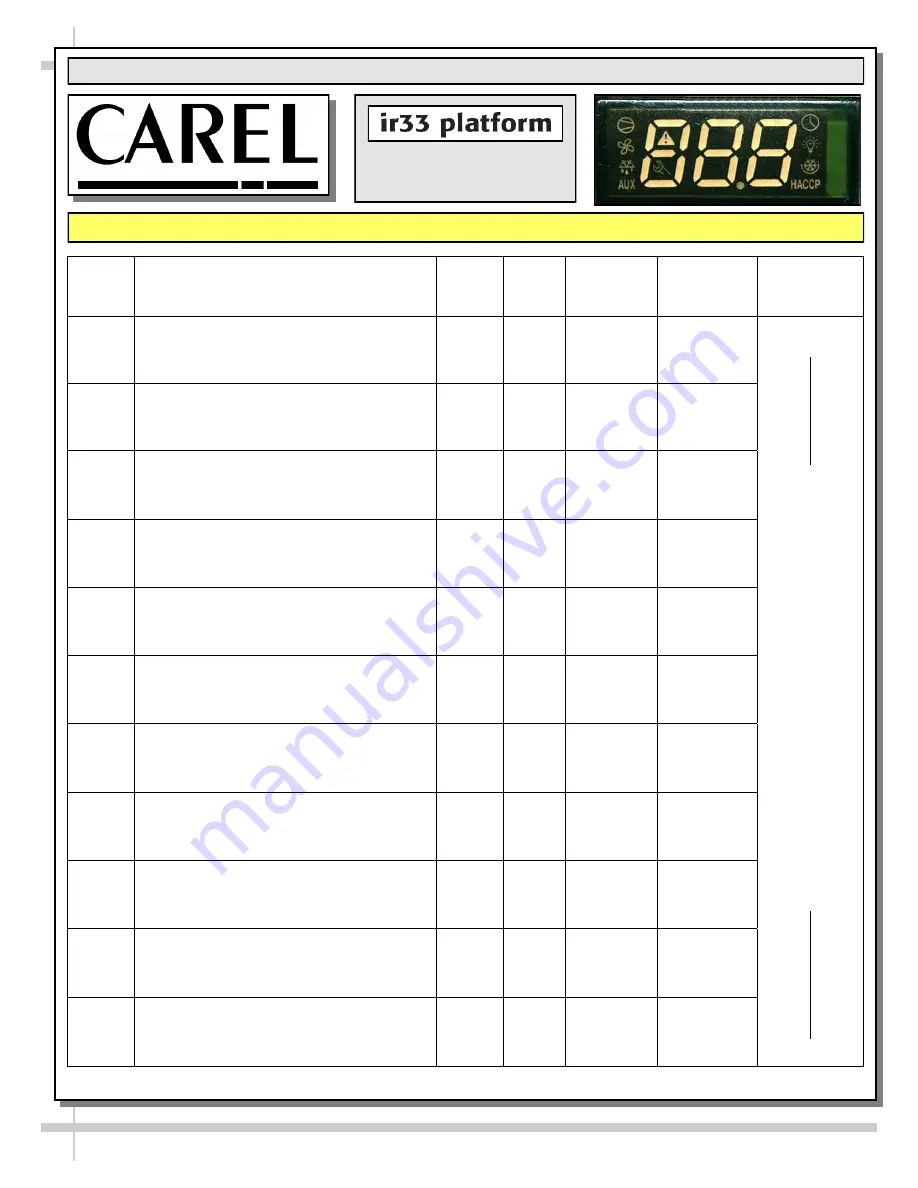
CODE
PARAMETER
UOM* TYPE MINIMUM MAXIMUM
DEFAULT
/5
Select Celsius (°C) or Fahrenheit (°F)
flag
C
0
1
/c1
Calibration of probe 1
°C/°F
C
-20
20
/c2
Calibration of probe 2
°C/°F
C
-20
20
St
Temperature set point
°C/°F
F
r2
r1
rd
Control delta
°C/°F
F
20
0.1
dl
Interval between defrosts
hours
F
0
250
dt1
End defrost temperature, evaporator
°C/°F
F
-50
200
dP1
Maximum defrost duration, evaporator
min
F
1
250
d6
Display on hold during defrost
-
C
0
2
dd
Dripping time after defrost
min
F
0
15
d/1
Display of defrost probe 1
°C/°F
F
-
-
21
For Case
Specific
Defaults
See Serial
Label
Located
Near
Electrical
Access
On Your
Case.
For
Additional
Technical
Information
Call
Structural
Concepts
Technical
Service
Dept. at
1(800)
433.9489
* Unit Of Measure
Read And Save These Instructions - Page 3 of 3
Integrated Electronic
Microprocessor Controller
Summary Table of Operating Parameters