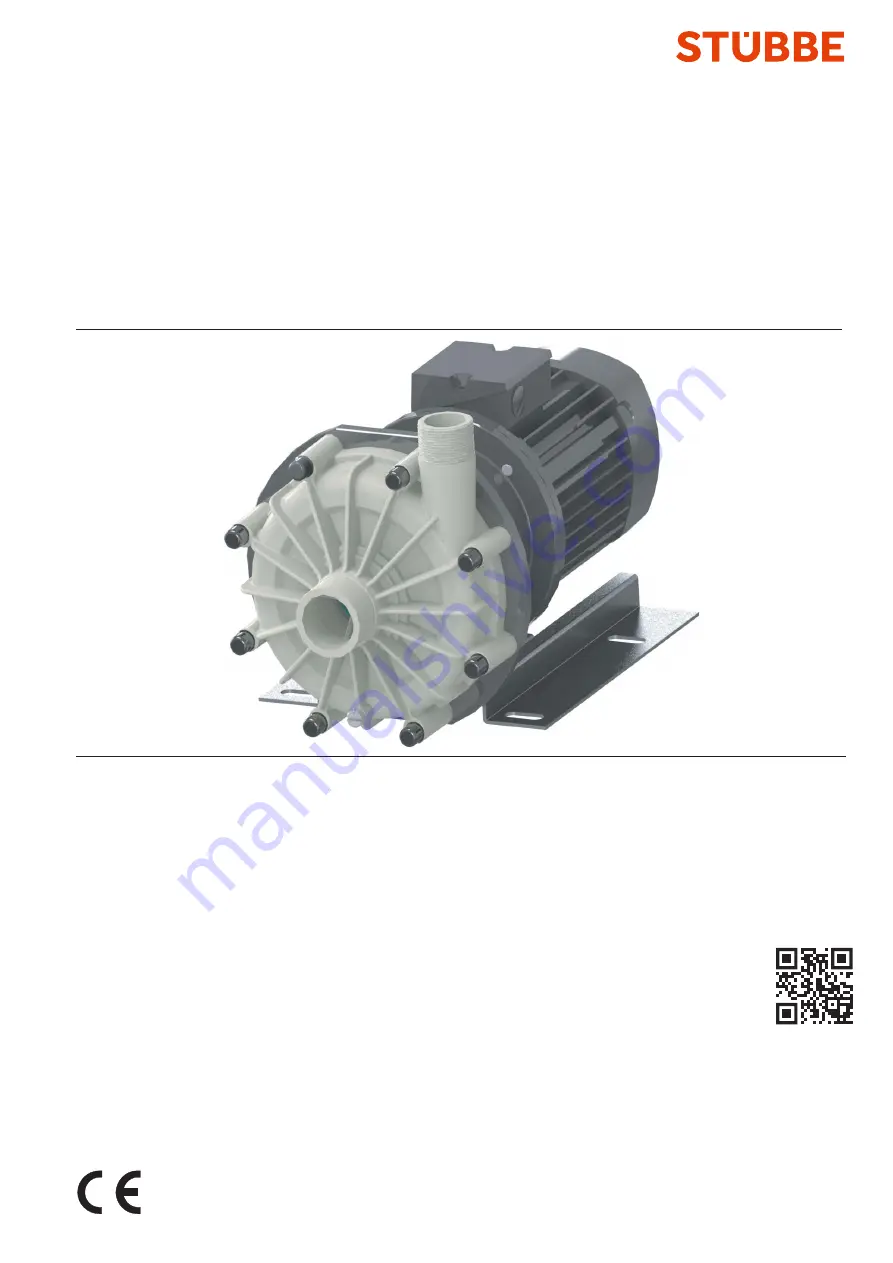
Magnetically driven spiral
cased centrifugal pump
Original operating manual
Series SHM
Version
BA-2018.08.21 EN
Print-No.
300 092
TR MA DE Rev004
STÜBBE GmbH & Co. KG
Hollwieser Straße 5
32602 Vlotho
Germany
Phone: +49 (0) 5733-799-0
Fax: +49 (0) 5733-799-5000
E-mail:
Internet:
Subject to technical modifications.
Read carefully before use.
Save for future use.