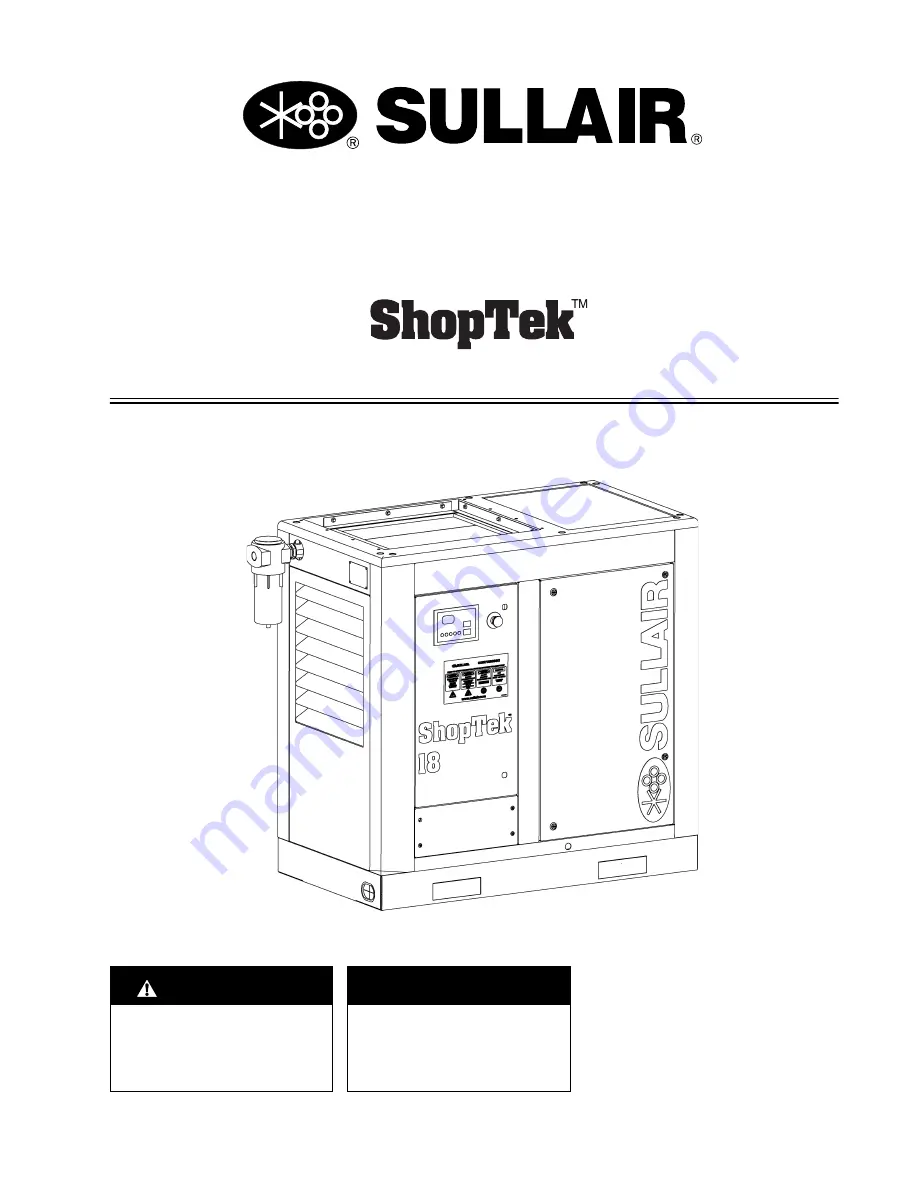
ST18 & ST22
U.S.A. & Mexico
PART NUMBER:
88291013-137 R05
The information in this manual is current as of its
publication date and applies to compressors with
serial number
:
37215080087
and all subsequent serial numbers.
OPERATION & MAINTENANCE MANUAL
Publication date: 11/25/2015
Copyright © 2014 – 2015 Sullair, LLC. All rights reserved.
Subject to EAR, ECCN EAR99 and related export control restrictions.
WARRANTY NOTICE
Failure to follow the instructions
and procedures in this manual,
or misuse of this equipment, will
void
its warranty.
SAFETY WARNING
Users are required to read the
entire Operation & Maintenance
Manual before handling or using
the product.