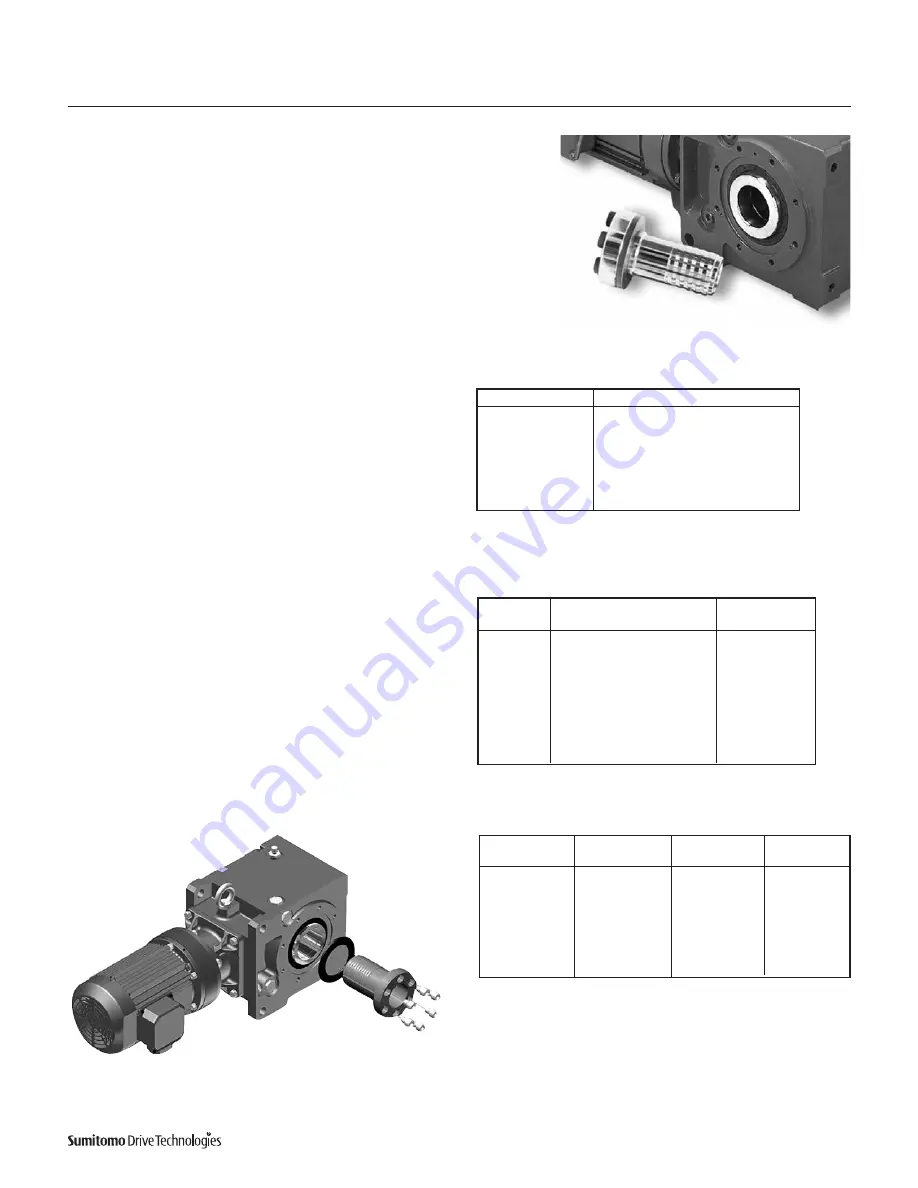
Inch
Tolerance
Metric mm
Tolerance*
1
11
/
16
- 1
15
/
16
+.003 /.001
40-50
.064 /.025
2 - 2
7
/
16
+.003 /.001
50-65
.076 /.030
2
1
/
2
- 3
7
/
16
+.003 /.001
65-80
.076 /.030
3
1
/
2
- 3
15
/
16
+.003 /.001
80-100
.090 /.036
Shaft Dia.
Tolerance
3
/
4
" - 1
1
/
8
"
+0 - .005"
1
3
/
16
" - 2"
+0 - .006"
2
1
/
16
" - 3
1
/
8
"
+0 - .007"
3
3
/
16
" - 4
3
/
4
"
+0 - .008"
Taper Grip
®
Bushing
Size
Screw Size
Screw Torque
Qty. & Code
lb. ft.
A
6 X M12
112E7003
56
B
6 X M12
112E7003
104
C
6 X M16
112G7003
185
D
6 X M16
112G7003
185
E
8 X M16
112G7003
185
Figure 1.
PERMISSIBLE SHAFT TOLERANCE
Figure 2.
BUSHING SCREW TIGHTENING TORQUES
*Metric Tolerances are F8.
NOTE:
Shaft runout TIR should be no greater than .001".
Figure 3.
BUSHING BORE TOLERANCES
NOTE:
Shaft runout TIR should be no greater than .001".
NOTE:
Similar to all shrink disk type devices. It is essential to properly
assemble and tighten the mounting bolts. Carefully follow the Sumitomo
instructions for selection and installation in order to avoid any slippage.
Incorrect mounting or slippage of the bushing will impair function and
removal of the drive.
Fitting the Reducer on the Shaft
1. Check the size and condition of the shaft to which the reducer will
be fitted. Permissible shaft tolerances are given in Figure 1.
2. Ensure all mating surfaces of the hub, the inside and outside diam-
eters of the Taper-Grip
®
bushing and the shaft are free from burrs
and corrosion. Clean each surface with a solvent to REMOVE ALL
TRACES OF GREASE AND OIL.
3. Lightly oil each screw and insert into the bushing flange; ensure
they do not protrude beyond the rear face.
4. Slide the thrust collar onto the Taper-Grip
®
bushing, ensuring that it
is located immediately behind the flange. Screw the Taper-Grip
®
bushing into the hub in a clockwise direction until the flange con-
tacts the thrust collar.
5. Unscrew the Taper-Grip
®
bushing until a gap of 1mm minimum
exists between the flange and thrust collar. Tighten all screws until
they are finger tight.
6. Slide the reducer onto the shaft at least as far as the counter bore
in the Taper-Grip
®
bushing. Gradually tighten each screw in a star
pattern to the torque levels shown in Figure 2.
7. Install the torque arm assembly if one is used.
8. After mounting is complete, the Cyclo BBB can then be filled with
oil. Please follow proper guidelines for oil lubrication. Grease lubri-
cated units are pre-filled at the factory.
9. After the reducer has been running for 20 or 30 hours, re-tighten
the screws to the torque values listed in Figure 2. Screw torque
should be subsequently checked at normal service intervals.
1
Cyclo
®
BBB