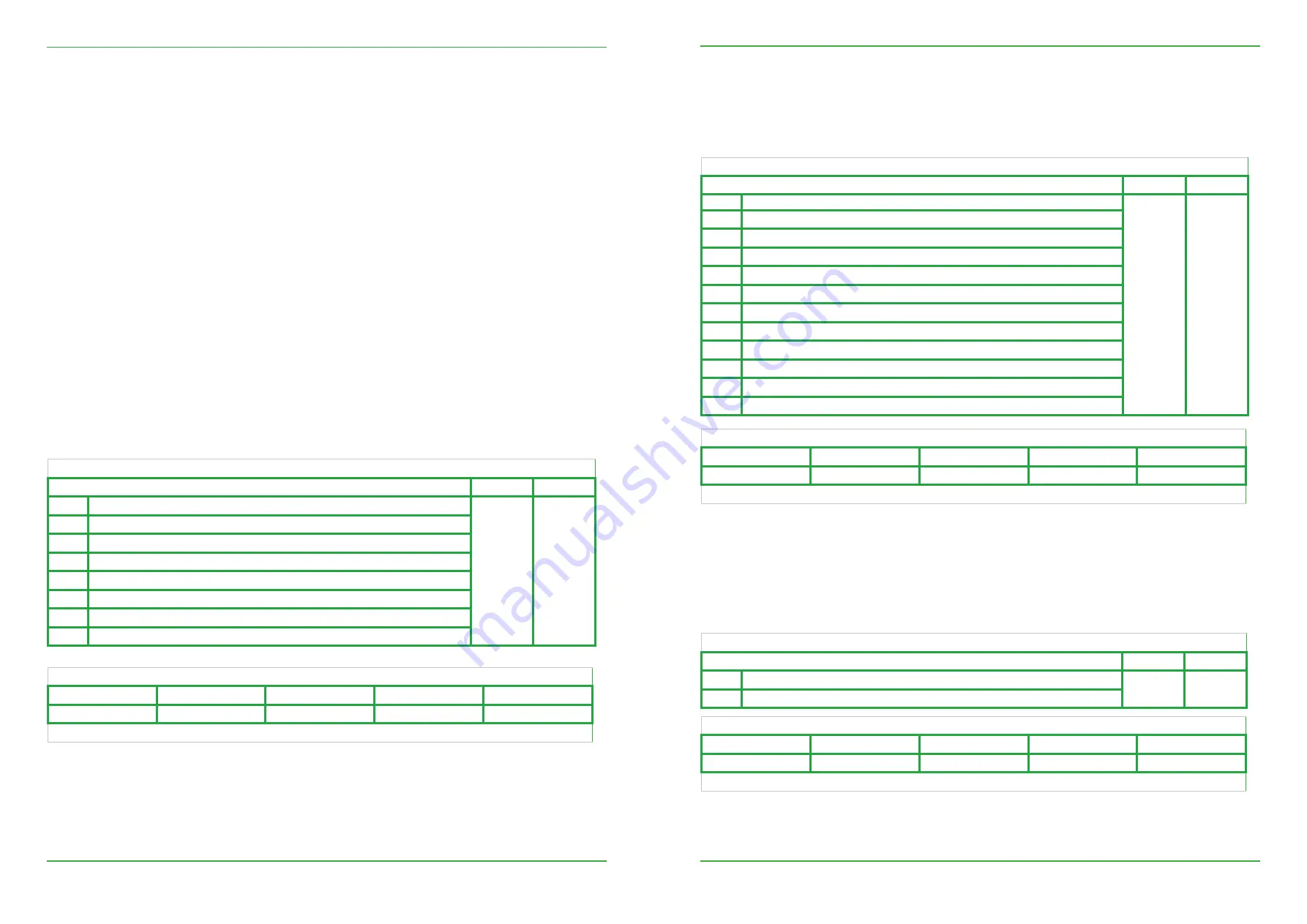
31
30
Operation and maintenance instructio
ns – CLASS UNIT TAC5
Operation and maintenance instruction
s – CLASS UNIT TAC5
- Conditions:
• Mode Airflow control or Demand control: during the initialization of the pressure alarm.
• Mode Pressure control: during the initialization of the pressure reference via airflow
- Causes:
The reference pressure (Paref) cannot be identified and the fans are stopped. 4 possibilities:
1.
Actual airflow < requested airflow: The requested working point is ‘too high’ (too high pressure loss)
for the maximal available pressure at the requested airflow for this fan.
2.
Actual airflow > requested airflow: the nominal airflow requested to initialize the pressure alarm
cannot be reached because the lower limit of the fan’s operating zone has been reached.
3.
Very unstable pressure (pumping).
4.
Assigned airflow not reached after 3 minutes.
If this occurs during initializing an alarm pressure, there are 2 options:
1.
No action is taken: the control will operate without a pressure alarm.
2.
Corrective action is taken (change the working point to one located in the working
zone of the fan, by reducing the pressure system, modifying the nominal airflow…) and restart the setup operation.
If this occurs during initializing of the assignment pressure in pressure control mode: Corrective action must be taken
(change the working point to one located in the working zone of the fan, by reducing the pressure system,
modifying the nominal airflow …) and restart the setup operation.
- Effects:
7.3 TYPE 3: ALARM REPORT DURING REFERENCE PRESSURE INITIALIZATION
Displayed on HMI TACtouch
Text displayed
LED ALARM
LED Pa
P.20
Initialisation of the reference pressure - Unstable supply air pressure
RED
/
P.21
Initialisation of the reference pressure - Unstable extract air pressure
P.22
Initialisation of the reference pressure - Supply air flow too low
P.23
Initialisation of the reference pressure - Extract air flow too low
P.24
Initialisation of the reference pressure - Supply air flow not reached
P.25
Initialisation of the reference pressure - Extract air flow not reached
P.26
Initialisation of the reference pressure - Supply air flow too high - Min. limit of the motor
P.27
Initialisation of the reference pressure - Extract air flow too high - Min. limit of the motor
TAC control board
AL1 relay
O.R.1
LED ALARM
LED AF
Fans
ALARM
/
ON
/
Stopped
Auto reset: no
- Conditions:
- Causes:
•
The setpoint cannot be fulfilled because the upper or lower limit of the fan’s working zone has been reached
- Effects:
- Conditions:
- Causes:
• Crucial data from the circuit board has been lost
- Effects:
- Solutions:
• Try a TOTAL RESET of the data using the advanced setup. If still not resolved, order a new circuit board.
7.4 TYPE 4: ALARM INDICATING THE SYSTEM CANNOT FULFIL THE SETPOINT
7.5 TYPE 5: ALARM INDICATING A DATA FAILURE IN THE CONTROL CIRCUIT
Displayed on HMI TACtouch
Text displayed
LED ALARM
LED Pa
S.11
“Constant Pressure” fan 1 - Measured pressure too high - Minimum air flow reached
RED
/
S.12
“Constant Pressure” fan 1 - Measured pressure too low - Maximum air flow reached
S.13
“Constant Pressure” fan 3 - Measured pressure too high - Minimum air flow reached
S.14
“Constant Pressure” fan 3 - Measured pressure too low - Maximum air flow reached
S.20
“Demand control” fan 1 - Air flow too low - Reduce the pressure on this fan
S.21
“Demand control” fan 1 - Air flow too high - Minimum limit of the motor reached
S.22
“Demand control” fan 2 - Air flow too low - Reduce the pressure on this fan
S.23
“Demand control” fan 2 - Air flow too high - Minimum limit of the motor reached
S.24
“Demand control” fan 3 - Air flow too low - Reduce the pressure on this fan
S.25
“Demand control” fan 3 - Air flow too high - Minimum limit of the motor reached
S.34
“Constant Air Flow” fan 3 - Air flow too low - Reduce the pressure on this fan
S.35
“Constant Air Flow” fan 3 - Air flow too high - Minimum limit of the motor reached
Displayed on HMI TACtouch
Text displayed
LED ALARM
LED Pa
D.10
Programme Error
RED
/
D.20
Data Error
TAC control board
AL1 relay
O.R.1
LED ALARM
LED AF
Fans
/
/
ON
/
/
Auto reset: yes
TAC control board
AL1 relay
O.R.1
LED ALARM
LED AF
Fans
Alarm status
/
ON
/
Stopped
Auto reset: no