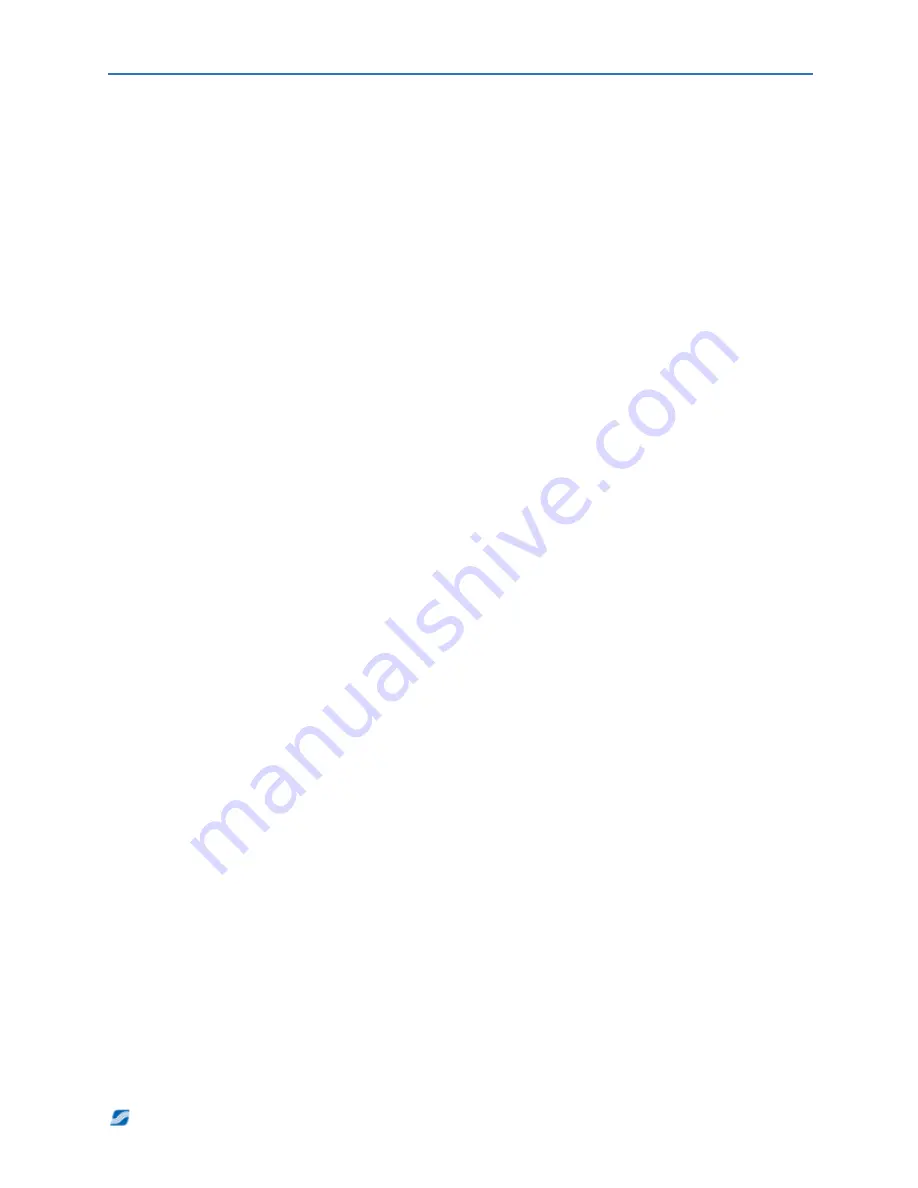
2-16 AC Motoring Chassis Dynamometer
2.5.2 Motor Identification (ID)
In order for the system to work properly and smoothly, the motor and controller must be
synchronized together or “mated”. This is done through a process using the local mode on the
controller panel. The Motor ID is done by SuperFlow prior to shipping but it can be done on site as
a test or motor operation check.
1. Remove the coupling between the AC Motor and dynamometer roll. The motor ID should be
done without any load on the motor.
2. Power the ABB drive.
3. Press the
Loc
Button.
4. Press the
Para
Button.
5. Navigate to the
99 -10
parameter using the up and down buttons.
6. Change 99-10 to
Standard
.
7. Press the Green Go Button.
8. The drive will perform the identification process which will take a few minutes.
9. After it finishes the drive will display
ID Done
.
10. Press the
Rem
Button to place the drive in remote mode.
2.5.3 Remote Control Test
From the dyno handheld set the controller to speed mode by pressing the
blue arrow
button then
the
Modes
(J) button. Press the A or B buttons to select speed and press
Done
. Set the ABB
controller to remote by pressing the Rem button. Increase the load control to 10 and the motor
should start turning. Decrease the load control to 0 and the motor should stop turning. Switch the
motor off from WinDyn.
2.5.4 Torque Calibration
Any load (positive or negative) applied by the AC Motor is measured by an in-line torque sensor
mounted on the roll-to-motor drive shaft. This torque is used in the total power calculations for a
vehicle under test on the dynamometer.
Calibration information on the Interface in-line torque transducer is used to generate a coefficient
that converts the voltage output to torque. This coefficient is entered into the system configuration
file and should be accurate for all applications. However, the torque readings can be verified if
desired using the following procedure.
Further detailed information for this section is pending.