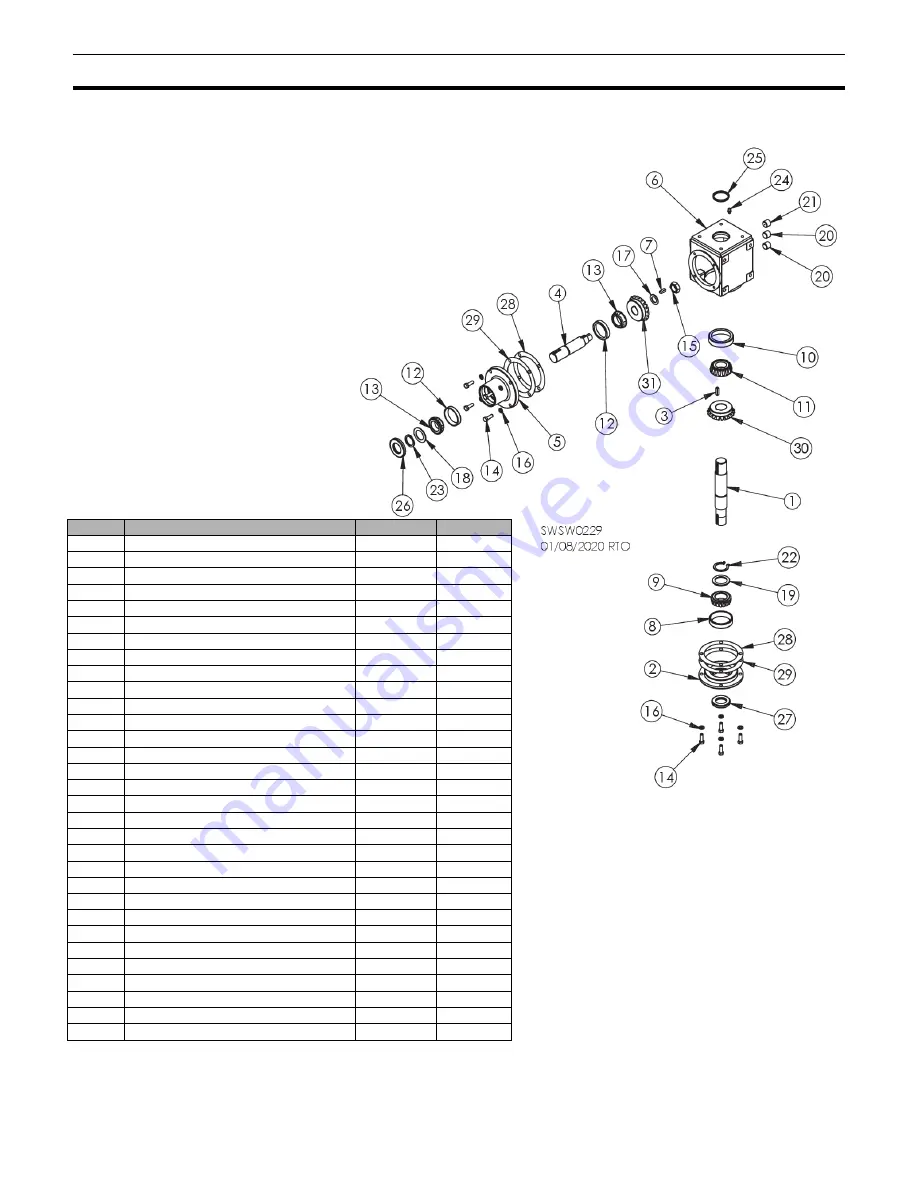
Parts/Assemblies
34
TOP GEARBOX
REF. #
DESCRIPTION
QTY.
PART #
1
Sprocket shaft
1
E5379
2
Plate, open end
1
E5902-01
3
Key,1/4" x 1"
1
E5915
4
Shaft, 8"
1
EU0839
5
Output hub, 1-1/4" shaft
1
EU0840
6
Gearbox case
1
F9004
7
Key, 1/4" sq. x 3/4"
1
G7508
8
Bearing cup, 2-23/32 OD
1
J0115
9
Tapered bearing, 1-3/8”
1
J0120
10
Bearing cup
1
J0125
11
Tapered bearing, 1-1/4”, .94
1
J0130
12
Bearing cup
2
J0133
13
Tapered bearing,1-1/4”
2
J0134
14
Screw, 5/16 – 18 x 1
8
J0527
15
Lock nut, 3/4" - 16
1
J1055
16
Split lock washer, 5/16”
8
J1200
17
Machine bushing, 3/4 x 1-1/4”, 14ga
1
J1260
18
Machine bushing, 1-1/4”, 14ga
1
J1273
19
Machine bushing, 1-3/8”, 10ga
1
J1275
20
1/2" center sunk hex head plug
2
J2615
21
1/2” center sunk head vented plug
1
J2616
22
Snap ring, 1.37”
1
J3589
23
Snap,ring,1-3/4”
1
J35981
24
Drive-in grease zerk, 1/4"
1
J3605
25
Soft plug,1-7/8”
1
J6980
26
Seal, 1-1/4 2.378
1
J7005
27
Seal,1-3/8” x 2.129, r/c
1
J7010
28
Plastic shim, 0.003” thick
As needed
J7090
29
Plastic shim, 0.010 thick
As needed
J70901
30
Beveled gear, 18-tooth,1-1/4" bore
1
J8528
31
Beveled gear, 18-tooth, 1" bore
1
J8529
Summary of Contents for U-Trough Power Sweep
Page 3: ...Limited Warranty 3 ...
Page 26: ...Parts Assemblies 26 PARTS ASSEMBLIES COMPLETE U TROUGH ...
Page 28: ...Parts Assemblies 28 U TROUGH BODY ASSEMBLY ...
Page 30: ...Parts Assemblies 30 U TROUGH POWER SWEEP DRIVE HOUSING ...
Page 38: ...Parts Assemblies 38 U TROUGH 20 INCLINE POWERHEAD EU1180 ...