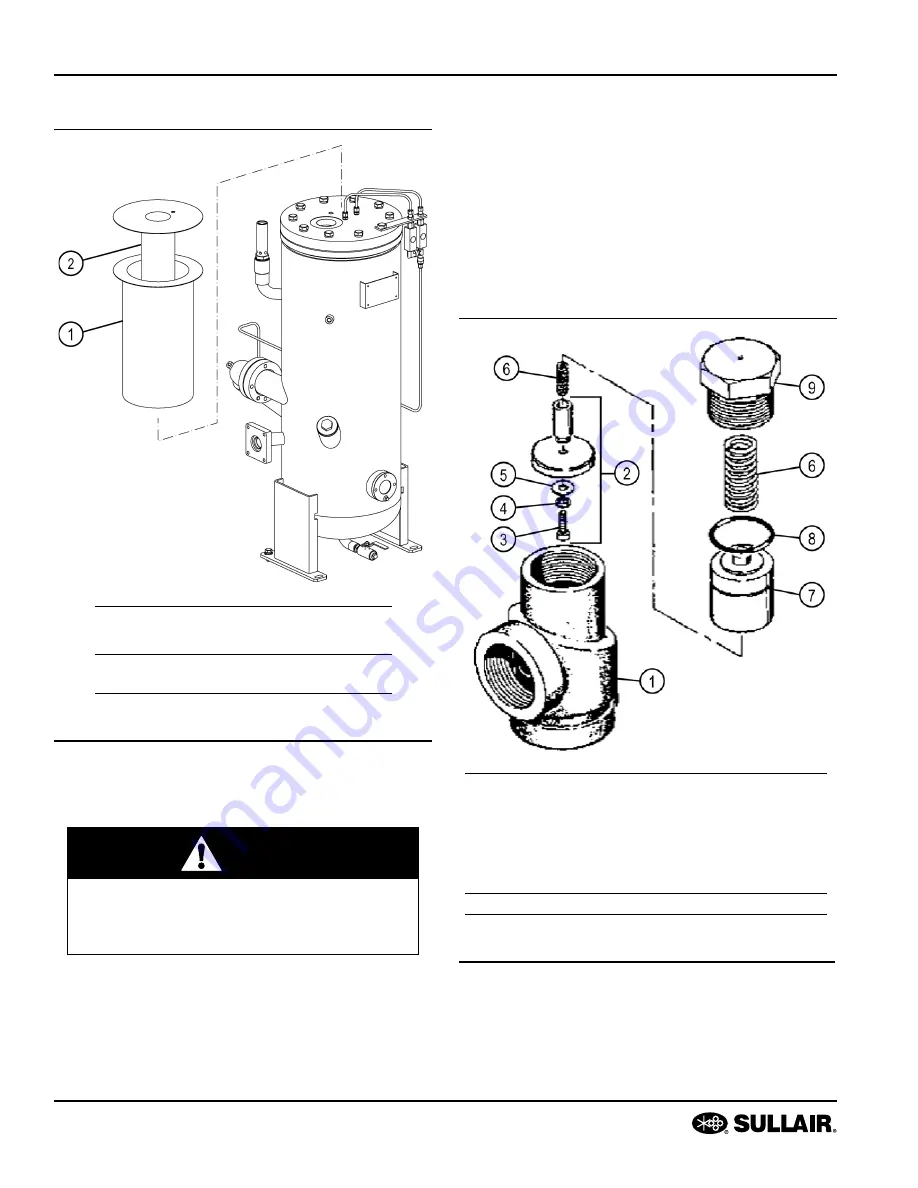
6: Maintenance
ShopTek™ ST45, ST55, ST75 (U.S.A. & Mexico) Operation & Maintenance Manual
88292021-240 R01
38
Subject to EAR, ECCN EAR99 and related export control restrictions.
7. Install the new primary & secondary fluid/air
separator elements and gasket assembly.
8. Reassemble in reverse order, carefully
adjusting the purge oil return line tube so it
has the correct clearance from the separator
element base (see
Section 6.4.5: Purge oil
return line filter maintenance
).
9. Evenly tighten the separator cover bolts to
138 N m (102 lbf ft).
10. Check the continuity of the separator ele-
ment to the ground.
11. Re-tension the separator cover bolts after
the compressor has reached operating tem-
perature.
6.4.7
Minimum pressure valve
maintenance
1. Shut down the compressor and bleed pres-
sure to zero.
CAUTION
Do not remove the staples incorporated into the
gaskets.They maintain a ground contact with the
separator.
Figure 6-5: Fluid/air separator tank
1. Primary fluid/air separator element
1
2. Secondary fluid/air separator element
2
1
Primary element part number: 250042-862
2
Secondary element part number: 02250061-137
Figure 6-6: Minimum pressure valve
1. Valve body
6. Spring
2. Check valve assembly
7. Piston
3. Hex head set screw
8. O-ring
4. Spring lock washer
9. Top cap
5. Gasket
Minimum pressure valve repair kit part number: 88290018-146