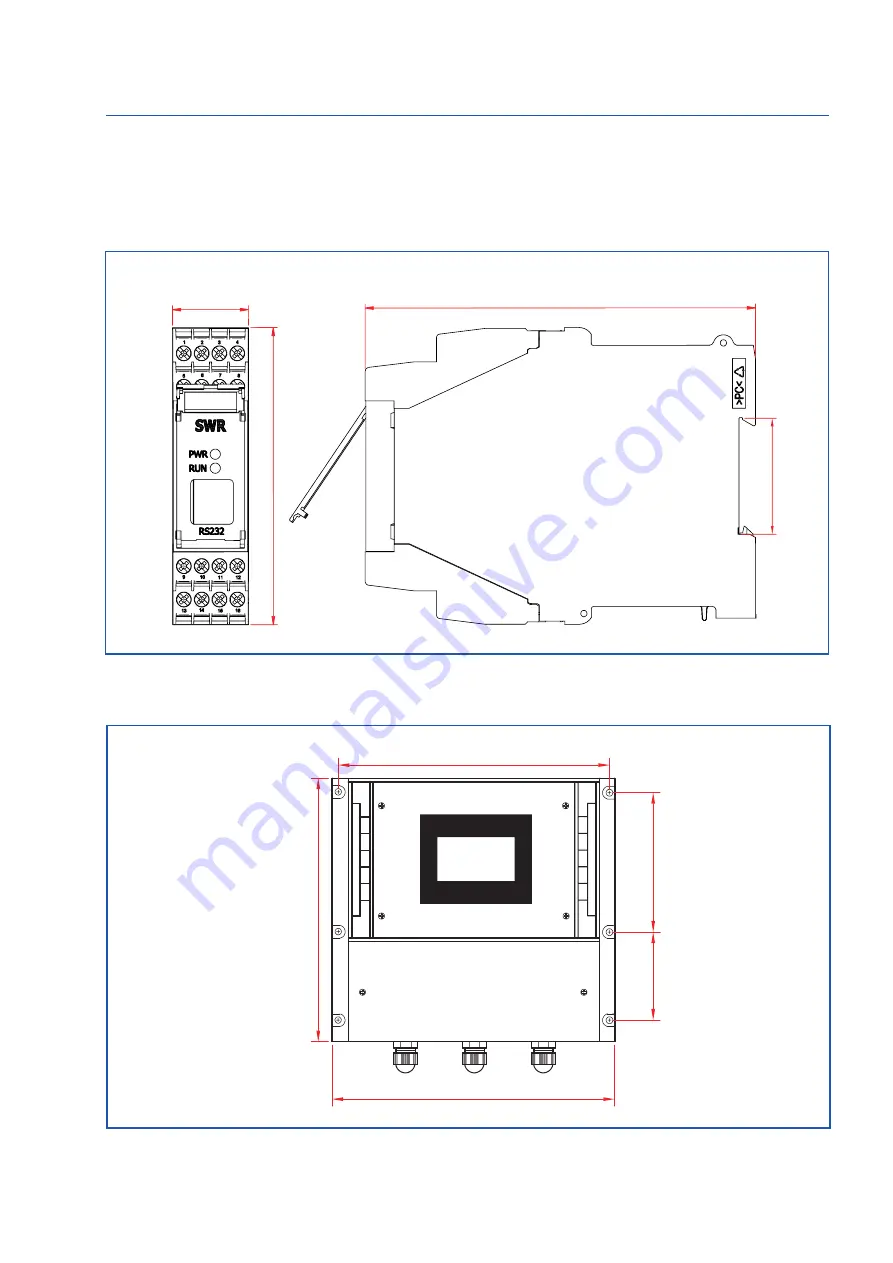
Operating Instructions
10
Fig. 9: DIN rail housing for the transmitter
Fig. 10: Field housing for the transmitter
4.4 Mounting the transmitter
•
The entire transmitter can be installed at a maximum distance of 300 m from the sensor.
The housing is prepared for installation on a DIN rail according to DIN EN 60715 TH35.
23
90
118
35
90
120
244
254
237