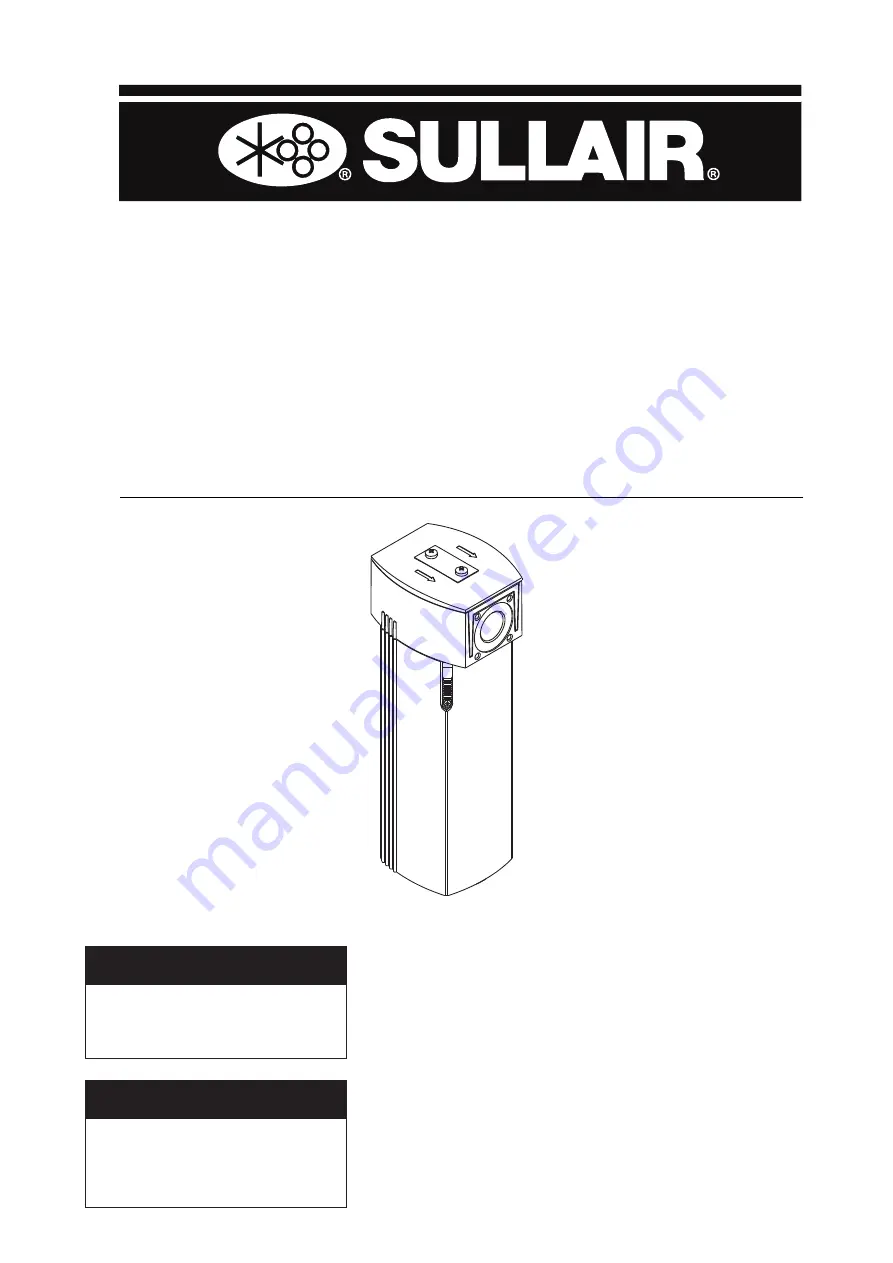
SAFETY WARNING
Users are required to read
the entire User Manual before
handling or using the product.
Keep the User Manual in a safe
place for future reference.
WARRANTY NOTICE
Failure to follow the instructions
and procedures in this manual or,
misuse of this equipment will
VOID its warranty!
MANUAL PART NUMBER:
02250247-389 R02
©SULLAIR LLC
USER MANUAL
SXT - SXCS - SXF - SXH
THREADED FILTERS
COALESCING FILTERS