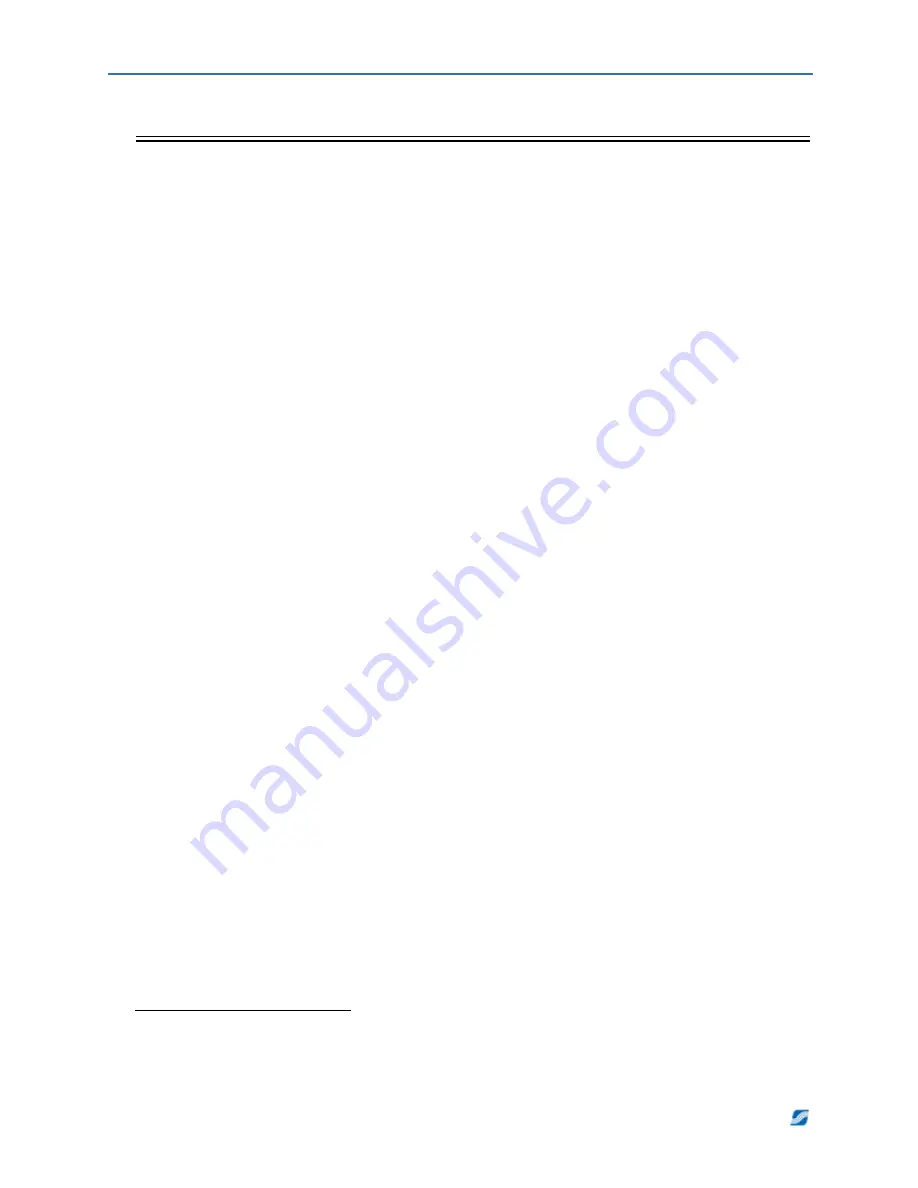
Carbon Monoxide Warnings
SuperFlow Technologies Group 1-5
1.5 Carbon Monoxide Warnings
When operating fuel-generated equipment in enclosed areas, take the following precautions to
protect you and your employees against carbon monoxide exposure.
What is carbon monoxide?
1
Carbon monoxide (CO) is a poisonous, colorless, odorless, and tasteless gas. Although it has no
detectable odor, CO is often mixed with other gases that do have an odor; therefore, you can
inhale carbon monoxide right along with gases you can smell and not even know that CO is
present.
CO is a common industrial hazard resulting from the incomplete burning of natural gas and any
other material containing carbon such as gasoline, kerosene, oil, propane, coal, or wood. One of
the most common sources of exposure in the workplace is the internal combustion engine.
How does CO harm you?
Carbon monoxide is harmful when breathed because it displaces oxygen in the blood and
deprives the heart, brain, and other vital organs of oxygen. Large amounts of CO can overtake you
in minutes without warning—causing you to lose consciousness and suffocate.
Besides tightness across the chest, initial symptoms of CO poisoning may include headache,
fatigue, dizziness, drowsiness, or nausea. Sudden chest pain may occur in people with angina.
During prolonged or high exposures, symptoms may worsen and include vomiting, confusion,
and collapse in addition to loss of consciousness and muscle weakness. Symptoms vary widely
from person to person. CO poisoning may occur sooner in those most susceptible: young children,
elderly people, people with lung or heart disease, people at high altitudes, or those who already
have elevated CO blood levels such as smokers. CO poisoning poses a special risk to fetuses.
Acute poisoning may result in permanent damage to the parts of your body.
How can employers help prevent CO poisoning?
To reduce the chances of CO poisoning in your workplace:
• Install an effective ventilation system that will remove CO from work areas.
• Maintain equipment and appliances that can produce CO to ensure they are in good
working order, promote their safe operation, and reduce CO formation.
• Consider switching from gasoline-powered equipment to equipment powered by
electricity, batteries, or compressed air if it can be used safely.
• Prohibit the use of gasoline-powered engines or tools in poorly ventilated areas.
• Provide personal CO monitors with audible alarms if potential exposure to CO exists.
• Test air regularly in areas where CO may be present, including confined spaces.
• Install CO monitors with audible alarms.
1. Information in this section was adapted from the “OSHA Fact Sheet,” U.S. Department of Labor, Occupational Safety
and Health Administration, 2002,
http://www.osha.gov/OshDoc/data_General_Facts/carbonmonoxide-factsheet.pdf
February 2007.