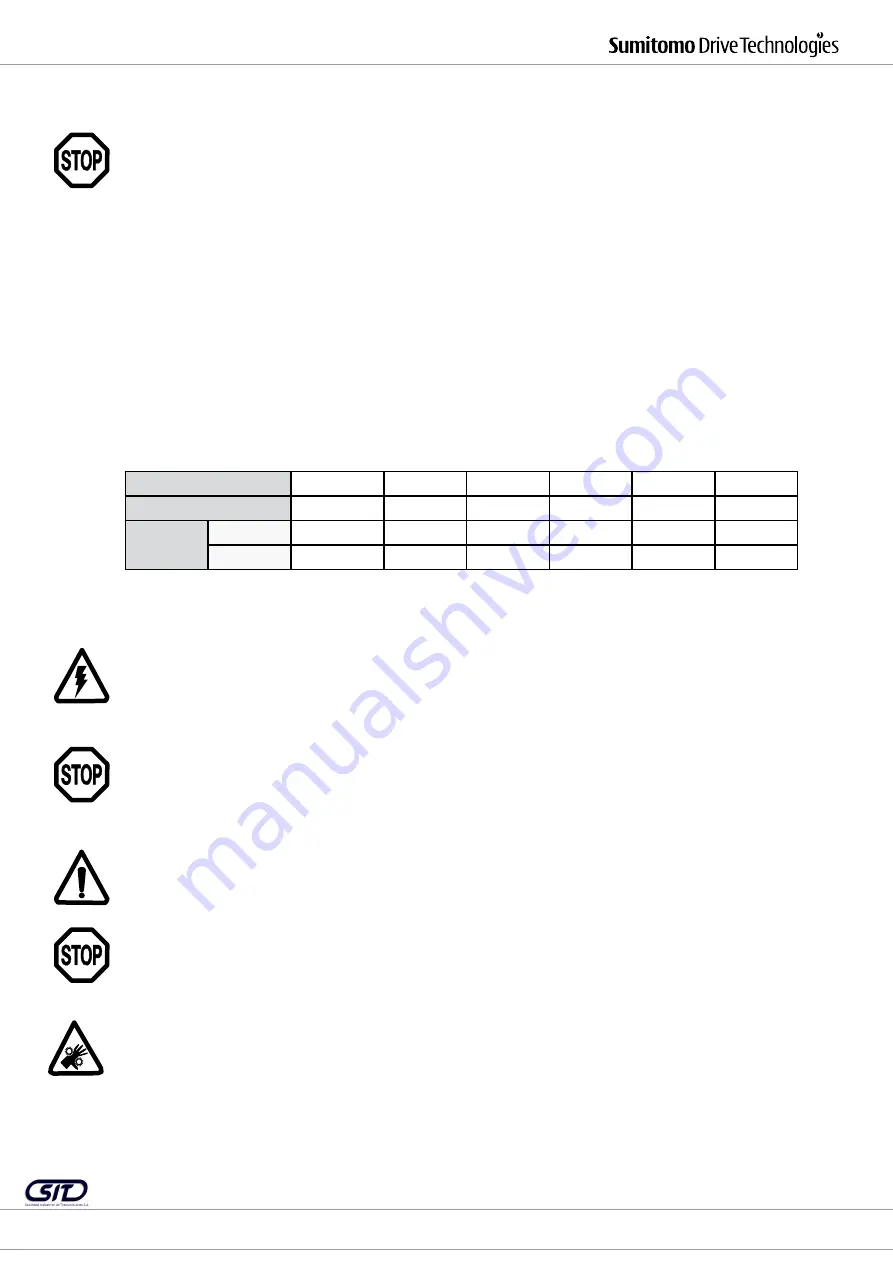
PARAMAX SFC Operating Manual
e-mail: [email protected]
www.sumitomodriveeurope.com
Tel. +49 (0) 8136 66 0
Cyclostraße 92
85229 Markt Indersdorf
29
PX_SFC_DEU_ENG_11_09_991131
The drive unit is to be set up so that inspection, maintenance, and other operations such as lubricant
top-ups, can be carried out easily.
In order to prevent overheating and risk of fire, ventilation of the PARAMAX SFC gearbox should not be
obstructed.
Tighten the mounting bolts to the specified torque only after carefully establishing perfect evenness
over the entire surface of the mounting base, which should provide torsional stiffness and vibration
damping, and after aligning the drive. After about 4 weeks, all mounting bolts should be checked again
to ensure the correct tightening torque.
We recommend using mounting bolts of DIN quality 10.9.
If the drive is to be loaded up to maximum output torque or maximum transverse force, positive-fit con-
nections (e.g. DIN 6325 cylinder pins) should be provided in addition to the foot mounting bolts.
5.2 Installation
Table 1 Mounting screw torques
* Screw class ISO 898-1/8.8
Mos2 paste is recommended for preventing electrochemical corrosion between the PARAMAX SFC gear
and the work machine when different metals are connected together, for example cast iron and stainless
steel.
The housing should also be grounded, using the grounding screws on the motor.
If the drive is to be painted over or partially re-finished, first ensure that the vent valve and shaft seals
are carefully masked off. Remove the masking tape after the painting work is completed.
PARAMAX SFC gear units should not be used for any purposes other than those indicated on the model
plate or in the manufacturer’s documentation; otherwise there is a risk of electric shocks, injuries, or
damage to the equipment.
Do not place any inflammable objects near the unit, otherwise there is a risk of fire.
Do not place near the PARAMAX SFC gear unit any objects that obstruct the ventilation. Insufficient ven-
tilation can lead to overheating, and therefore a risk of burning or fire.
Do not step on or hold onto the PARAMAX SFC gear unit, as this may cause injuries.
Installation size
SFC045
SFC055
SFC060
SFC065
SFC070
SFC075
Screw size *
M24
M30
M30
M30
M36
M36
Torque
Nm
706
1400
1400
1400
2430
2430
in lbs
6250
12390
12390
12390
21510
21510
SIT S.A. | Tfno. 943 457200 | [email protected] | www.sitsa.es
SIU 8320-00
Instrucciones de instalación y mantenimiento Reductores PARAMAX SFC para Torres de Refrigeración
20/03/2018