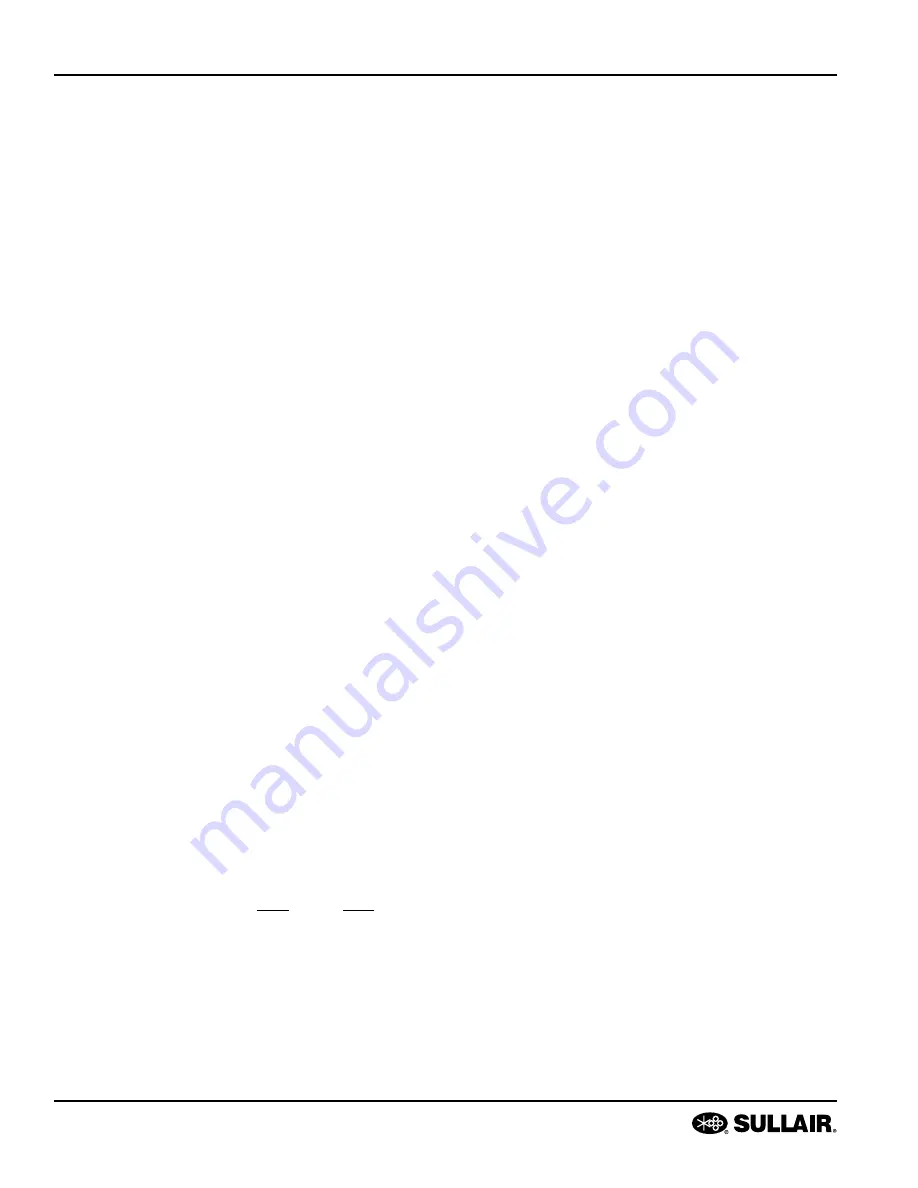
1: Safety
185 T3 Kubota User Manual
02250223-054 R01
6
Subject to EAR, ECCN EAR99 and related export control restrictions.
trical or other energy source, would cause personal injury
or equipment damage. The power source on any
machine shall be locked out by each employee doing the
work except when motion is necessary during setup,
adjustment or trouble-shooting.
A.
The established procedures for the application of
energy control shall cover the following elements and
actions and shall be initiated only by Authorized Per-
sons and done in the following sequence:
1. Review the equipment or machine to be
locked and tagged out.
2. Alert operator and supervisor of which
machine is to be worked on, and that power
and utilities will be turned off.
3. Check to make certain no one is operating
the machine before turning off the power.
4. Turn off the equipment using normal shut-
down procedure.
5. Disconnect the energy sources:
a. Air and hydraulic lines should be bled,
drained and cleaned out. There should
be no pressure in these lines or in the
reservoir tanks. Lockout or tag lines or
valves.
b. Any mechanism under tension or pres-
sure, such as springs, should be
released and locked out or tagged.
c. Block any load or machine part prior to
working under it.
d. Electrical circuits should be checked with
calibrated electrical testing equipment
and stored energy and electrical capaci-
tors should be safely discharged.
6. Lockout and/or Tagout each energy source
using the proper energy isolating devices
and tags. Place lockout hasp and padlock or
tag at the point of power disconnect where
lockout is required by each person perform-
ing work. Each person shall be provided with
their own padlock and have possession of
the only key. If more than one person is
working on a machine
each
person
shall
affix
personal lock and tag using a multi-lock
device.
7. Tagout devices shall be used only when
power sources are not capable of being
locked out by use of padlocks and lockout
hasp devices. The name of the person affix-
ing tag to power source must be on tag along
with date tag was placed on power source.
8. Release stored energy and bring the equip-
ment to a “zero mechanical state”.
9. Verify Isolation: Before work is started, test
equipment to ensure power is disconnected.
B.
General Security
1. The lock shall be removed by the “Autho-
rized” person who put the lock on the
energy-isolating device. No one other than
the person/persons placing padlocks and
lockout hasps on power shall remove pad-
lock and lockout hasps and restore power.
However, when the authorized person who
applied the lock is unavailable to remove it
his/her Supervisor may remove padlock/pad-
locks and lockout hasps and restore power
only if it is first:
a. verified that no person will be exposed to
danger.
b. verified that the “Authorized” person who
applied the device is not in the facility.
c. noted that all reasonable efforts to con-
tact the “Authorized” person have been
made to inform him or her that the lock-
out or tagout device has been removed.
d. ensured that the “Authorized” person is
notified of lock removal before returning
to work.
2. Tagout System—Tags are warning devices
affixed at points of power disconnect and are
not to be removed by anyone other that the
person placing tag on power lockout. Tags
shall never be by-passed, ignored, or other-
wise defeated.
1.12 Jump starting
A.
Observe all safety precautions mentioned elsewhere
in this manual.
B.
Batteries may contain hydrogen gas which is flam-
mable and explosive. Keep flames, sparks and other
sources of ignition away.
C.
Batteries contain acid which is corrosive and poison-
ous.
DO NOT
allow battery acid to contact eyes, skin,
fabrics or painted surfaces as serious personal injury
or property damage could result. Flush any con-
tacted areas thoroughly with water immediately.
Always wear an acid-resistant apron and face shield
when attempting to jump start the compressor.