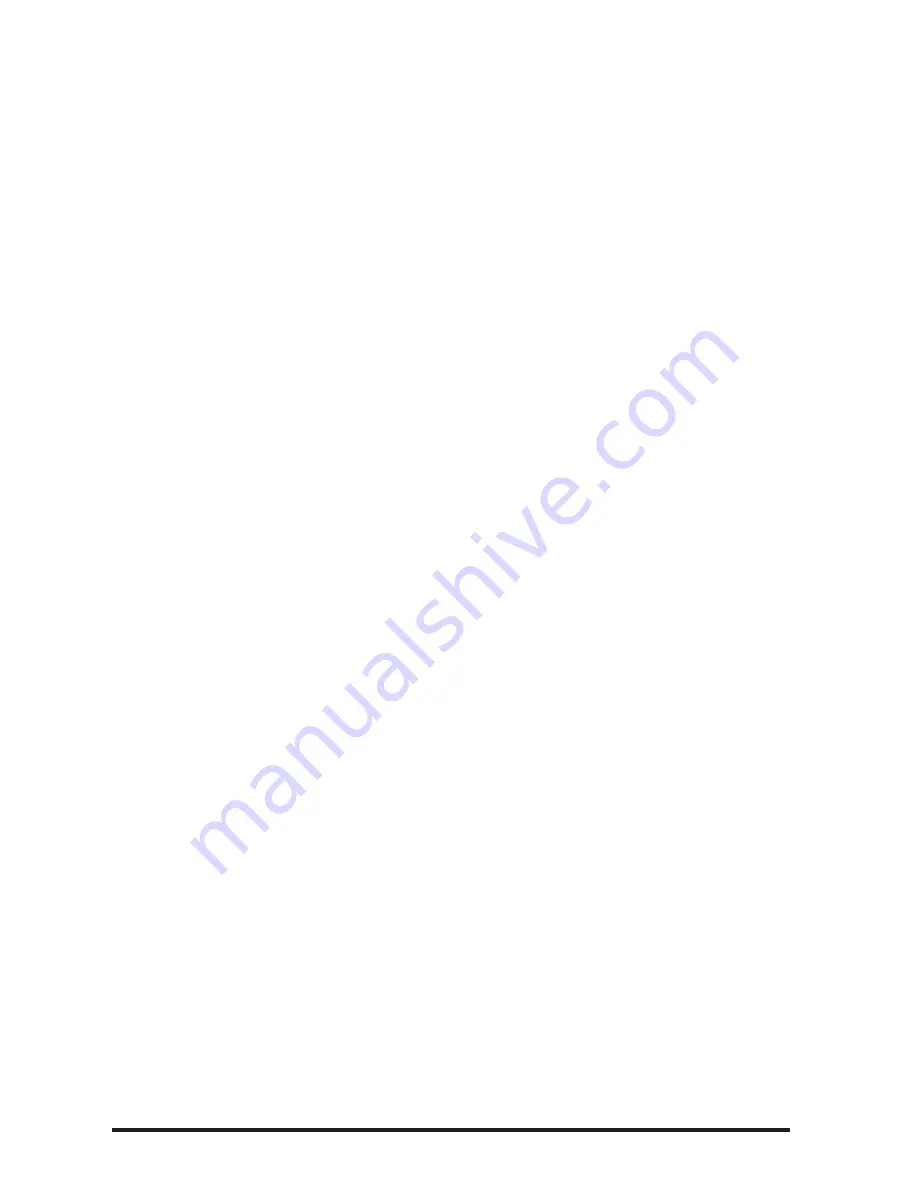
Page iv
PocketMIKE Operating Manual
5. Use of Couplants
Operators must be familiar with the use of ultrasonic couplants. Testing
skills must be developed so that couplant is used and applied in a
consistent manner to minimize variations in couplant layer thickness
and errors in test results. Calibration and actual testing should be
performed under similar coupling conditions, using a minimum amount
of couplant and applying consistent pressure on the transducer.
6. Doubling
Ultrasonic thickness gauges will, under certain conditions, display
readings which are twice (or, in some cases, three times) the actual
material thickness being measured. This effect, commonly known as
“doubling,” can occur below the minimum specified range of the
transducer. If the transducer being used is worn, doubling is possible at
a thickness greater than the minimum of the specified range.
When using a new transducer, any reading which is less than twice the
minimum specified range of the transducer may be a “doubled” read-
ing, and the thickness of the material being tested should be verified by
the use of other methods. If the transducer shows any sign of wear,
doubling may occur at a thickness greater than twice the minimum of
the specified range. This thickness should be determined by calibrating
the PocketMIKE on reference blocks that represent the complete range
of possible thicknesses that may be encountered in testing. This is
particularly important when the test piece is being ultrasonically
measured for the first time or in any case where the history of thickness
of the test specimen is unknown.
Physics of Ultrasound
These instruments operate on the ultrasonic pulse-echo principle,
similar to sonar. A short ultrasonic pulse is transmitted into the part by a
probe (transducer). The pulse travels through the material under test
until it encounters an interface, that is a material with substantially
different physical characteristics, such as air or liquid, at the back
surface of the part. At the interface, the pulse is reflected back to the
probe.
Page iv
PocketMIKE Operating Manual
5. Use of Couplants
Operators must be familiar with the use of ultrasonic couplants. Testing
skills must be developed so that couplant is used and applied in a
consistent manner to minimize variations in couplant layer thickness
and errors in test results. Calibration and actual testing should be
performed under similar coupling conditions, using a minimum amount
of couplant and applying consistent pressure on the transducer.
6. Doubling
Ultrasonic thickness gauges will, under certain conditions, display
readings which are twice (or, in some cases, three times) the actual
material thickness being measured. This effect, commonly known as
“doubling,” can occur below the minimum specified range of the
transducer. If the transducer being used is worn, doubling is possible at
a thickness greater than the minimum of the specified range.
When using a new transducer, any reading which is less than twice the
minimum specified range of the transducer may be a “doubled” read-
ing, and the thickness of the material being tested should be verified by
the use of other methods. If the transducer shows any sign of wear,
doubling may occur at a thickness greater than twice the minimum of
the specified range. This thickness should be determined by calibrating
the PocketMIKE on reference blocks that represent the complete range
of possible thicknesses that may be encountered in testing. This is
particularly important when the test piece is being ultrasonically
measured for the first time or in any case where the history of thickness
of the test specimen is unknown.
Physics of Ultrasound
These instruments operate on the ultrasonic pulse-echo principle,
similar to sonar. A short ultrasonic pulse is transmitted into the part by a
probe (transducer). The pulse travels through the material under test
until it encounters an interface, that is a material with substantially
different physical characteristics, such as air or liquid, at the back
surface of the part. At the interface, the pulse is reflected back to the
probe.
Summary of Contents for PocketMIKE
Page 2: ......
Page 3: ...PocketMIKE Operating Manual version 1 0 ...
Page 4: ......
Page 10: ...Page vi PocketMIKE Operating Manual ...
Page 12: ...Page viii PocketMIKE Operating Manual ...
Page 20: ...Page 8 PocketMIKE Operating Manual ...
Page 28: ...Page 16 PocketMIKE Operating Manual ...
Page 36: ...Page 24 PocketMIKE Operating Manual ...
Page 38: ...Page 26 PocketMIKE Operating Manual ...