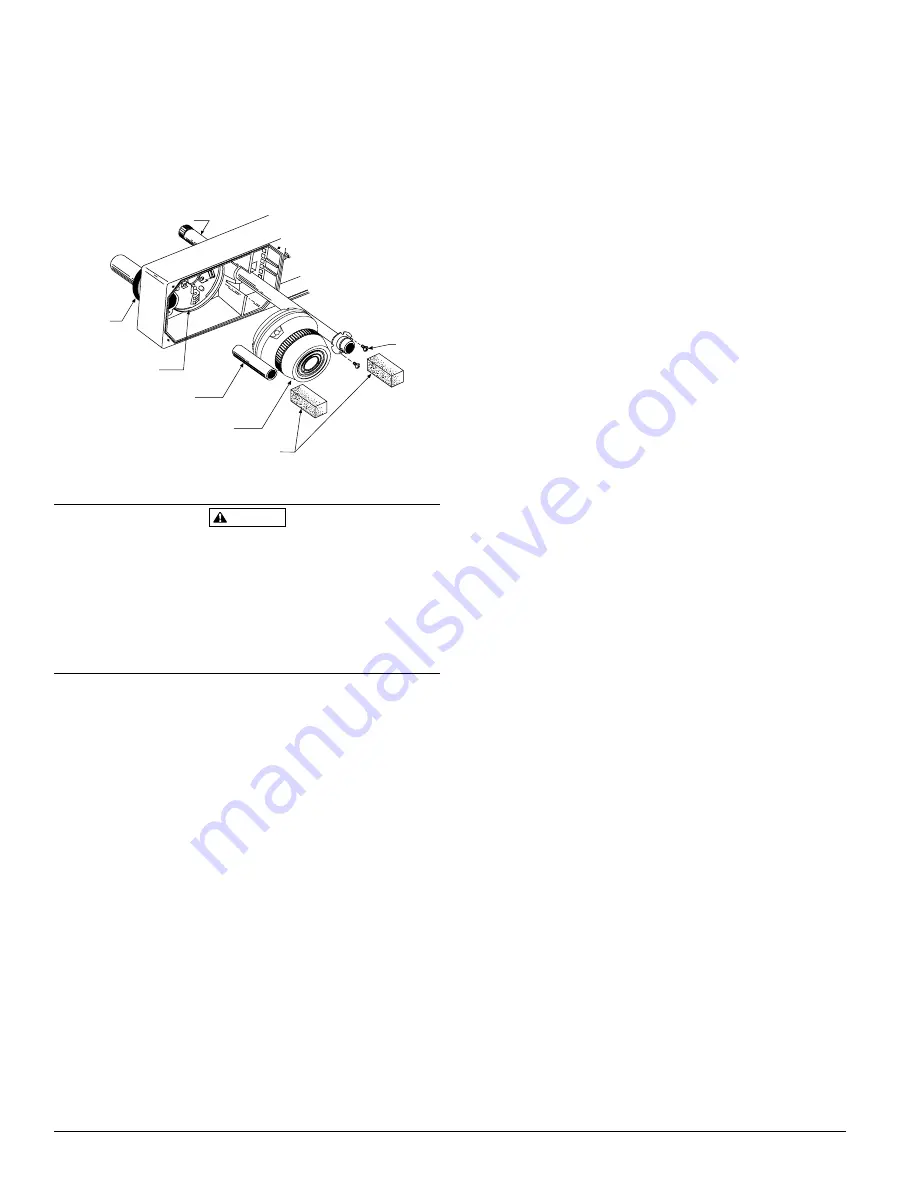
[5.6] Install The Filters
To install the sampling tube filters, simply push the filter
adapter into the exhaust tube, and then push the filter onto
the adapter tube on the left, as shown in Figure 8. Then in-
stall the other filter over the end of the inlet sampling tube.
Figure 8. Sampling tube filter installation:
SAMPLING TUBE
FILTERS
SAMPLING TUBE
MOUNTING
SCREWS
DETECTOR HEAD
EXHAUST
FILTER ADAPTER
DETECTOR BASE
INLET SAMPLING TUBE
FOAM GASKET
A78-2106-01
CAUTION
Filters require periodic cleaning or replacement, depending
on the amount of dust and dirt accumulated. Visually in-
spect the filters at least quarterly; inspect them more often
if the dust accumulation warrants it. See Section [6] for
more information. Replacement filters can be ordered from
System Sensor, 3825 Ohio Ave., St. Charles, IL 60174. (Ex-
haust tube/intake tube filter P/N F36-05-00)
[5.7] Perform Detector Check
1. Perform STANDBY AND TROUBLE TEST per Section
[6.2.1].
2. Perform MAGNET TEST per Section [6.2.2.1]. The
RTS451 test of Section [6.2.2.2] may substitute for this
requirement.
3. Perform AIR FLOW TEST per Section [6.1.1].
4. Perform SMOKE RESPONSE TEST per Section [6.1.2].
5. Perform SENSITIVITY TEST per Section [6.2.3].
6. Record all test results in the DETECTOR TEST LOG pro-
vided with this manual.
[5.8] Install The Cover
Install the cover using the four screws that are fixed in the
housing cover. Be certain filters are installed as specified in
Section [5.6]. Make sure that the cover fits into the base
groove and that all gaskets are in their proper positions.
Tighten the four cover screws to 10 in-lbs.
[6] Duct Detector Maintenance And Test Procedures
Test and maintain duct detectors as recommended in NFPA
72. The tests contained in this manual were devised to as-
sist maintenance personnel in verification of proper detec-
tor operation.
Before conducting these tests, notify the proper authorities
that the smoke detection system will be temporarily out of
service. Disable the zone or system under test to prevent
unwanted alarms.
After conducting these tests, record the appropriate infor-
mation in the DETECTOR TEST LOG provided with this
manual.
[6.1] Smoke Entry Tests
[6.1.1] Air Flow
To verify sufficient sampling of ducted air, use a manom-
eter to measure the differential pressure created from air
flow across the sampling tubes. The pressure should mea-
sure no less than 0.01 inches of water and no greater than
1.20 inches of water.
[6.1.2] Smoke Response
To determine if smoke is capable of entering the sensing
chamber, visually identify any obstructions. Plug the ex-
haust and inlet tube holes to prevent ducted air from carry-
ing smoke away from the detector head, then blow smoke
such as cigarette, cotton wick, or punk directly at the head
to cause an alarm. REMEMBER TO REMOVE THE PLUGS
AFTER THIS TEST, OR THE DETECTOR WILL NOT FUNC-
TION PROPERLY.
D400-14-00
8
I56-554-05
Summary of Contents for DH400
Page 14: ...NOTES D400 14 00 14 I56 554 05 ...