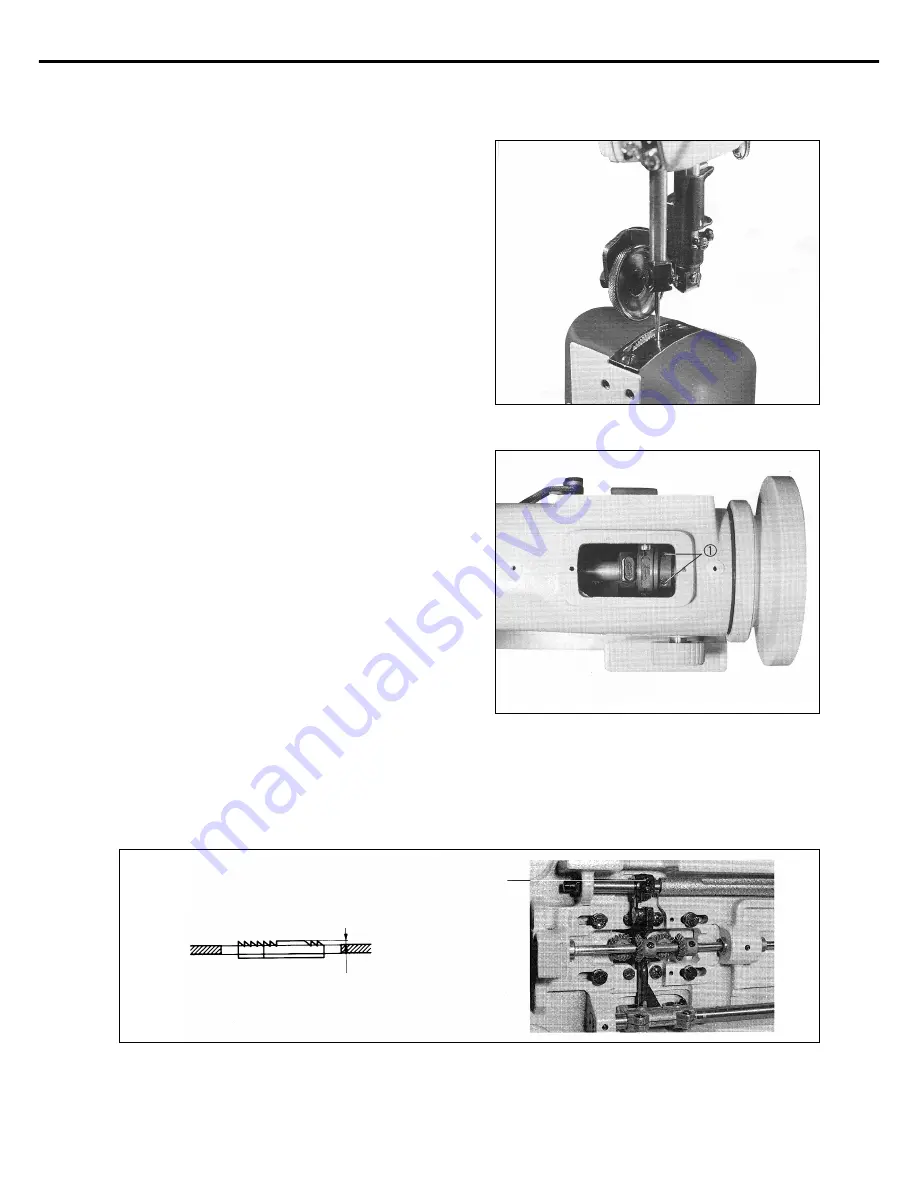
18
9) Adjusting timing of needle and feed dog
As in the figure, it is normal that the upper part of feed dog
goes down and the needle hole meets the upper part of needle
plate. If not, loosen the feed cam screws
①
and move the cam
position right and left to the proper match. If gear moves faster
than needle, turn the feed cam to the opposite direction of the
machine rotation. If t gear moves slower than needle, rotate to
the proper match.
[Figure 19]
[Figure 20]
10) Adjusting height of feed dog
The normal adjustment is as follows. Turn pulley to place feed dog at the height point. And loosen lifter crank clamp screw
①
to
move the crank up and down. After that, make the crank protrude 1mm in parallel with the upper needle plate and fix the gear.
[Figure 21]
①
About 1mm