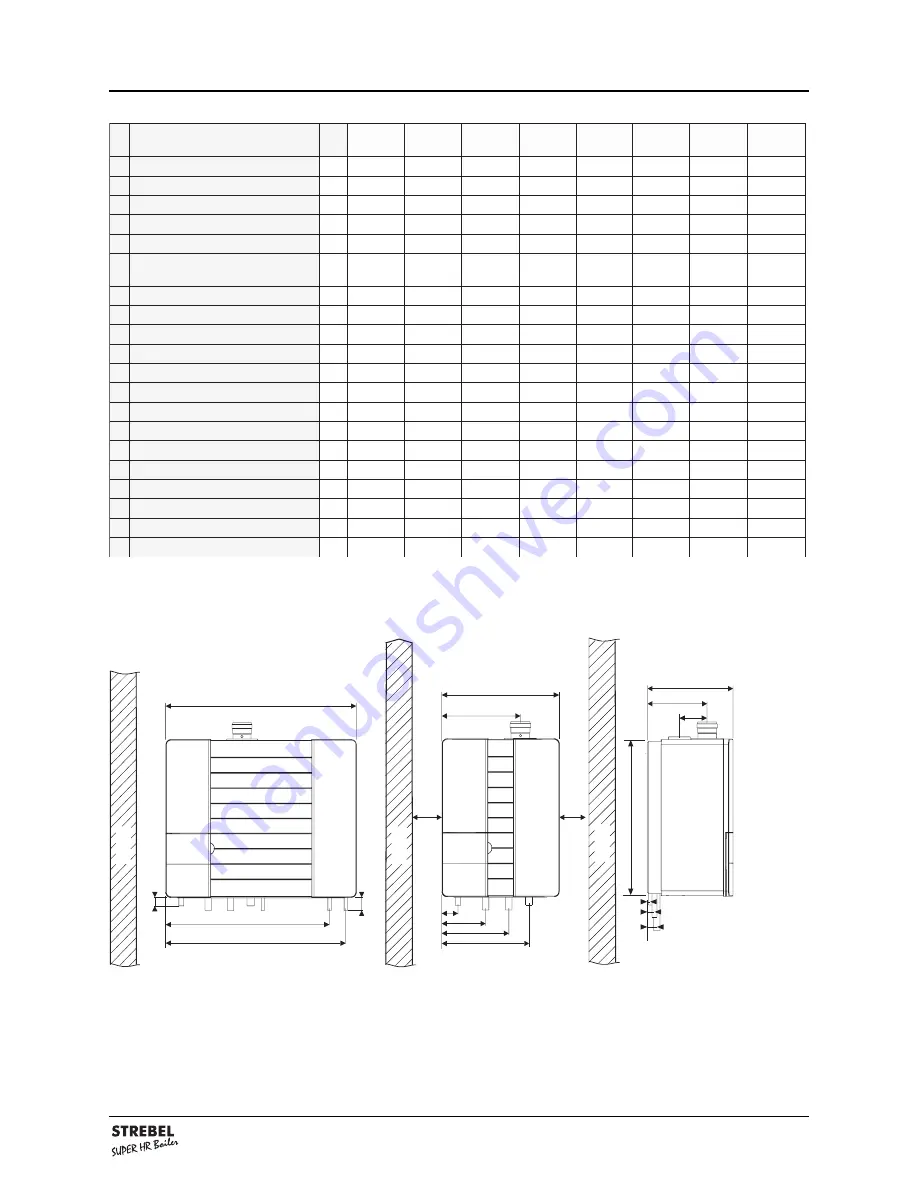
Installation instructions S-HR series page 5
3.1 Dimensions
Dimensions (in mm)
figure 1
wall
C
E
F
A
U
T
S
wall
B
M
N
P
Q
R
B
wall
D
H
J
K
10
50
G
Dimensions
table 1
ti
n
u
f
o
e
p
y
t
R
H
-
S
5
1
R
H
-
S
4
2
R
H
-
S
T
4
2
R
H
-
S
5
3
R
H
-
S
T
5
3
R
H
-
S
1
5
R
H
-
S
T
1
5
R
H
-
S
0
6
A
t
h
g
i
e
h
m
m
0
8
6
0
8
6
0
8
6
0
8
6
0
8
6
0
8
6
0
8
6
0
8
6
B
h
t
d
i
w
m
m
0
0
5
0
0
5
0
4
8
0
0
5
0
4
8
0
6
6
0
0
0
1
0
6
6
C
h
t
p
e
d
m
m
0
7
3
0
7
3
0
7
3
0
7
3
0
7
3
0
7
3
0
7
3
0
7
3
D
t
s
u
a
h
x
e
s
a
g
e
u
lf
/
e
d
i
s
tf
e
l
m
m
5
3
3
5
3
3
5
3
3
5
3
3
5
3
3
5
9
4
5
9
4
5
9
4
E
t
s
u
a
h
x
e
s
a
g
e
u
lf
/
e
r
t
n
e
c
o
t
e
r
t
n
e
c
y
l
p
p
u
s
d
n
a
m
m
0
2
1
0
2
1
0
2
1
0
2
1
0
2
1
0
2
1
0
2
1
0
2
1
F
t
s
u
a
h
x
e
s
a
g
e
u
lf
/
k
c
a
b
m
m
0
7
2
0
7
2
0
7
2
0
7
2
0
7
2
0
7
2
0
7
2
0
7
2
G
e
p
i
p
s
a
g
/
e
d
i
s
tf
e
l
m
m
5
6
5
6
5
6
5
6
5
6
5
6
5
6
5
6
H
e
p
i
p
w
o
lf
/
e
d
i
s
tf
e
l
m
m
5
8
1
5
8
1
5
8
1
5
8
1
5
8
1
5
8
1
5
8
1
5
8
1
J
e
p
i
p
n
r
u
t
e
r
/
e
d
i
s
tf
e
l
m
m
5
8
2
5
8
2
5
8
2
5
8
2
5
8
2
5
4
4
5
4
4
5
4
4
K
e
p
i
p
n
o
it
a
s
n
e
d
n
o
c
/
e
d
i
s
tf
e
l
m
m
0
7
3
0
7
3
0
7
3
0
7
3
0
7
3
0
3
5
0
3
5
0
3
5
L
e
p
i
p
k
n
a
t
n
o
i
s
n
a
p
x
e
/
e
d
i
s
tf
e
l
m
m
0
3
4
0
3
4
0
9
5
M
e
p
i
p
r
e
t
a
w
d
l
o
c
/
e
d
i
s
tf
e
l
m
m
5
2
7
5
2
7
5
8
8
N
e
p
i
p
r
e
t
a
w
t
o
h
/
e
d
i
s
tf
e
l
m
m
5
9
7
5
9
7
5
5
9
P
*
g
f
o
t
h
g
n
e
l
e
p
i
p
m
m
8
1
8
1
8
1
8
1
8
1
8
1
8
1
8
1
Q
*
k
d
n
a
c
f
o
t
h
g
n
e
l
e
p
i
p
m
m
0
4
0
4
0
4
0
4
0
4
0
4
0
4
0
4
R
*
w
d
n
a
e
;
r
;
a
f
o
t
h
g
n
e
l
e
p
i
p
m
m
0
6
0
6
0
6
0
6
0
6
0
6
0
6
0
6
S
*
c
e
p
i
p
f
o
e
r
t
n
e
c
/
k
c
a
b
m
m
5
2
5
2
5
2
5
2
5
2
5
2
5
2
5
2
T
*
g
e
p
i
p
f
o
e
r
t
n
e
c
/
k
c
a
b
m
m
0
4
0
4
0
4
0
4
0
4
0
4
0
4
0
4
U
*
w
;
k
;
e
;
r
;
a
e
p
i
p
f
o
e
r
t
n
e
c
/
k
c
a
b
m
m
0
5
0
5
0
5
0
5
0
5
0
5
0
5
0
5