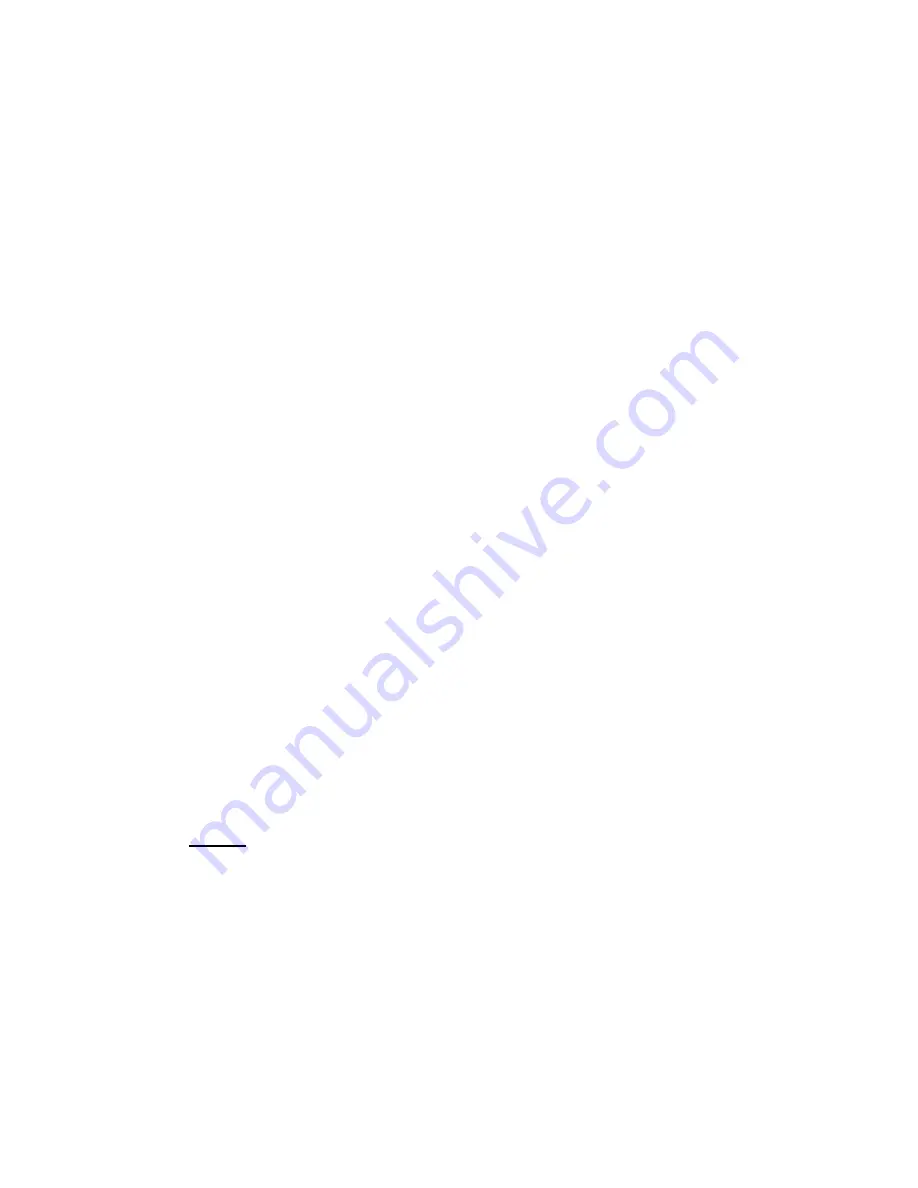
19
entered the mixer or without the mixer paddles turning. Doing either of these two operations
will cause extreme loading of the mixers electrical motor and power train.
5.
After all bags have been emptied into the mixer, add the remainder of the after slowly until
the correct material consistency is obtained.
6.
When the mixer is thoroughly blended and air entrained (2-3 minutes after last bag of
material is dumped), the mixer door should be opened to allow the mixed material to gump
into the pump hopper.
7.
The mixer should be left running continuously. The mixing action of the paddle blades will
force remainder of mixed material out of the discharge door.
8.
After all material is discharged to the holding hopper, close door, spray with wash down hose
& nozzle, begin mixing a new batch (Step #1).
9.
Turn the pump control switch to FORWARD. The material level in the hopper is designed to
a specific volume that will allow continuous operation of the mixer. As one batch is mixed
another is being pumped. However, before the pump hopper is completely empty, the batch
in the mixer should be discharged to keep the pump from running dry. If for any reason the
required mixing time is greater than the required pumping time, turn the pump controls to
OFF before the pump runs completely out of material. Running the pump dry can cause
damage to the stator in a matter of seconds.
10.
The hose and hopper should be monitored periodically to make sure that the hose is not
plugged. If the level in the hopper stops falling, the material hose becomes very firm and no
material is flowing from the end of the hose, the hose is plugged. Turn the pump to
REVERSE immediately until the hose becomes soft again.
Caution
: Only after the pump has been reversed and the hose is soft again should the hose
be uncoupled and the plug removed.
11.
If a void is desired at the top of the tank’s annulus, this is easily accomplished. First, fill the
tank completely using the standard procedure. Next, place the pump in reverse to suck
material back from the tank. Make sure that material is continuously flowing back to the