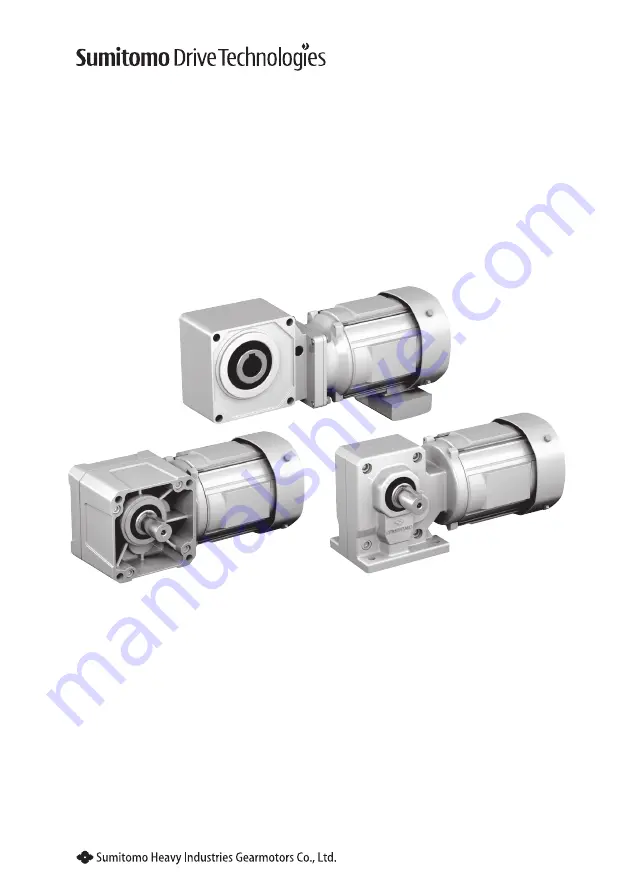
HYPONIC DRIVE®
■Gearmotors and reducers should be handled, installed, and maintained by trained technicians.
Carefully read the instruction manual before use.
■A copy of this instruction manual should be sent to the actual user.
■This instruction manual should be retained by the user for future reference.
《CAUTION》
No.NM2201E-6
Instruction Manual