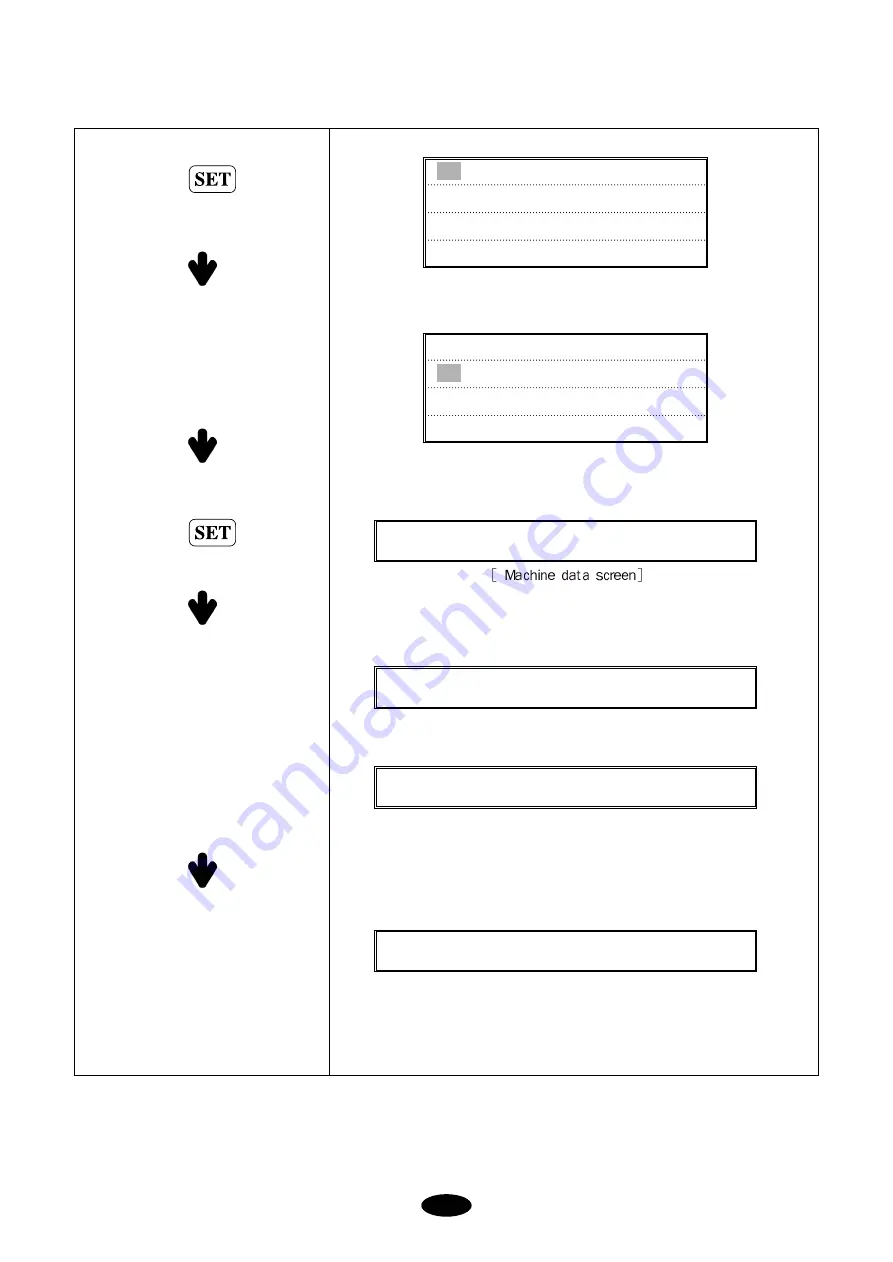
7-5
You will see this message on your
VFD start screen if you selected
WHEEL.
Move the cursor to
“
13. EXIT
”
to go
to the new program.
You will see this message on your
start screen if you selected SPRING.
After the machine is automatically
rebooted, check if the VFD screen
correctly displays your selection.
Check the version as well.
= = = S W F [ W ] B / V x . x x = = =
S Y S T E M C H A N G E . . .
= = = S W F [ S ] B / V x . x x = = =
[ U K 1 2 0 6 ] x x x x / x / x x
Press
Press
12. MACHINE SETTING
13. EXIT
12. MACHINE SETTING
13. EXIT
※
If you skip
“
12. MACHINE SETTING
”
and go straight to
“
13. EXIT,
”
the machine will ask for your machine set-up.
“
12. MACHINE SETTING
”
will automatically appear on the screen.