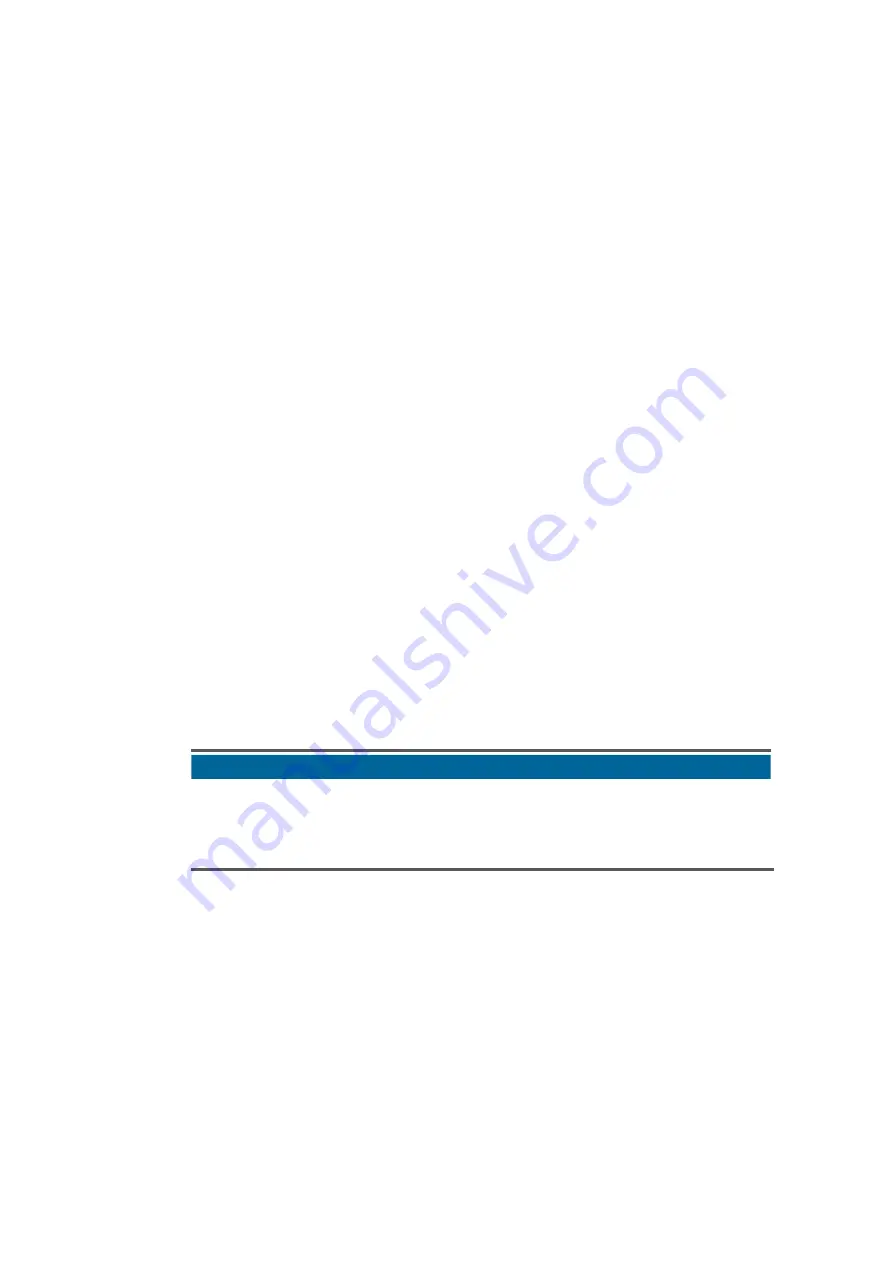
WDE
53
© STULZ SpA . – all rights reserved EN/36B/08.2018
The soft start is installed inside the e-box on the supply line to the compressor. Its purpose is the
reduction of compressor starting current. This can be obtained in two ways:
• Soft start is the most common method of starting. The initial torque setting is DIP switch
selectable as a percentage of the locked rotor torque (LRT), ranging from 15…65% of full value.
The starting time is customer set, ranging from 2…15 seconds.
• Current limit start is used when a limitation of the maximum starting current is necessary. This is
DIP switch selectable and can be adjusted from 150…450% of full load amps. The current limit
starting time is customer set, ranging from 2…15 seconds.
• Other operation modes of this device are kick start and soft stop, but these must be disabled for
the control of the air conditioner.
Additional features:
• Motor overload: The overload is DIP switch selectable. The overload trip class is selectable for
OFF or a 10, 15, or 20 protection. A current transformer (CT) monitors each phase. The motor’s
full load current rating is set by a potentiometer. The overload reset option can be operated either
manually or automatically.
• Fault indication: this device monitors both the pre-start and running modes. A single LED is used
to display both RUN/ON and FAULT indication. If the controller senses a fault, it shuts down the
motor and the LED displays the appropriate fault condition. The controller monitors the following
conditions:
-Overload
-Over-temperature
-Phase reversal
-Phase loss / Open load
-Phase imbalance
-Shorted SCR
Any fault condition will cause the auxiliary contacts to change state and the hold-in circuit to
release. All faults can be cleared by either pressing the reset button or by removing control power.
Overload and over-temperature are time-based conditions that may require waiting for some
additional cooling time, before reset is possible.
Control terminal description
The device contains eight control terminals on the front of the controller. These control terminals are
described below.
Terminal number Description
Terminal number Description
A1
Control power input
97
N.O. relay - aux. contact for fault indication
A2
Control power common
98
N.O. relay - aux. contact for fault indication
IN1
Start input
13
N.O. auxiliary relay #1 (normal/up-to-speed)
IN2
Stop input
14
N.O. auxiliary relay #1 (normal/up-to-speed)
Auxiliary contacts
Two hard contacts are provided as standard. These contacts are finger safe. The first contact is
for fault indication. The auxiliary relay #1 is programmable via dipswitch #14, for normal/up-to-
speed indication. A side-mounted additional auxiliary relay #2 can be added as an accessory and
programmed via dipswitch #15 for normal/up-to-speed indication.