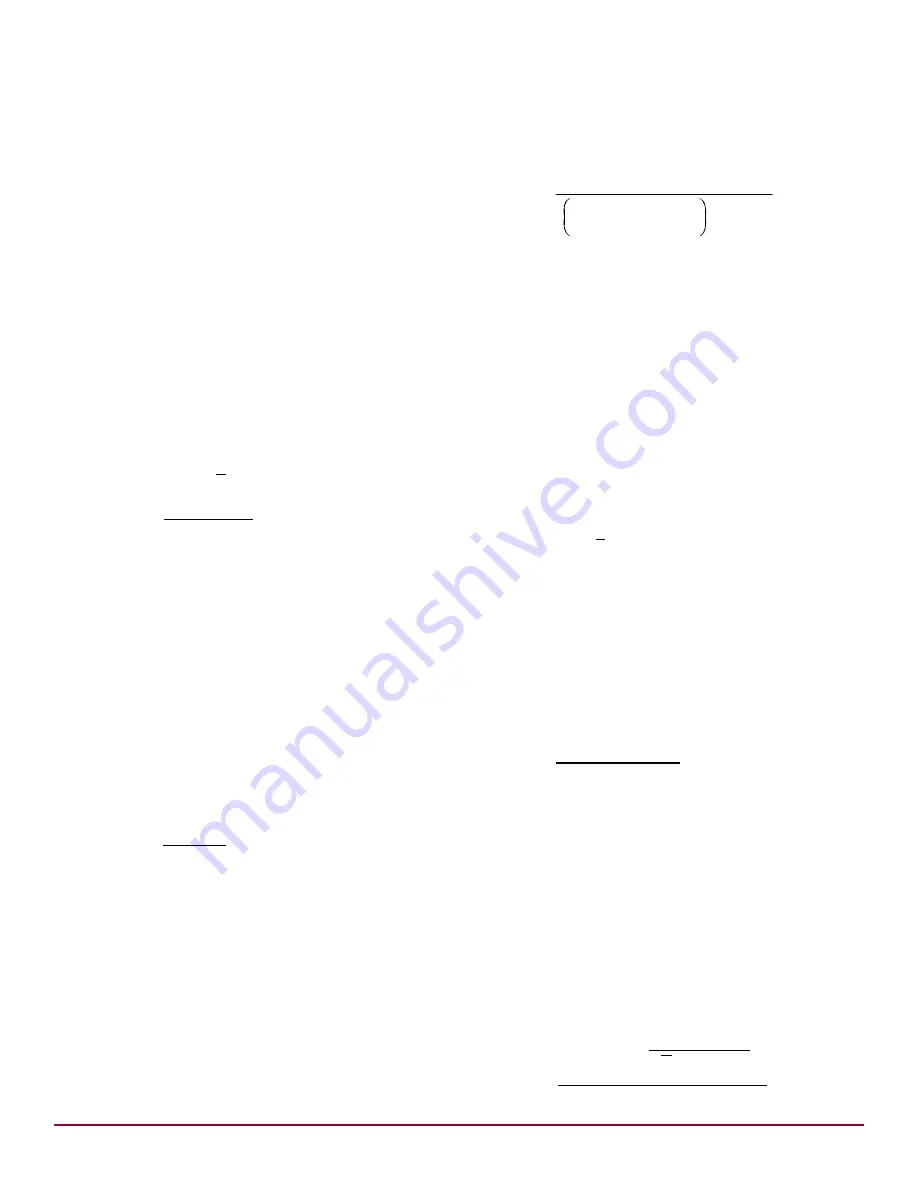
2
Supertex inc.
●
1235 Bordeaux Drive, Sunnyvale, CA 94089
●
Tel: 408-222-8888
●
www.supertex.com
AN-H48
Step 1: Switching Frequency and resistor (R
1
)
The switching frequency determines the size of the induc
-
tor L1 and size or type of input filter capacitor C
1
. A larger
switching frequency will result in a smaller inductor, but will
increase the switching losses in the circuit. For off-Line ap
-
plications, typical switching frequencies should be in range
20KHz-150KHz. The higher the input voltage range (for ex
-
ample in Europe 230VAC), the lower the frequency should
be to avoid extensive capacitive losses in the converter. For
North America AC line a frequency of f
S
= 100kHz is a good
compromise. From the datasheet, the oscillator resistor
needed to achieve this is 228kΩ.
Step 2: Choose the Input Diode Bridge (D1)
and the thermistor (NTC1)
The voltage rating of the diode bridge will depend on the
maximum value of the input voltage. The current rating will
depend on the maximum average current drawn by the con-
verter.
V
BRIDGE
= 1.5 • (√2 • V
MAX,AC
)
(1)
I
BRIDGE
=
V
O,MAX
• I
O,MAX
(2)
V
MIN, DC
• η
The 1.5 factor in equation (1) a 50% safety margin is more
than enough. For this design, choose a 400V, 1.0A diode
bridge.
Placing a thermistor (or resistor) in series with input bridge
rectifier will effectively limit the inrush charging current to in
-
put bulk capacitor C
1
during the initial start-up of the convert-
er. Except this useful action during very short time interval,
such a series element creates a unnecessary power loss
dissipation during normal operation of the converter, and
must be minimized. A good rule of thumb is that the thermis
-
tor should limit the inrush current to not more than five times
the steady state current as given by equation (2), assuming
maximum voltage is applied. The required cold resistance is:
R
COLD
=
V
BRIDGE
(3)
5 • I
BRIDGE
This gives us a 200Ω resistance at 25°C. Choose a thermis
-
tor with a resistance around 200Ω and rms current greater
than 0.2A for that application.
Step 3: Choose the Input Capacitors (C
1
/C
2
)
The first design criterion to meet is that the maximum LED
string voltage is should be less than half the minimum input
voltage to avoid having to implement a special loop compen-
sation technique. For this example, the minimum rectified
voltage should be:
V
MIN,DC
= 2 • V
O,MAX
= 80V
(4)
The hold-up and input filter capacitor required at the the di
-
ode bridge output have to be calculated at the minimum AC
input voltage. The minimum capacitor value can be calcu
-
lated as:
(5)
In this example,
C
1
≥ 26.45µF
.
Note: Equation (5) yields a conservative estimate to
for the least amount of capacitance required. It means
that the capacitor filter will normally care large ripple
content. Some electrolytic capacitors may not be able
to withstand such ripple current and minimum value of
C
1
capacitor may not be met, forcing the design to use
larger value capacitor. In the case where the allowable
ripple at the input of the buck converter is large, the
capacitor C
1
can be reduced significantly. See the Ap-
pendix for a more accurate calculation of the required
capacitor value.
The voltage rating of the capacitor should be more than the
peak input voltage with 10-12% safety margin.
V
MAX,CAP
≥ √2 • V
MAX,AC
→ V
MAX,CAP
≥ 191V
(6)
Choose a 250V, 33µF electrolytic capacitor.
Such electrolytic capacitors have a sizable ESR component.
The large ESR of these capacitors makes it inappropriate
to absorb the high frequency ripple current generated by
the buck converter. Thus, adding a small MLCC capacitor
in parallel with the electrolytic capacitor is a good option to
absorb the high frequency ripple current. The required high
frequency capacitance can be computed as:
C
2
=
I
O,MAX
• 25
(7)
(f
S
• 0.05 • V
MIN,DC
)
In this design example, the high frequency capacitance re
-
quired is about 250V, 22µF.
Step 4: Choose the Inductor (L1)
The inductor value depends on the ripple current in the
LEDs. Assume a +/- 15% ripple (a total of 30%) in the LED
current, an aggressive assumption would go up to +/-30% to
reduce the size of the inductor more than twice at the price
of reduced efficiency and, possibly, reduced LED lifetime.
Then, the inductor L1 can be computed at the rectified value
of the nominal input voltage as:
(8)
C
1
≥
V
O,MAX
x I
O,MAX
2 x V
2
MIN,AC
- V
2
MIN,DC
x η x freq
L1 =
V
O,MAX
x 1-
V
O,MAX
√2 x V
AC,NOM
0.3 x I
O,MAX
x f
S
]
]