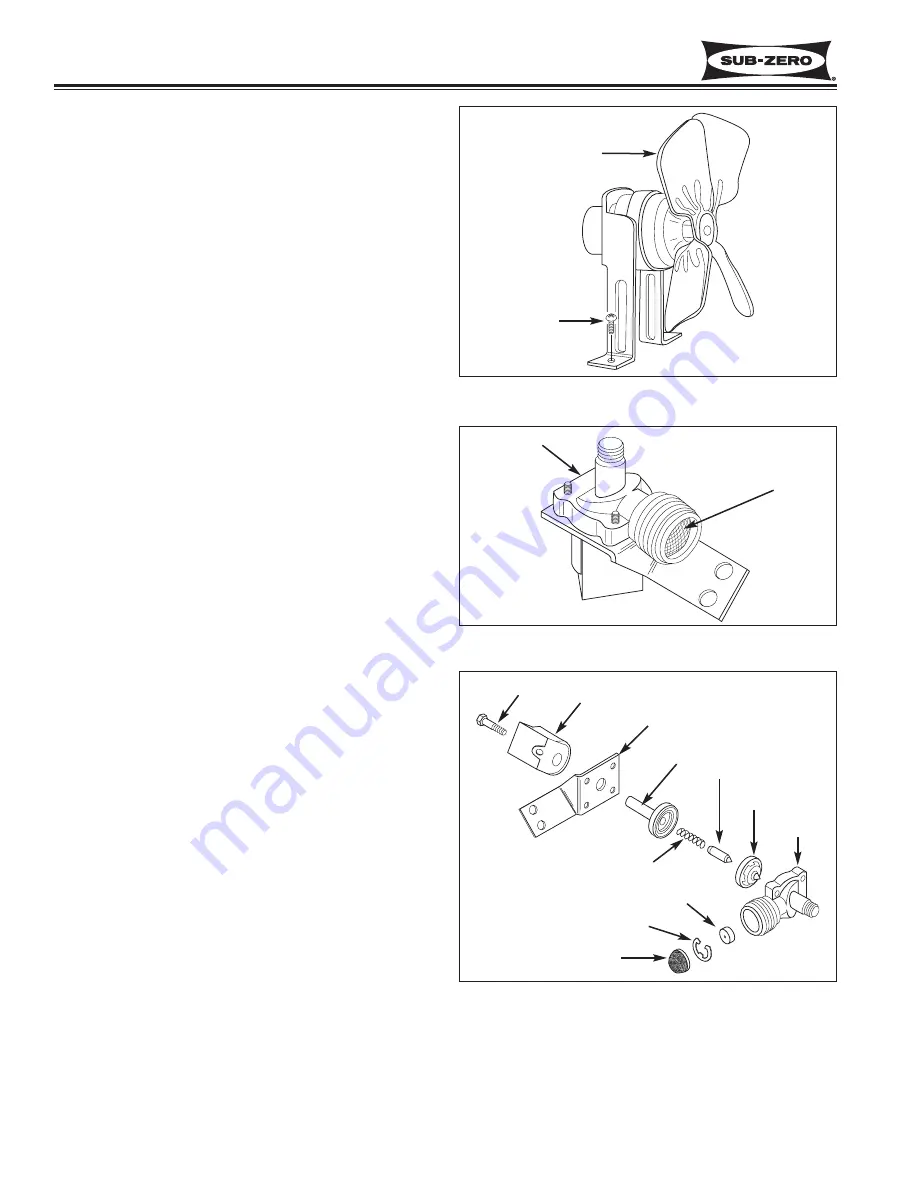
Page 37
Component Access & Removal
Model 506 (UC Ice Maker)
Model 506 (UC Ice Maker)
4-12
#3752200 - Revision B - May, 2006
Condenser Fan
The condenser fan has a 3-watt motor that turns the fan
blade at 1200 RPM. When facing the motor shaft, the
fan blade will turn counterclockwise. To check or
remove the condenser fan, the unit compartment will
need to be pulled out of the unit.
To check:
1.
After removing the wire leads, use an ohmmeter set
on the R x 1 scale.
2. Check across terminals. The ohmmeter should
read approximately 75 ohms.
The motor can also be checked by attaching a 120 volt
test cord to the terminals. When power is supplied, the
fan should operate.
To remove:
1. Remove screws that secure the fan bracket to the
base of the unit compartment.
2. Pull out the fan and bracket.
3. Remove the screws that secure the fan to the fan
bracket.
Water Inlet Valve
The water inlet valve is located in the front of the unit
compartment. The valve features a spring-loaded sole-
noid and has an 80-mesh screen in the water inlet.
To check:
1. After removing the wire leads, use an ohmmeter set
on the R x 100 scale.
2. Test across the terminals. The ohmmeter should
read approximately 250 ohms.
A flow washer in the water inlet valve controls water
flow to approximately 1 quart of water per minute at a
supply pressure of between 20 and 120 pounds psi.
To check for proper water flow:
1. Reconnect the water supply tube to the inlet side of
the water valve.
2. Attach a tube to the outlet side of the water valve.
Place the other end of tube in a quart jar held over
a pan to catch any overflow.
3. Attach a 120 volt test cord to terminals.
4. Supply power to water valve for 1 minute. During
this time, one quart of water should flow into jar. If
not, check wire mesh and flow washer for obstruc-
tion, then disassemble water valve.
NOTE:
When reassembling the flow washer, note that
the side of the washer with lettering must face away
from the body of the valve.
Figure 4-19. Condenser Fan
Figure 4-20. Water Inlet Valve
Figure 4-21. Exploded View of Water Inlet Valve
Screw
Coil
Bracket
Guide
Armature
Diaphragm
Body
Spring
Flow Washer
Retainer
Screen
Screw
80 Mesh Screen
Valve Body
Condenser Fan