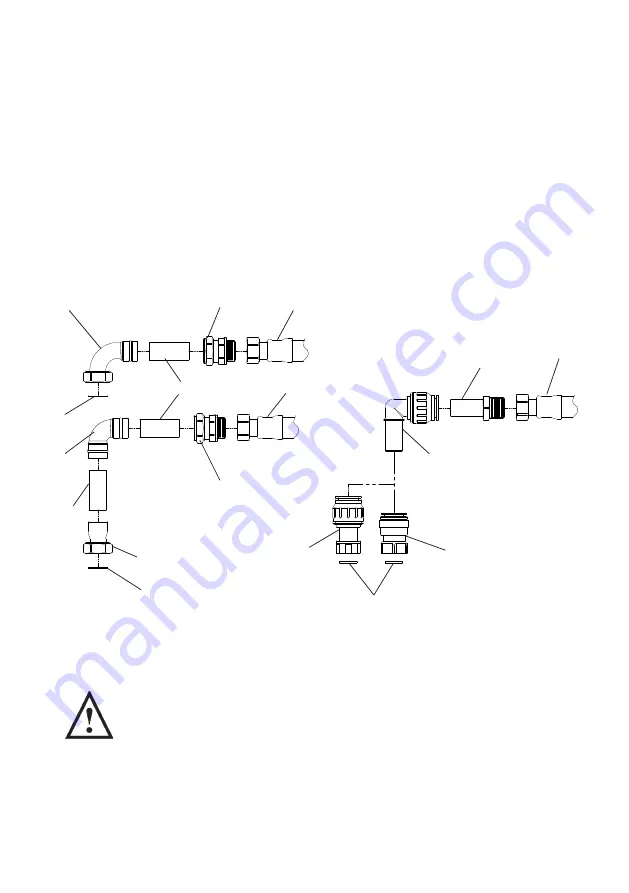
- 12 -
Cont ...
3.13
Typical Low Level Installation:
In certain installations it may be necessary to install a 90° bend on the inlet or
outlet connections of the pump before the flexible hose to accommodate a low
level installation.
Below are some preferred connection options. All connections seal on the pump
body using a fibre or rubber sealing washer. Tap connector fittings should be
used which must be of an appropriate pressure and temperature rating.
It is essential when using any of the fittings shown below, that a correct water
tight seal is obtained between the pump body and selected fitting and also
the flexible hose and selected fitting. If in doubt contact the fitting manufacturer
and confirm compatibility with the connection to be sealed.
Carefully check connections and pipework for leaks whilst pump running and
stationary before leaving the installation unattended.
If you have any concern either about using push-in fittings or should the
joint leak on final test isolate the water supplies and contact PumpAssist on
+44 (0) 800 31 969 80.
For applications in ROI pipe sizes above should read 21 mm.
Fig. 9
G¾ female x 22 mm
elbow tap connector.
Fibre washer.
22 mm
elbow.
22 mm
copper
pipe
Fibre washer.
G¾ female x 22 mm
tap connector.
22 mm compression to
G¾ male.
22 mm copper pipe.
G¾ female flexible hose
(supplied in kit).
22 mm compression to
G¾ male.
G¾ female flexible hose
(supplied in kit).
22 mm to G¾
male.
G¾ female
flexible hose
(supplied in
kit).
22 mm stem elbow.
G ¾ female x 22 mm tap
connector with flush central spigot
and rubber sealing washer fitted
directly to the pump terminals.
Sealing washer (sometimes
captured in fitting)
G ¾ female x 22 mm
swivel tap connector
with flush central
spigot and rubber
sealing washer fitted
directly to the pump
terminals.