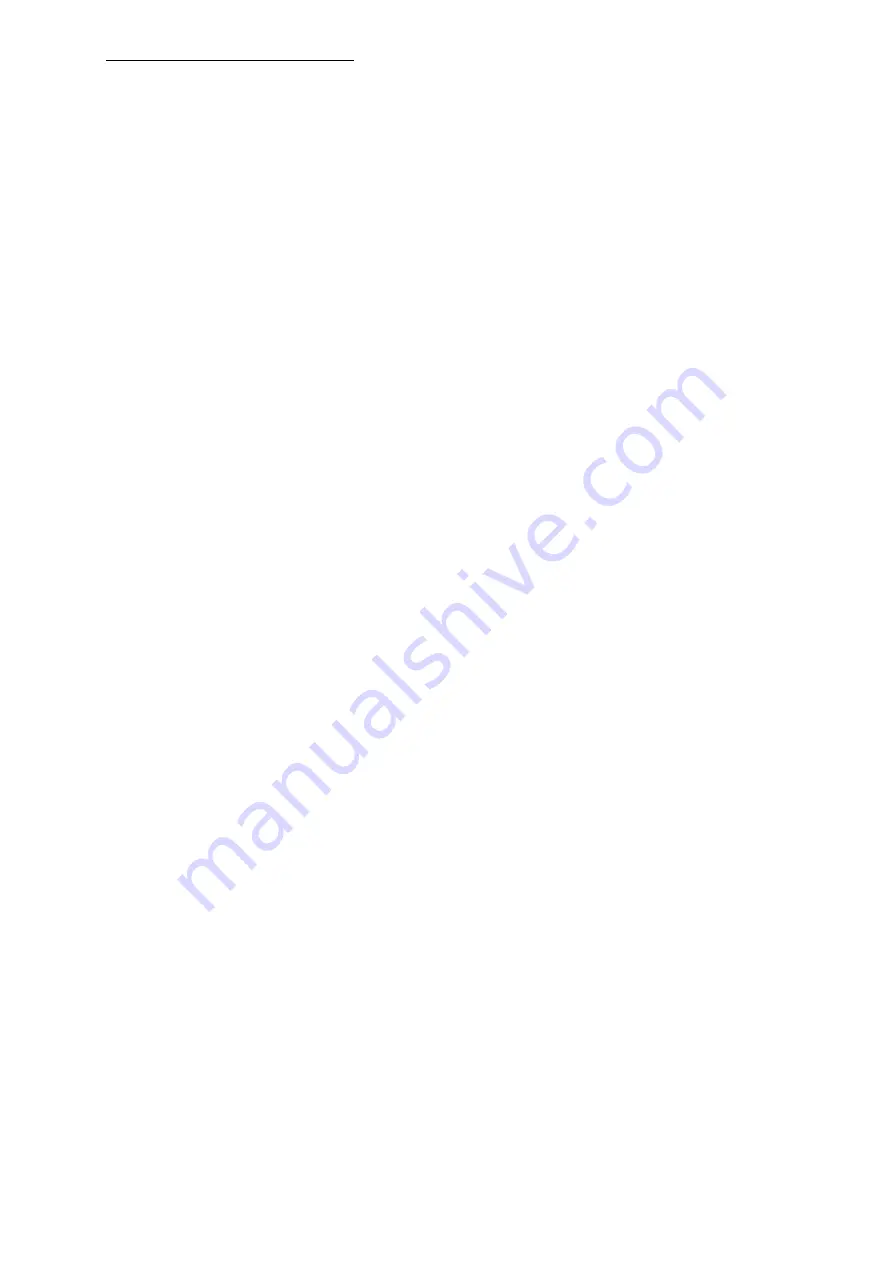
9
9.0
COMMISSIONING AND TESTING
Before commencing to commissioning the boiler, check the following:-
9.1
Electrical
Electrical supply is switched off.
All electrical connections are sound and correctly made.
Electrical system is correctly earthed.
9.2
Gas Supply
Gas supply is purged of air, and tested for soundness as described in BS. 6891 : IGE/UP/2 Gas Installation
Pipework, Boosters and Compressors on Industrial and Commercial Premises.
All appliance gas cocks are turned off.
Gas supply is on at meter.
9.3
Water
Boiler and system have been flushed through and are filled, and circulating pumps operational.
Flow and return valves are open.
9.4
To Test Soundness of Safety Shut-Off Valve
1. Ensure that the main gas cock and electricity supply are turned OFF.
2. Remove plug from pressure test point on inlet side of the safety shut off-valve and connect pressure gauge.
3. Turn ON main gas cock to pressurise the system up to the seat of the safety shut-off valve.
4. Turn OFF main gas cock, leave for two minutes checking for any drop in pressure on the gauge. If any
pressure loss is observed, re-pressurise by opening and closing the main gas cock, and test the assembly
for
leaks using a leak detector solution.
5. If no external leaks are detected and loss of pressure occurs, this is the result of a let-by at the safety shut-
off valve.
9.5
To Light The Boiler
9.5.1
Fully Automatic Models
(see Fig. 2 & 3)
1. Connect pressure gauge to burner pressure test point.
2. Switch on mains electrical supply.
3. Turn ON main gas cock.
4. Depress reset button on limit thermostat to ensure stat is “made”.
5. Set control thermostat to required temperature and push button “I” (on control panel) to the ON position.
6. After switching on, ignition spark should appear, followed by ignition of the main burner at pilot setting .
If
flame is not established control box will lock out in approximately 5 seconds. This may occur in
initial start
due to air in the gas line. The control box may be reset after a delay of approximately 15
seconds by
pressing the red button (B1) on the control panel, the red light should go out.
7. When pilot flame is satisfactory the gas valve will open to main flame.
8. Check main burner pressure (as per TABLE 1).
Adjust burner pressure on gas control if necessary.
Burner pressure should be rechecked after about 30 minutes of operation and adjusted if necessary.
9. Switch Off electrical supply with button “I” (on control panel). Check that main burners are extinguished.
Remove pressure gauge and replace plug in test point.
9.6
All Models
After lighting the boiler as described above, the operation of the thermostat should be checked. All gas lines
should be re-checked for soundness, using a leak detector solution.
The gas rate should be checked at the meter, but unless this differs significantly from the rated heat input
quoted in TABLE 1, the setting pressure given should be maintained.
9.7
LPG
If gas conversion is required refer to Fig. 4.