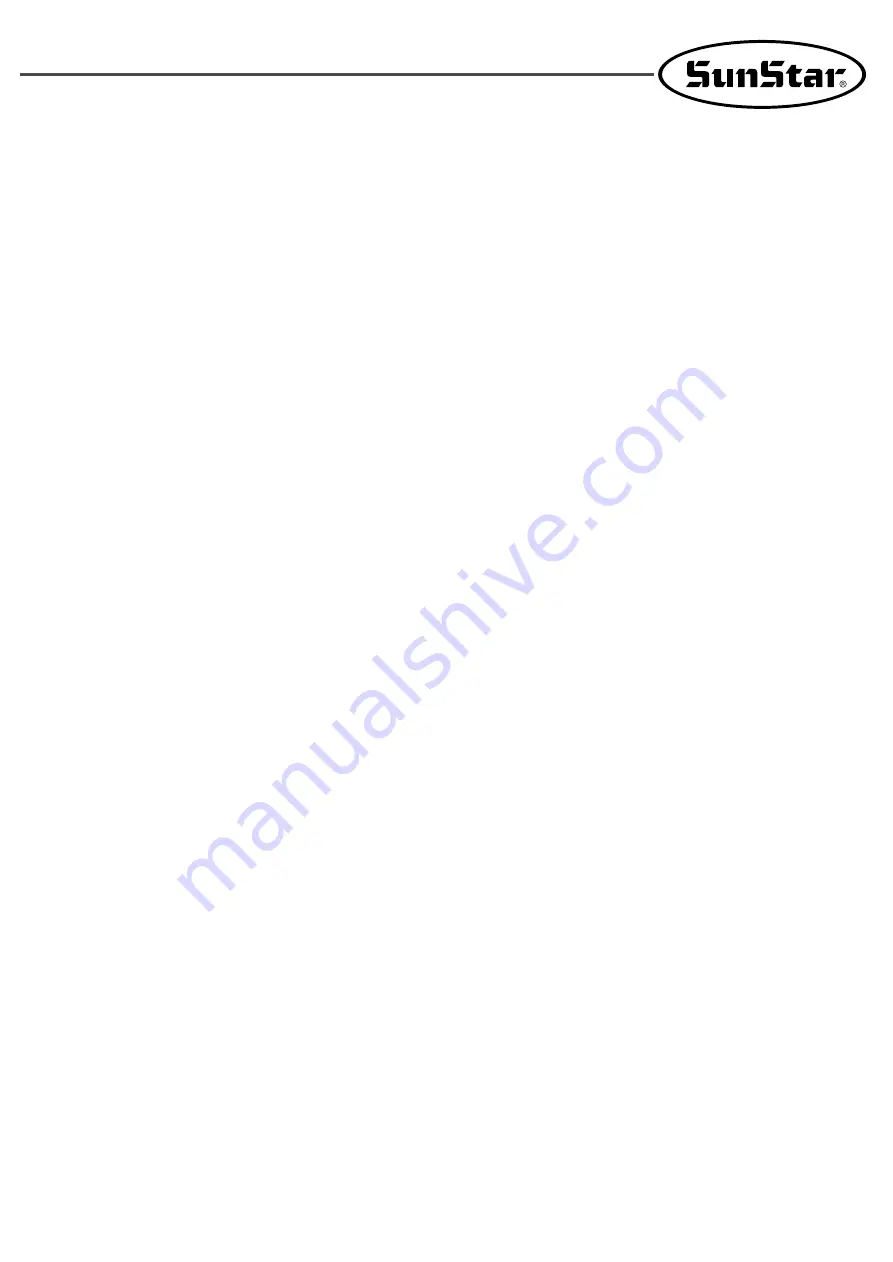
5
3) Safety Guide
● Caution / Installation of the Machine
▶The machine has to install autherized engineer only.
▶Contact the Sunstar dealer from whom you purchased your machine or ask an authorized
technician for installation.
▶Because weights of this sewing machine is about 60Kg, in case of the moving the machine it
is required a minimum two person at least.
▶Make sure to keep this sewing machine away from other machines that generate electric noise
such as high frequency welding machines. Such electric noise may cause the malfunction of
this sewing machine.
▶Do not plug in the machine before completing its installation. If pedal is pressed by your
mistake, it is caused injury of operator
▶Be sure to cover the motor and the belt with provided for connected belt pant between motor
and machine head.
▶Never operate the machine without oil lubrication.
▶Check the voltage and phase whether it is correct on the marked specilication of Motor name
plate or not.(phase : single or 3 phase)
▶All electric wires must be installed to have a minimum distance at 25mm from operating parts
of machine. Check the installation whether wire is overly pressed by the fixture for avoiding
the risk of electric shock or fire
▶In case of using a table with wheel for the machine, fix the wheels.
▶Because of the heavy weight of the machine, a minimum of two person must be involved in
titling the machine back or return.
▶When handling the lubricant for the machine, wear glasses and gloves to protect your eyes
and skin from the oil. Do not drink the lubricant and keep it away from children.
Summary of Contents for KM-818
Page 21: ...Table drawing 7 7 21 1 KM 818 1 ...
Page 22: ...22 2 KM 818 2 ...