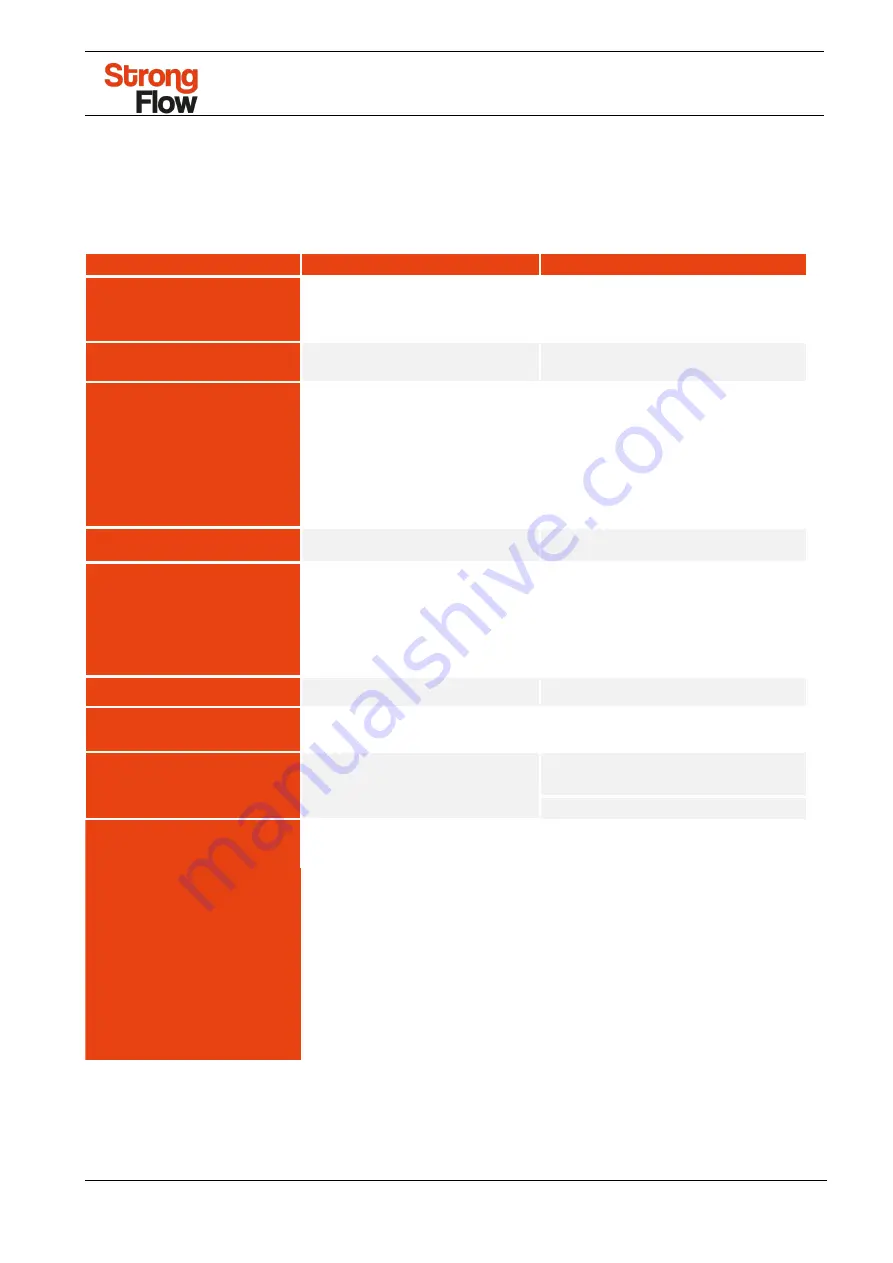
Operating and maintenance
instructions
AG-250/330 water softeners
Sivu 18/22
StrongFlow Oy
Tel. +358 20 730 1820
Domicile: Kaarina
Ahokylänkatu 3
www.strongflow.fi
Business ID: 2024125-8
FI-20780 Kaarina
VAT no: FI25511181
6.3 Possible problems and causes
Problem
Possible cause
Solution
a. Uncontrolled brine refill flow rate
a. Remove brine control to clean ball and seat
b. Air leak in brine to air check
b. Check al connections in brine line for leaks.
Refer to instructions.
c. Drain control clogged with resin or other debris c. Clean drain control
Flowing or dripping water at
a. Valve stem return spring weak
a. Replace spring. (Contact dealer)
drain or brine line after regeneration
b. Debris preventing valve disc from closing
b. Remove debris
a. Low water pressure
a. Make correct setting according to instructions.
b. Restricted drain line
b. Remove restriction.
c. Injector plugged
c. Clean injector and screen.
d. Injector defective
d. Replace injector and cap. (Contact dealer)
e. Valve disc 2 and/or 3 not closed.
e. Remove foreign matter from disc and check
disc for closing by pushing in on stem.
Replace if needed. (Contact dealer)
f. Air check valve prematurely closed
f. Put control momentarily into brine refill, C8.
Replace or repair air check if needed
a. AC adapter or motor not connected
a. Connect power
b. Defective adapter or motor
b. Replace adapter/motor. (Connect dealer.)
Brine tank overflow
Control will not draw brine
Control will not regenerate automatically
a. Improper regeneration
a. Repeat regeneration after making certain
correct salt dosage was set.
b. No salt in regenerant tank
b. Add salt
No conditioned water after
c. Injector or screen plugged
c. Clean injector and screen.
regeneration
d. Air check valve closes prematurely
d. Put control momentarily in brine/slow rinse, C2
Replace or repair air check if needed
(Contact dealer.)
Water taste salty
Regeneration does not work normally
Check brine draw and time of regeneration.
Control power has been connected and the
control is not sure of the estate of the operation.
Disconnect and reconnect the power. If problem
persists, obtain the appropriate controller or AC
adapter for either 50 or 60 Hz power.
a. Controller does not know the position of the
a. Wait for two minutes fot the controller to return to
camshaft. Camshaft should be rotating to find
home position. The hourglass should be flashing on
home position.
the display indicating the motor is running.
b. Check that motor and optical sensor is connected.
Verify that motor wire harness is connected to motor
and controller module. Verify that motor gear has
engaged can gear. If everything is connected try
replacing in this order:
wire harness, motor, optical sensot, controller.
c. Camshaft is turning for more than five
c. Verify that optical sensor is in place and connected
minutes to find position
to wire. Verify that camshaft is connected appropriately.
Verify that no dirt or rubbish is clogging any of the cam
slots. If motor continues to rotate indefinitely, replace
the following components in this order:
wire harness, motor, optical sensot, controller.
ERR 2 is displayed
b. Camshaft is not turning during ERR3 display.
ERR 3 is displayed
Control power does not match 50 or 60 Hz
Press the UP arrow and the control should reset.
ERR 1 is displayed