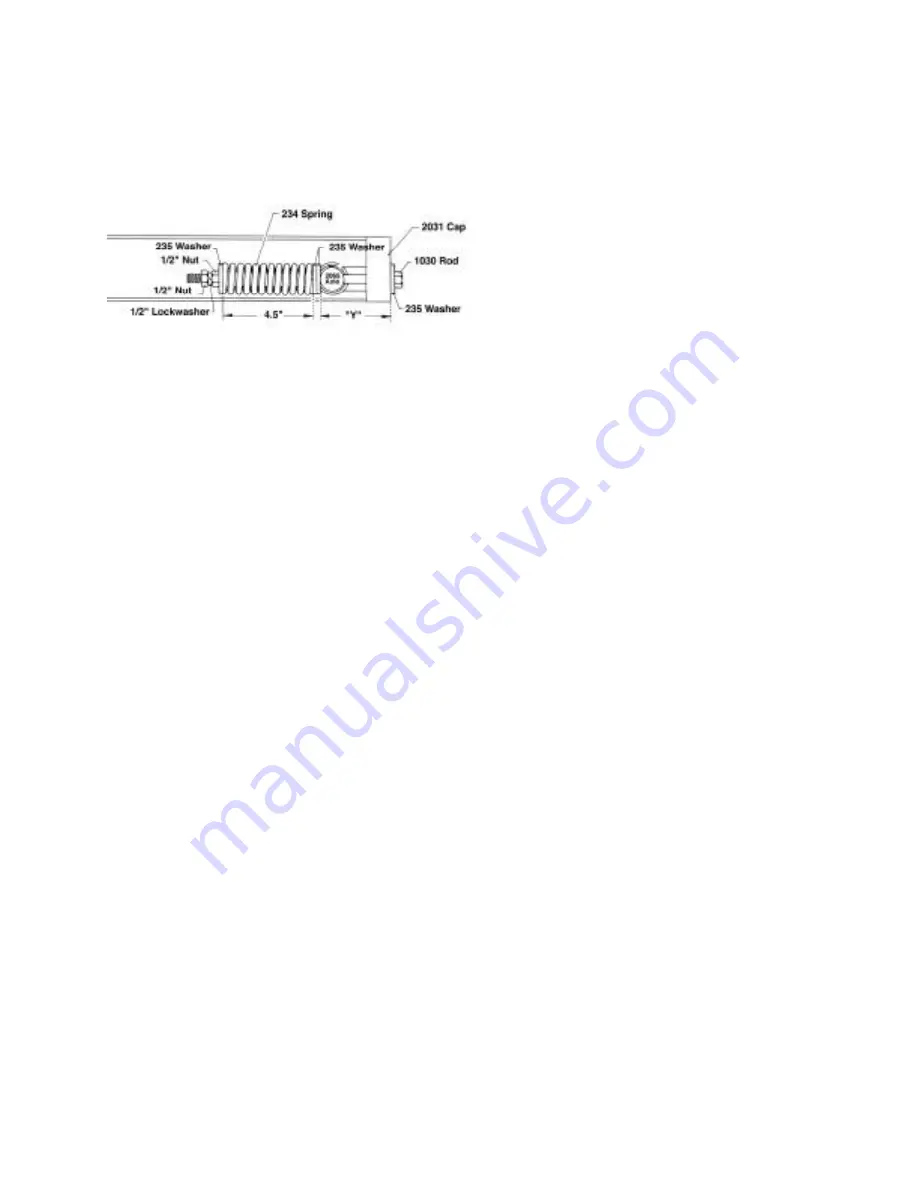
Rotate (clockwise or counter-clockwise) the nut
end of each #1030 Tension Rod so that its
respective #236 Washer (next to #234 Spring) is
drawn forward (or released rearward) thereby
setting its respective #234 Spring to a final length
of 4.5".
Work from left side to right side of Crawler
tightening each Spring 1/4" at a time until you
have achieved a 4.5" overall length for both
Springs. [Measure Spring length only].
At this time remount and safely restart your
Crawler. Drive it approximately 25 feet forward
and then go in reverse, back to your starting point.
Shut off the engine, set Brake and dismount.
Check the overall length of your #234 Springs for
any changes in length. Readjust to proper 4.5"
overall length if necessary. When satisfied,
secure each 1/2" Nut (on threaded end of each
#1030 Tension Rod) with a 1/2" Lock Washer and
a second 1/2" Nut...tighten.
NOTE
: Over time your track assemblies may
stretch. This can result in unstable track
alignment and “throwing” tracks. To remedy
this it may be necessary to compress the #234
Springs to a dimension smaller than 4.5
inches. Care should be taken not compress
beyond 4.25 inches as this will not leave
adequate room for compression during heavy
loading situations. Care must also be taken at
all times to assure that both springs are
compressed equally.
FOOTREST ADJUSTMENT
Right & Left Footrests (L) are adjustable in three
positions front to rear. To adjust, remove the three
3/8" Cap Screws holding each Footrest. Relocate
Footrest to its new position by aligning the two
3/8" slots in lower lip of Footrest with a mating set
of two 3/8" holes in floor of its respective Fender.
Locate the third 3/8" slot (in side lip of each
Footrest) with closest mating 3/8" wide vertical
slot in Crawler's body wall. From outside, insert
3/8" Cap Screws into the above mating holes and
slots; secure inside with 3/8" Locknuts.
SEAT LOCATION
The Seat and its associated "track assembly" can
be located in three positions (front to rear) on the
Cover assembly. To change Seat location,
release Seat Latch and using the Seat as a
handle, rotate the Seat/Cover Assembly rearward
until it hits its stop.
Inside the Cover, remove the four 5/16" Nuts and
Lock Washers holding the Seat's track assembly's
threaded studs in place. Let the Seat and its track
assembly drop away from the Cover...protect the
wires connecting the Seat Switch!
Reinsert the threaded studs of the track assembly
into one of the three new "hole patterns" you have
selected on outside of Cover. Secure inside
Cover with original 5/16" Nuts and Lock Washers.
[Make sure Seat Switch wires are back in place
and that the Seat can slide forward and back
without pinching the wires.]
Close Seat/Cover Assembly and secure Seat
Latch.