation systems.
3 Functionality check
3.1 Manual FGS
In the open position, all blades must be fully open and detented,
and the appropriate signaling circuit must be switched on.
•
To close the FGS: lever up the upper blade with your fingers
and release the thermal fusible link by pushing with a
screwdriver in the direction indicated by the arrow (Fig. 15).
Remove the screwdriver and release your fingers from the
blade. The blades must come up to the fully closed position
and remain there detented.
•
After reaching the end position of the blades, the appropriate
signaling circuit must switch on.
After checking, set the FGS into the open position (that is the
operating position; see Chap. 2.1.1).
3.2 Motorised FGS
After connecting the supply connectors (see Fig. 10 and Chapter
2.1.2), the FGS opens.
• The blades must come to the fully open position and must
remain there detented.
•
After reaching the end position of the blade, the appropriate
signaling circuit must be switched on.
After disconnecting the supply connector (see Fig. 10) - e.g. by
means of pulling the FGS out of the frame - the FGS closes.
DO NOT COME IN CONTACT WITH THE BLADES DURING THEIR
MOVEMENT TO AVOID RISK OF INJURY!
• The blades must come up to the fully closed position and
remain there detented.
•
After reaching the end position of the blades, the appropriate
signaling circuit must be switched on.
After checking, set the FGS into the open position (that is the
operating position; see Chap. 2.1.2).