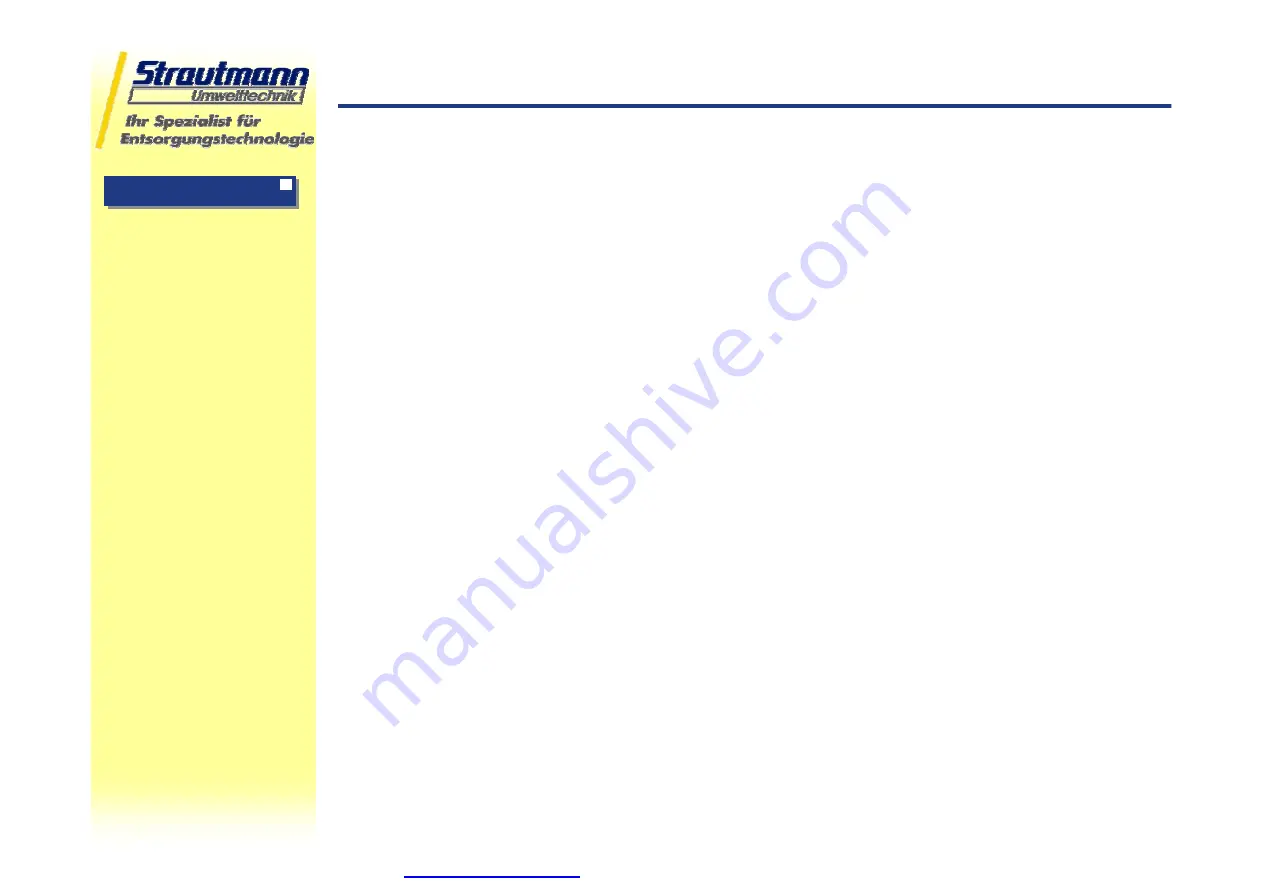
Remedying Faults at PP 1207– Klöckner Möller
Remedying faults PP 1207
page 1 – April 2005
Frequently occurring faults and remedies for them
are explained in the following tables.
The tables are divided up according to main fault areas.
•
Machine has no function
•
Machine does not run in automatic mode
•
Machine does not run in manual mode
•
Bale cannot be ejected
•
Press plate dropping - oil leakage
•
Door does not rise automatically
•
Hydraulic problems
•
Electrical problems
This documentation is also intended for the EK 1107/1109 and
PP 1208
PDF wurde mit pdfFactory-Prüfversion erstellt.