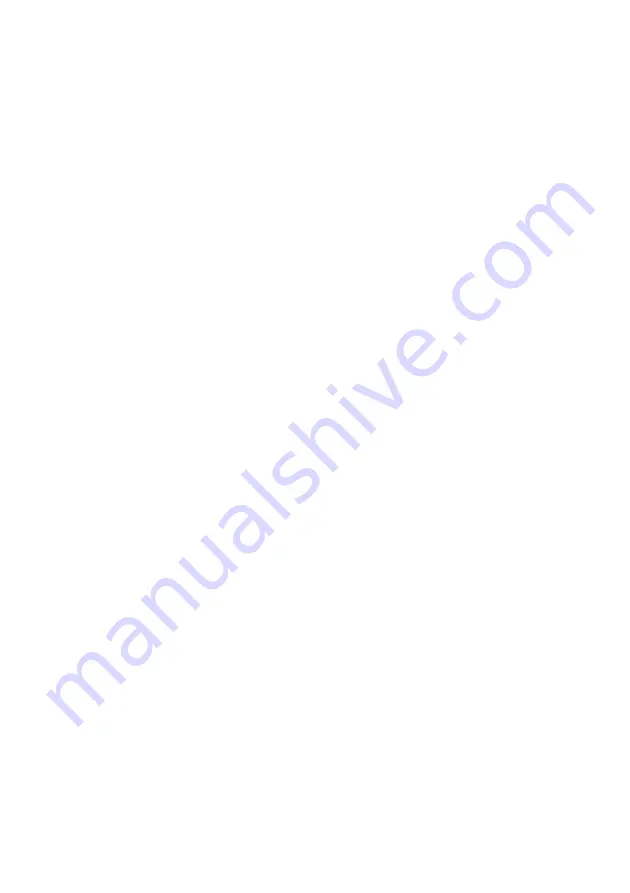
21
VIEW MODE
NORMAL
There are 2 view modes to choose:
- NORMAL: it is visualized “P LINE” (real pressure of the installation) and “INPUT P”
(configured pressure).
- SERVICE: it is visualized “Hz” (working frequency of the inverter), “REF”
(configured pressure), “PRESS” (real pressure of the installation) y “FL” (flow sensor
state).
SERIAL CONTROL
SLAVE
The iMATIC controller is configured by default as “SLAVE”.
In case of individual assembly just confirm “
SLAVE
” by pressing
ENTER
.
In case of group assembly (M-S), we will do the same for the slave device. For the
“
MASTER
” device we will change “
SLAVE
” by “
MASTER
” pressing
.
In the case of twin controller systems, change “
SLAVE
” by “
SWITCHER
” pushing
twice.
DIRECTION
CH 1
To set the communication channel. Press
ENTER
.
P LINE INPUT P
00.0 bar 00.0
After pressing
ENTER
, the system will remain configured showing the type of view
chosen in the previous section, Press
AUTOMATIC
in order to quit manual mode.
In case of group assembly press
AUTOMATIC
only in the device configured as
MASTER
.
In case of group assembly, after pressing
AUTOMATIC
in the
MASTER
device, the
AUTOMATIC LED LIGHT
of the
SLAVE
device will start to flash intermittently,
indicating that communication between both devices is ready. If this does not
happen verify the connection (fig 9).